Tundra Prerunner Updates & New OBS F-150 Prerunner Kibbetech
The latest developments at Kibbetech showcase the intricate work being done on a Toyota Tundra, focusing on its suspension and structural modifications. The front section of the Tundra is being meticulously crafted with extensive tube work to accommodate shock mounts and ensure there are no interference issues with the tires during full steer and bump. This process includes using a fixture that bolts onto the steering box and tubes, thereby establishing the location for the shock mount. Precise laser-cut tubes, matching those used in the tube chassis truck, are integrated into the design, ensuring a seamless and efficient build process. The bump mount area will be established once all welding is completed, with careful attention to the timing of the bump stop to avoid premature bottoming out.
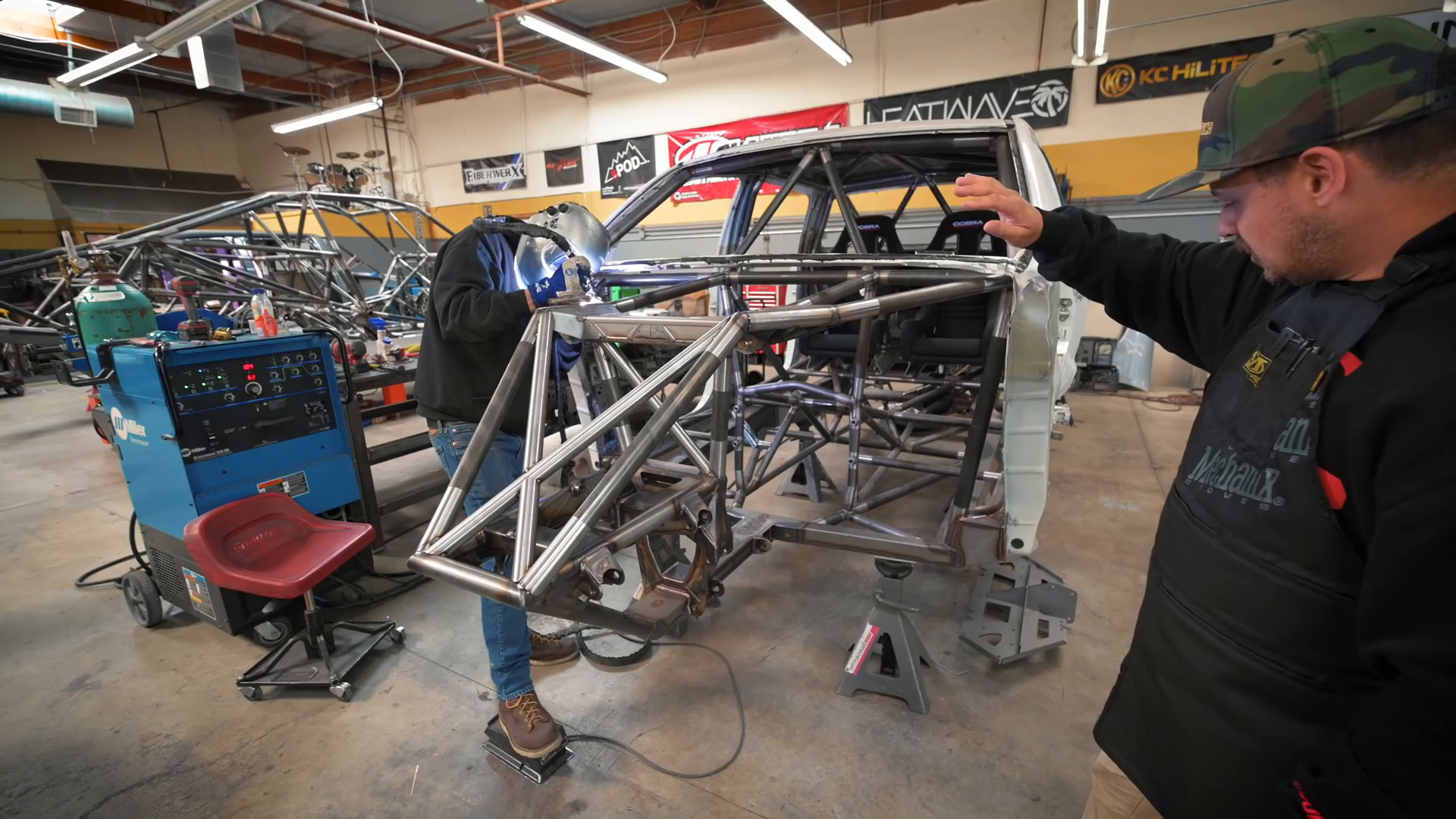
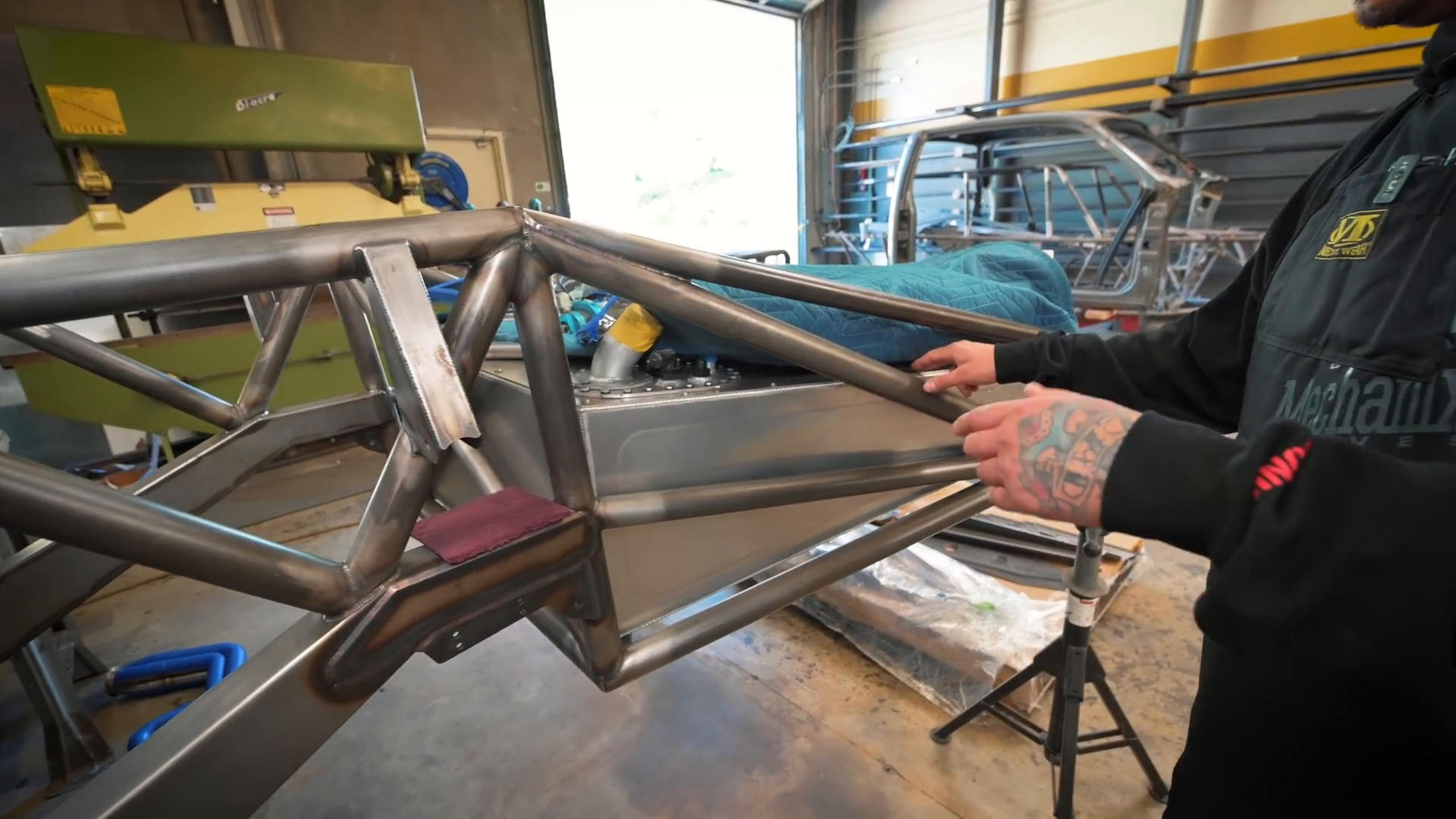
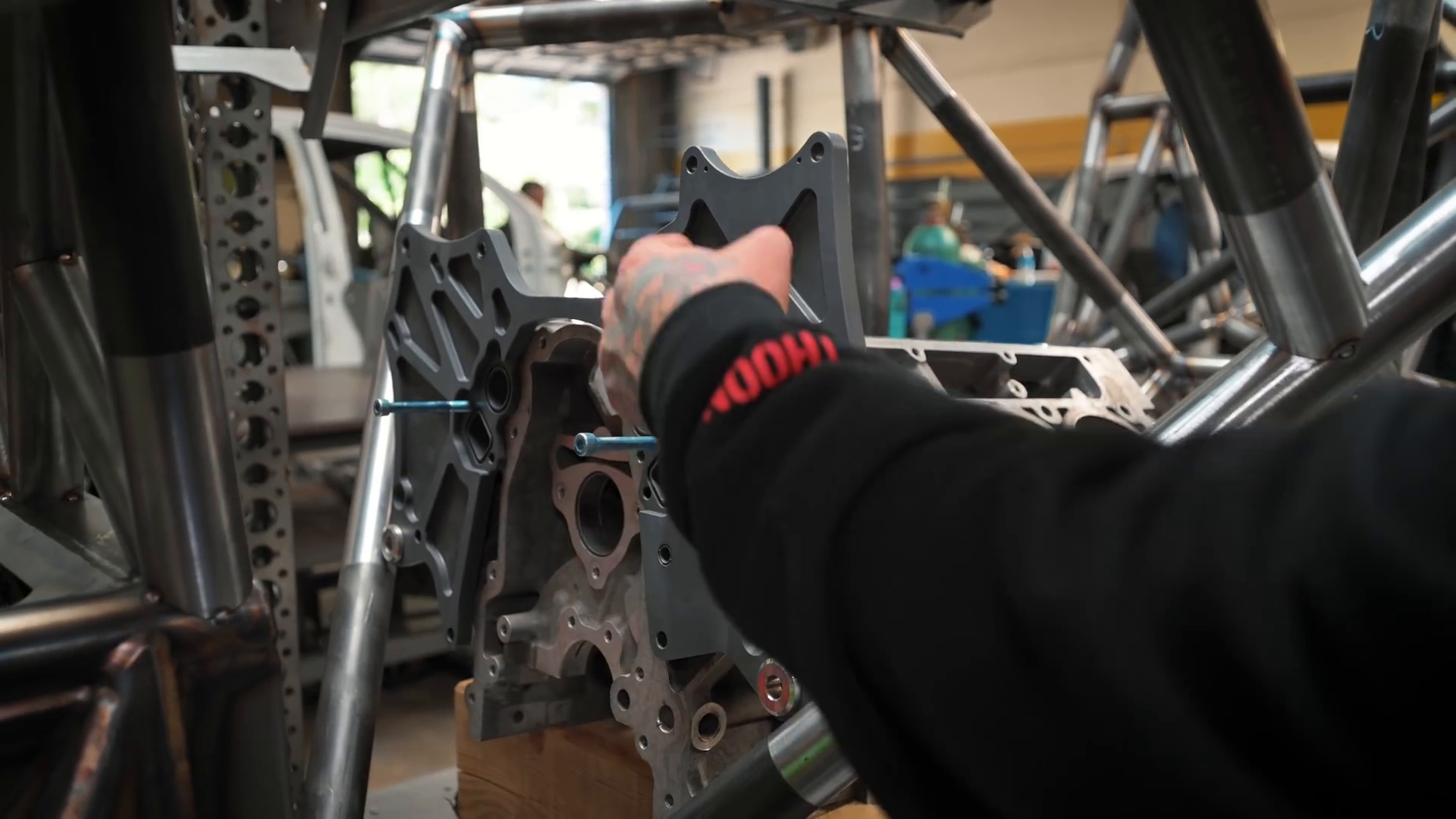
Sheet Metal Work and Electronics
Dashboard Fabrication
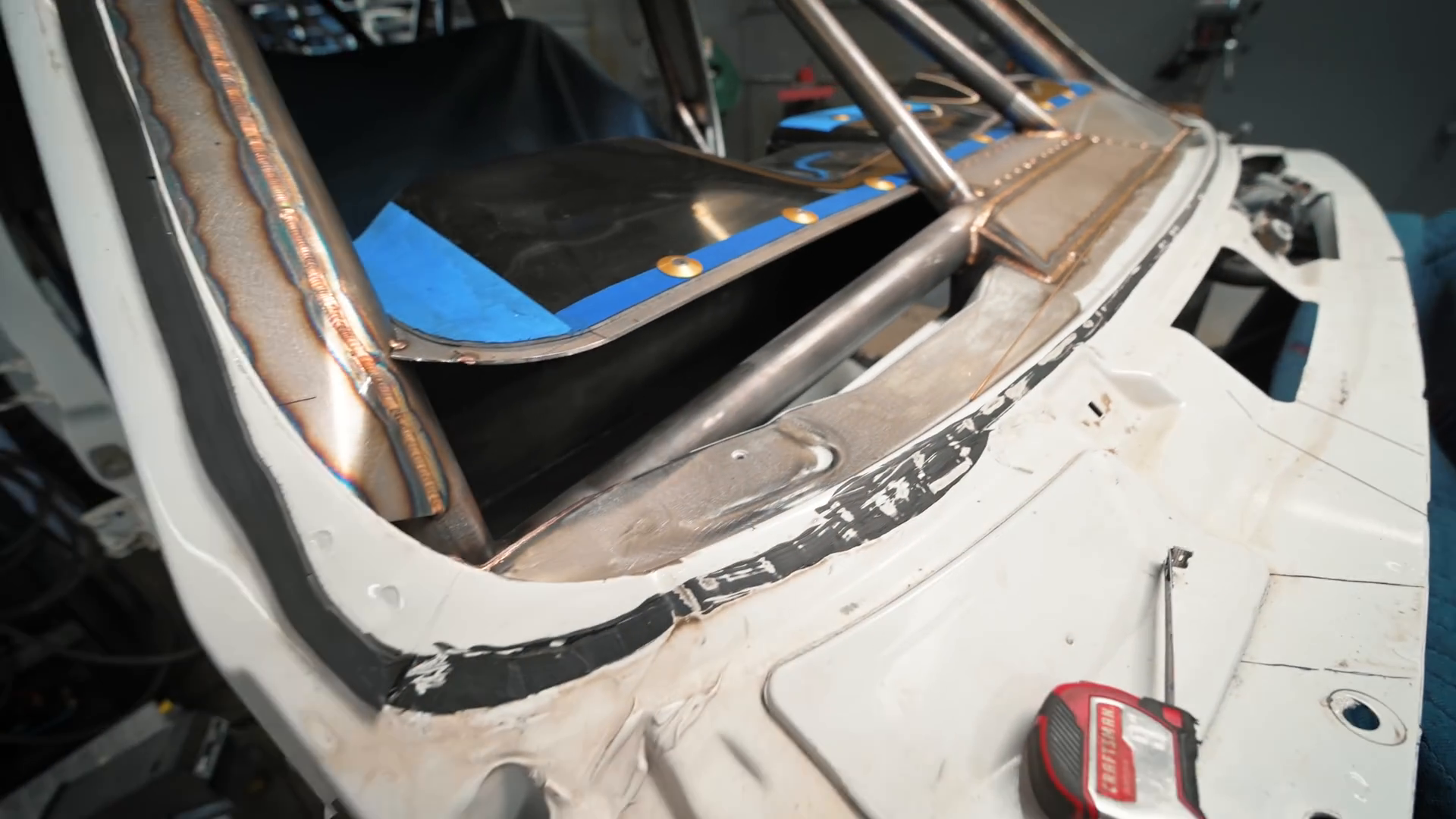
In the fabrication phase, significant progress is being made on the sheet metal work for the dashboard. A challenge arose in creating a seamless, one-piece dash extending to the vehicle’s forward section. The solution involves employing sheet metal, which will be welded and blended before being upholstered to form a neat seam. The dashboard will be bolted on separately, supported by a robust frame structure, ensuring durability and functionality.
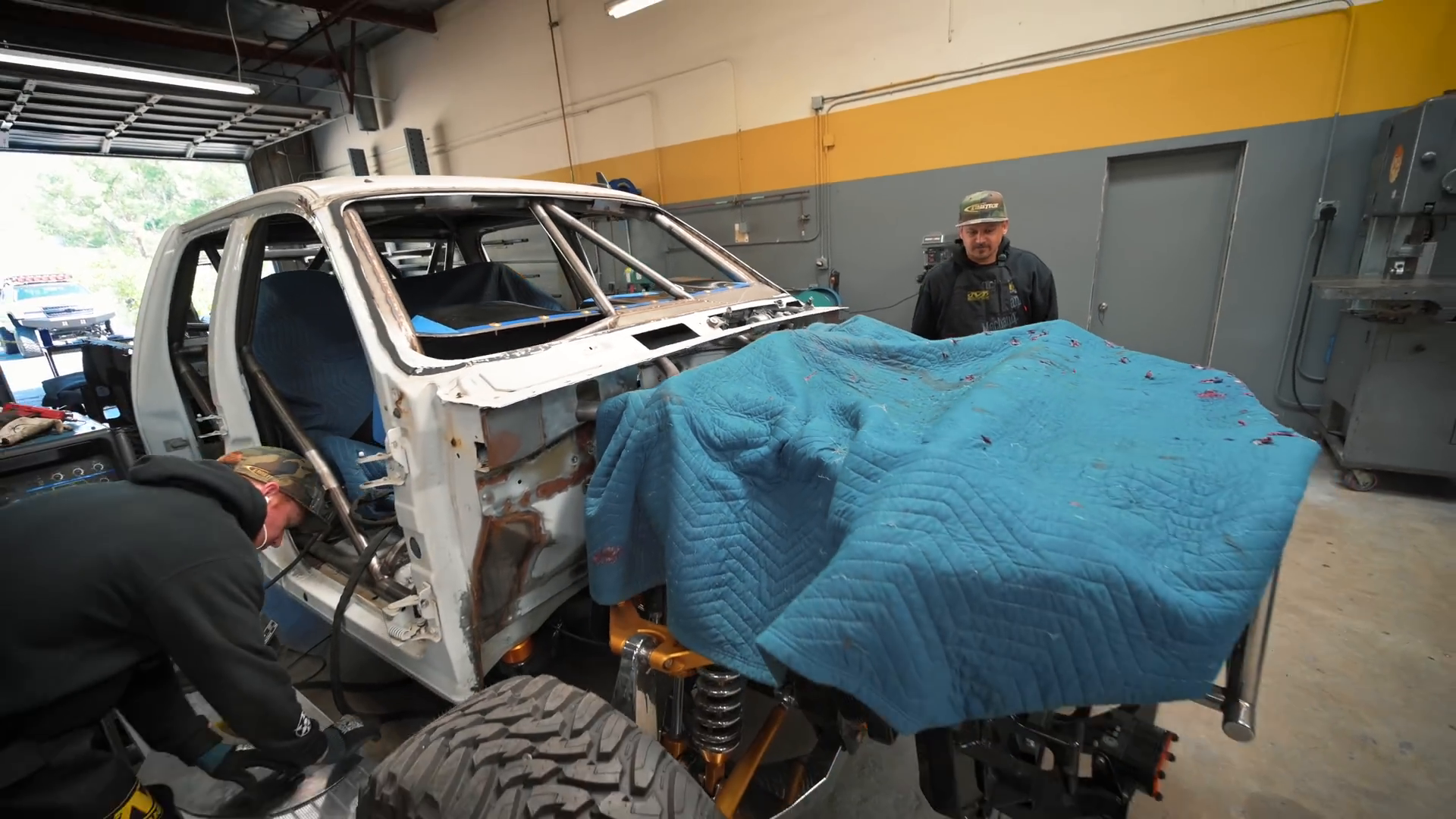
Integration of Electronics
With the structural elements nearing completion, the focus is shifting towards integrating electronics. Components like the dash shifters and columns are on their way, along with a variety of electronic systems. Once these elements are installed, the vehicle will undergo a series of final touches before the cab is removed for post-processing. This step is crucial to ensure the vehicle operates smoothly and efficiently with all new modifications seamlessly integrated.
Tube Chassis Truck Developments
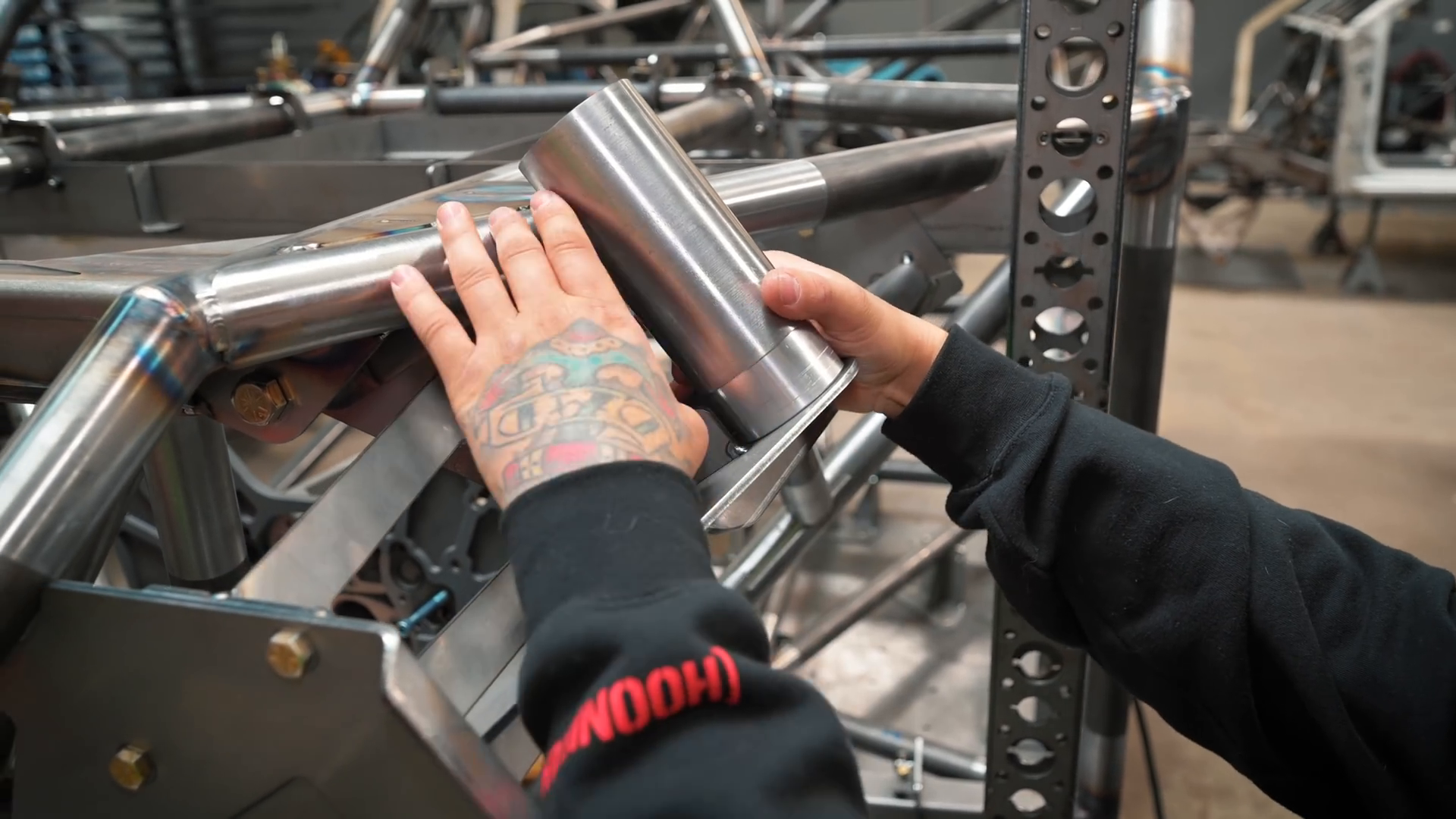
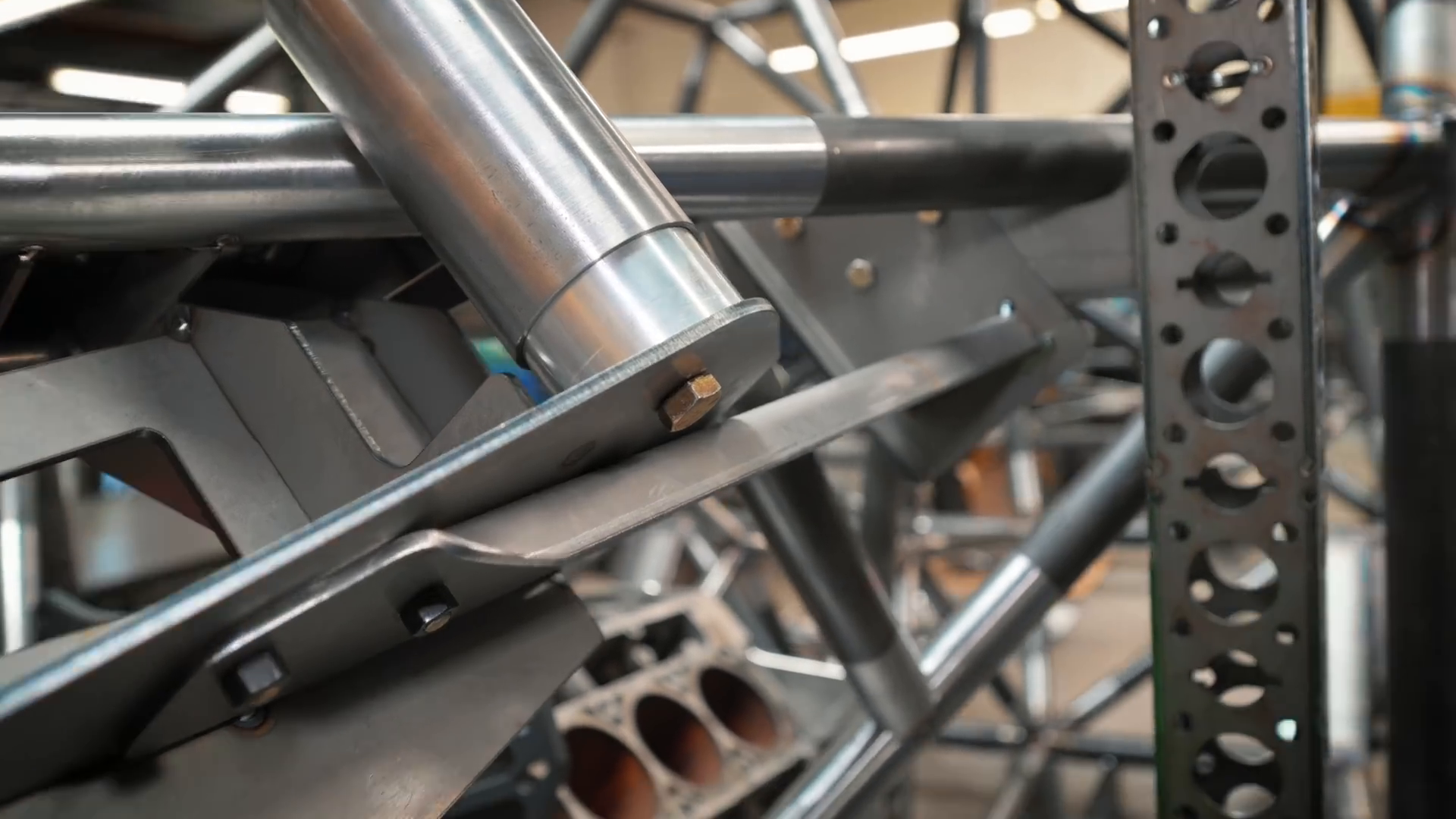
The tube chassis truck is another focal point in the workshop, where extensive welding and fabrication are underway. The fixture remains in place to guide the construction process, ensuring that all tubes are correctly positioned and welded. This meticulous process involves several stages, including tacking in filler pieces and allowing components to cool before proceeding with additional welding tasks. The goal is to achieve a robust shock mount and tube assembly that meets the demanding requirements of off-road racing.
OBS Ford Modifications
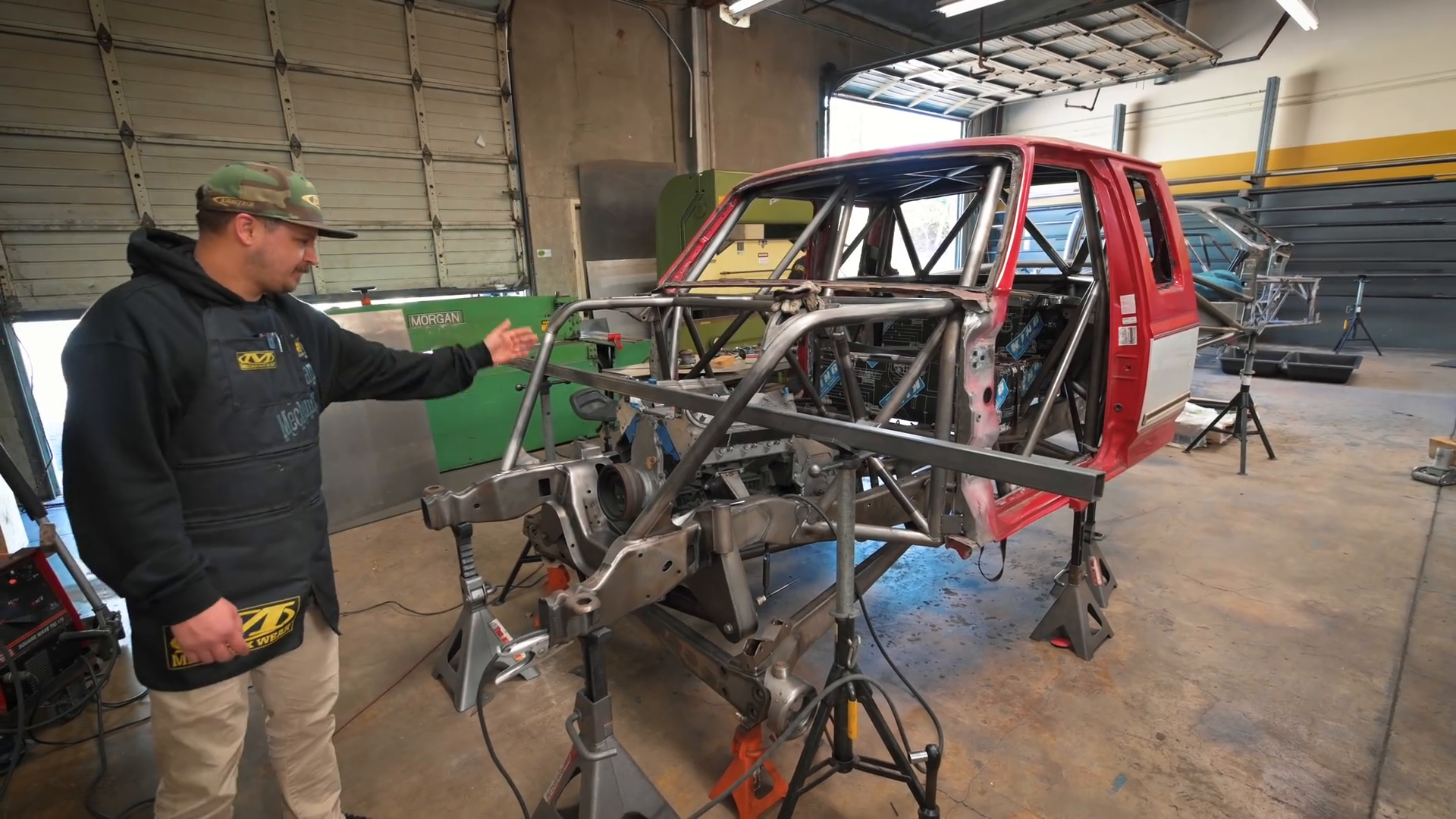
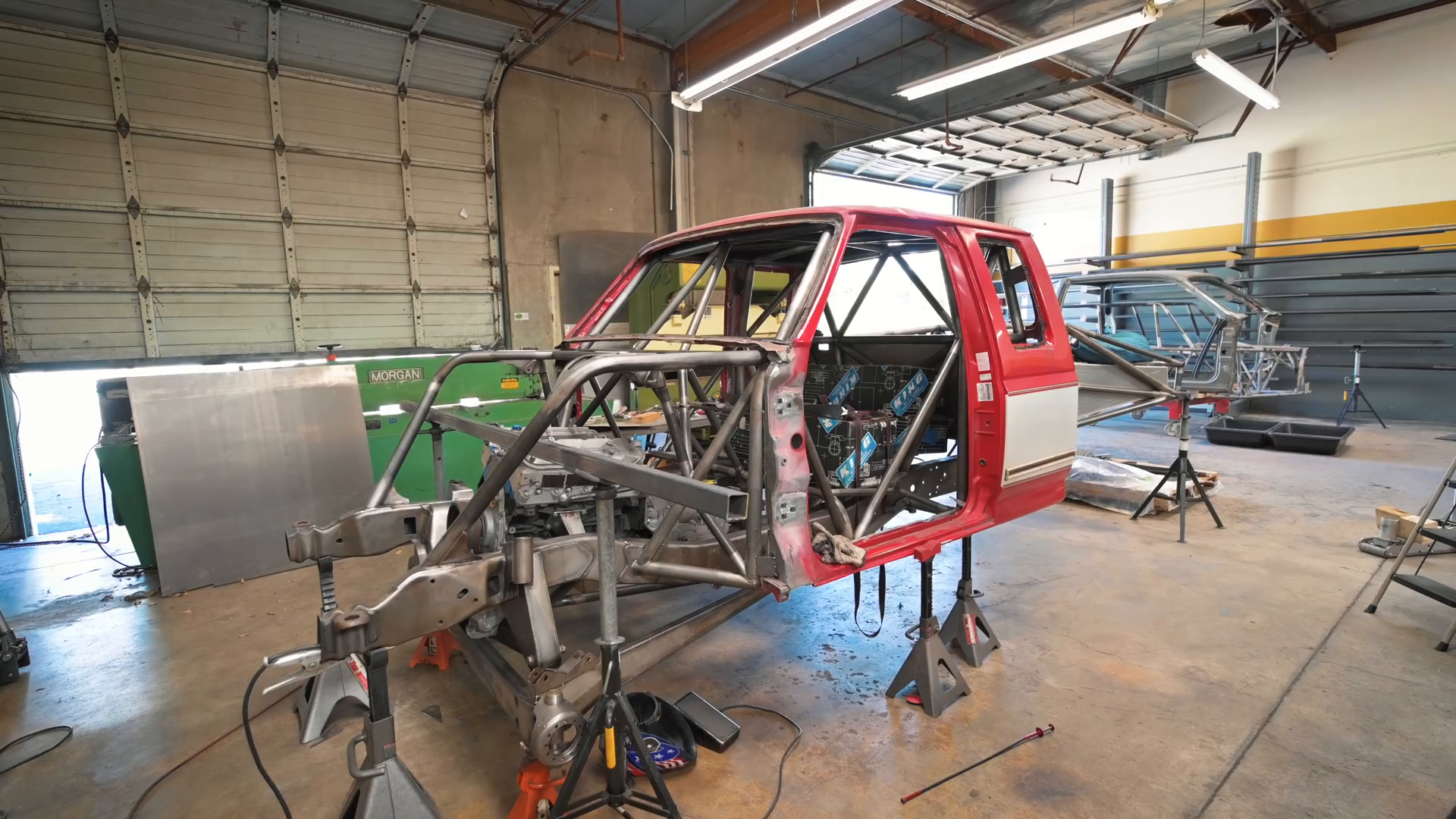
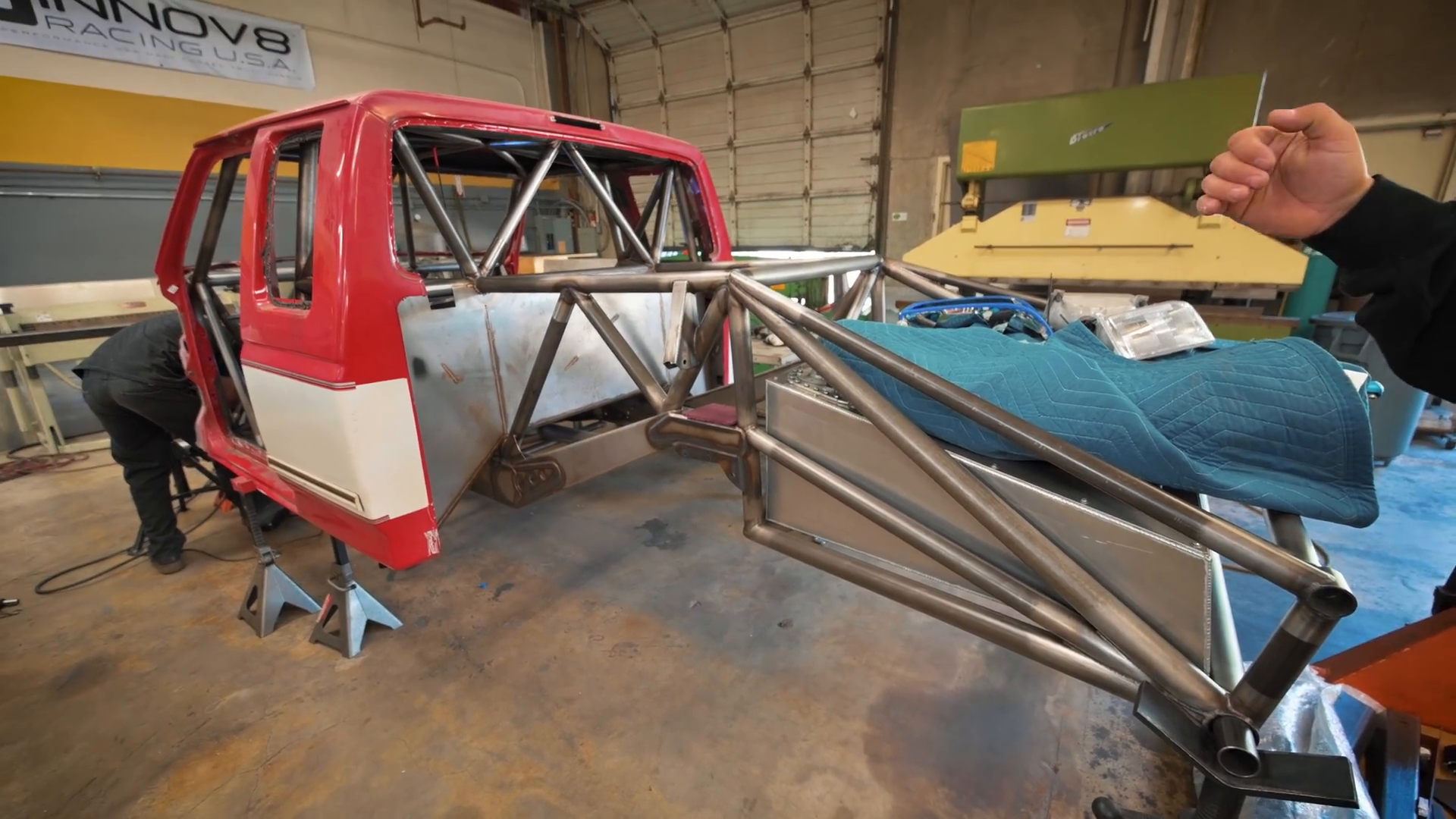
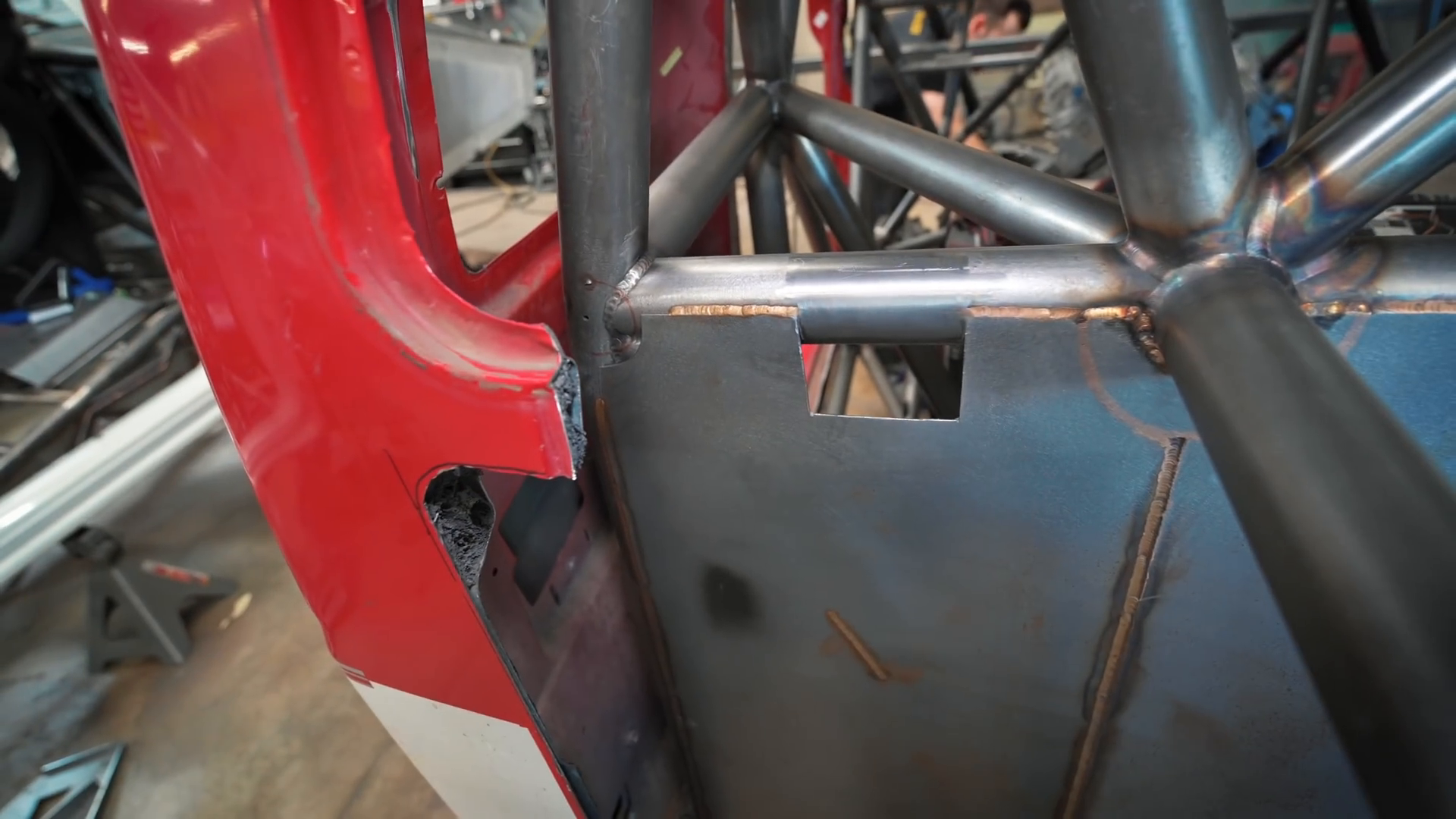
Engine and Structural Adjustments
The OBS Ford project involves a series of customizations aimed at enhancing its performance and structural integrity. A custom beam kit has been installed, powered by a 408 engine from Mulinix Racing Engines. The motor mounts are being redesigned for better clearance and ease of access, addressing issues observed with the previous setup. These modifications are essential for optimizing the vehicle’s performance, especially when dealing with the headers that conflict with the motor mounts.
Chassis and Suspension Enhancements
The project’s scope includes comprehensive work on the chassis and suspension. With shock mounts, bump mounts, and pivot points completed, attention is now on the steering system, which is set to feature a novel design not yet revealed. The cab, originally from another vehicle, has been replaced with one that has clean registration. This change involved significant alterations to the cage layout and frame, shortening the wheelbase for better handling and performance.
Machine Shop Progress and Future Plans
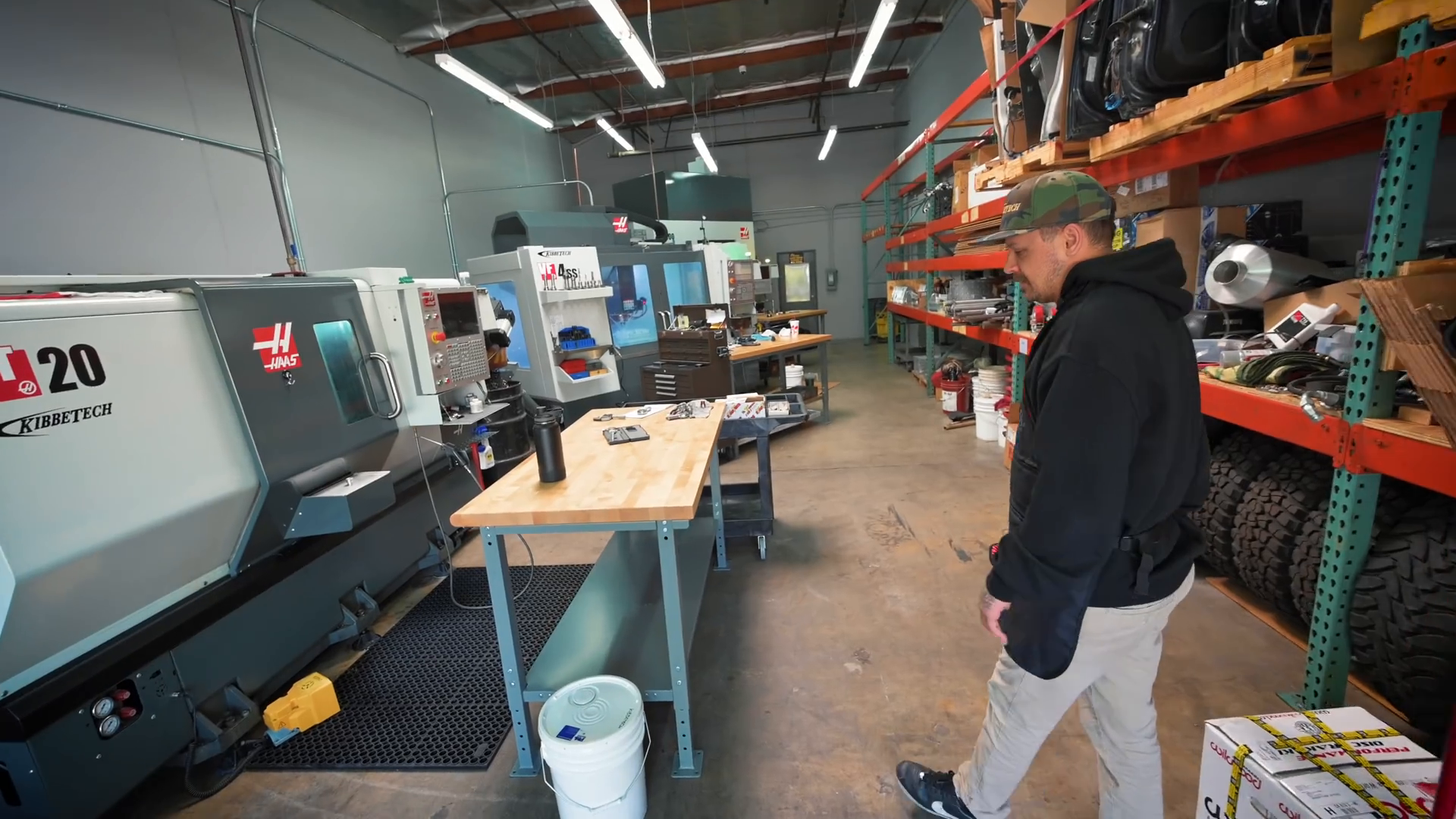
The machine shop at Kibbetech is bustling with activity as new equipment and setups are being finalized. Recent additions include new workstations with wood tops, providing organized and efficient spaces for each machine. This includes designated carts for staging materials and managing parts throughout the production process. The lathe, mill, and 5-axis machine each have dedicated setups to streamline operations and boost productivity.
The upcoming launch of the UMC (Universal Machining Center) is highly anticipated. While tooling and initial setup have faced delays, the machine is nearly ready to commence operations. This sophisticated equipment will enable advanced machining techniques, including 3D surfacing and simultaneous motions, crucial for handling complex parts with intricate radiuses and fillets. The implementation of 5th-axis tooling solutions promises to revolutionize the machining process, reducing the number of operations required for completing parts.
Conclusion
The projects at Kibbetech highlight the intricate and detailed work involved in high-performance vehicle modifications. From the Toyota Tundra’s suspension to the OBS Ford’s engine and chassis alterations, every task is carried out with precision and expertise. The ongoing advancements in the machine shop are set to enhance production capabilities, allowing Kibbetech to continue pushing the boundaries of engineering and fabrication. As these projects progress, they underscore the importance of innovation and meticulous planning in the automotive industry, paving the way for future developments and breakthroughs.
Categorized in: Fabrication, Prerunners, Trophy Trucks