Ranger Prerunner Build Part 9: Key Updates on Engine Cage, Shock Mounts, and Interior Design
The Ranger build is making significant strides as it transitions into a fully functional prerunner. This update covers the truck’s current state, focusing on the installation of key components such as the engine cage, radiator protection, and shock mounts. The project, led by a team committed to innovation and practicality, aims to create a unique vehicle capable of handling off-road challenges. This article delves into the intricate details of the build, exploring the decisions and engineering behind each modification.
Advanced Front-End Engineering
Engine Cage and Radiator Protection
The engine cage construction is a pivotal aspect of the Ranger build, providing a robust framework to support the vehicle’s front end. The cage incorporates two-inch 120-volt tubes, connecting to the A-pillar and extending under the cowling. A key feature is the custom radiator protection, ensuring the radiator is shielded from potential impacts. This thoughtful design places the radiator within the engine cage, a strategic move to enhance durability and safety. The choice of a 31×16 radiator, slightly smaller than the standard 31×19, accommodates the narrow frame rails of the Ranger.
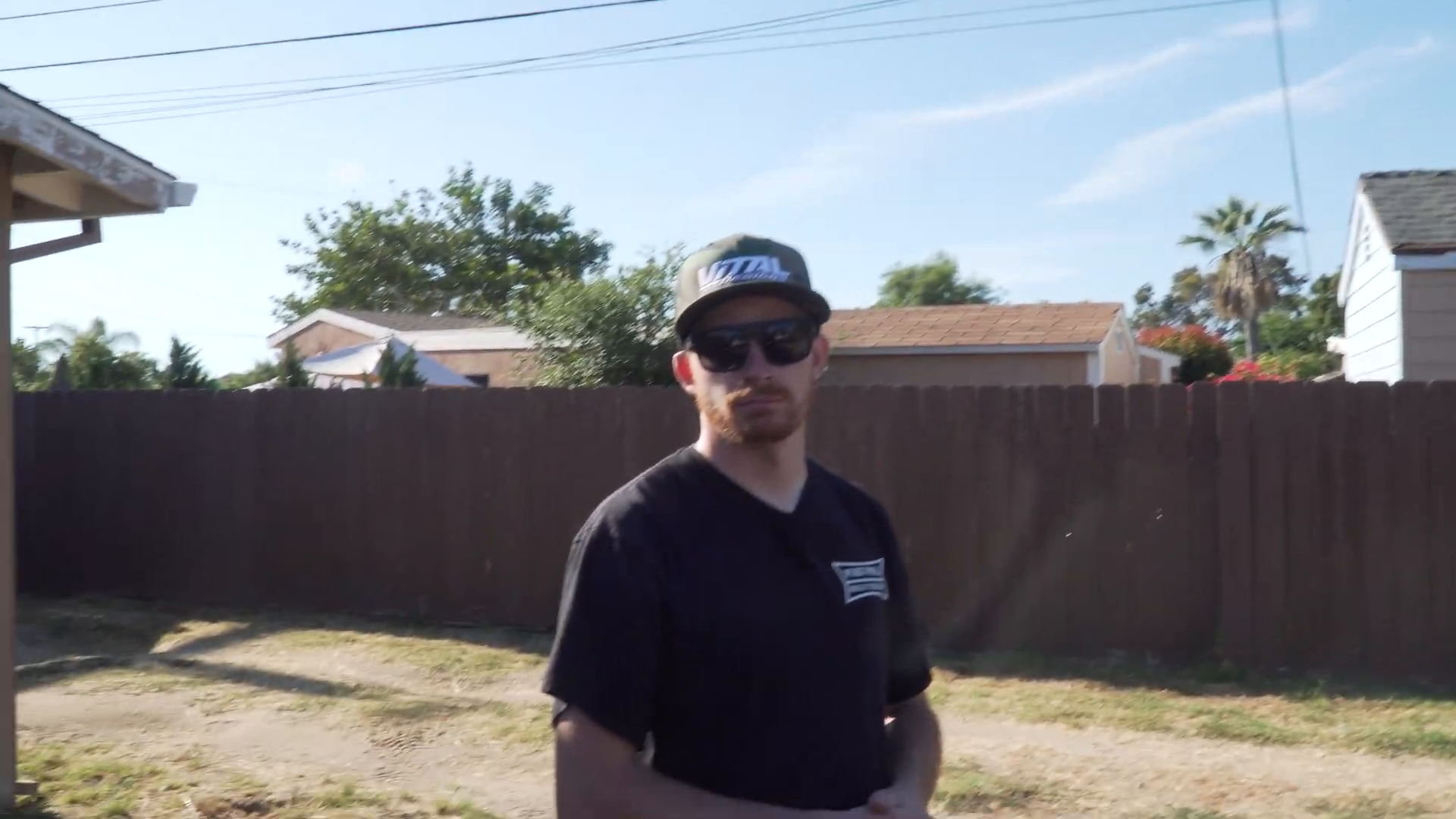
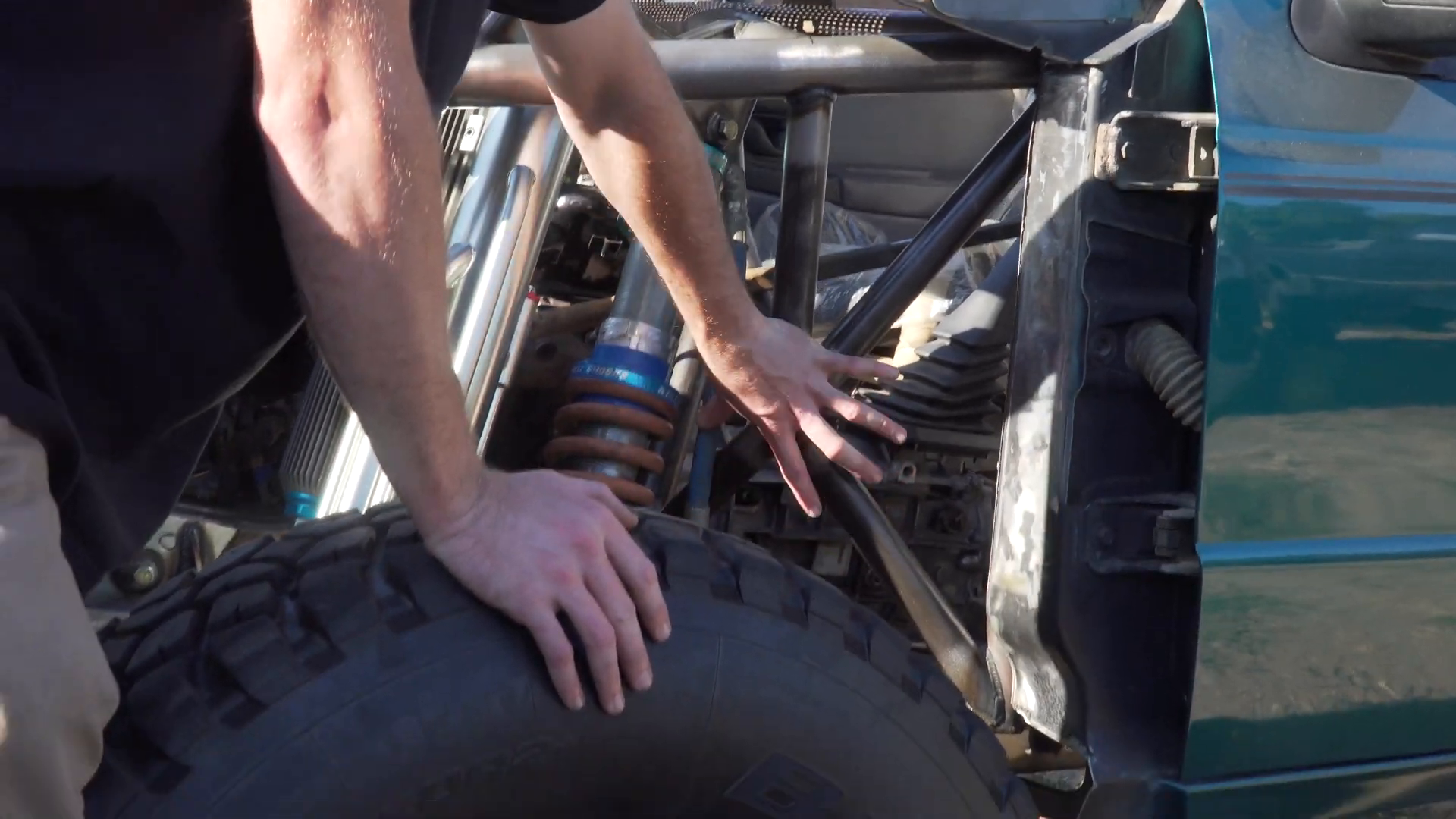
Shock Mounts and Steering Solutions
Shock mounts play a crucial role in the vehicle’s suspension system, with a unique inline setup adopted for this build. Unlike the staggered arrangement found in many trucks, the inline configuration simplifies assembly and aligns with the radius arm and beam. This design choice, combined with weld-in washers from Dirt King, bolsters the mounting structure’s integrity. The steering system has also been meticulously planned, relocating the steering box to optimize alignment and prevent interference during full compression. The integration of Delrin within the tie rods ensures stability, reducing the risk of binding and enhancing steering precision.
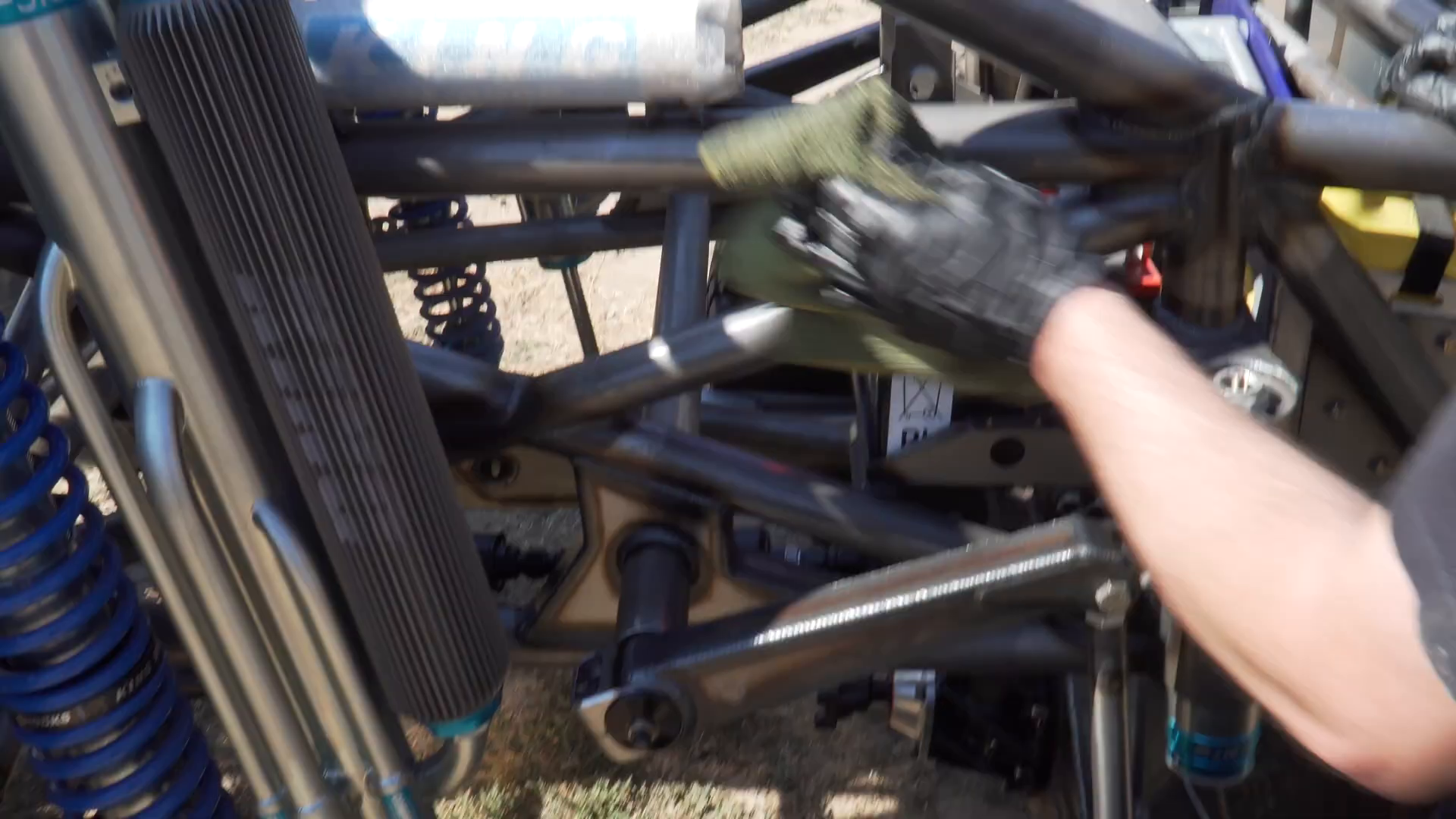
Interior Considerations and Comfort
Seat Positioning and Spatial Constraints
Inside the cab, the focus shifts to ergonomics and driver comfort. The seats are positioned for optimal height, angle, and distance, accounting for the limited space inherent in a regular cab truck. Adjustments to the pivot boxes were necessary to achieve a comfortable seating arrangement, maintaining a balance between headroom and leg positioning. Given the build’s emphasis on functionality, these considerations are vital to ensuring an enjoyable driving experience.
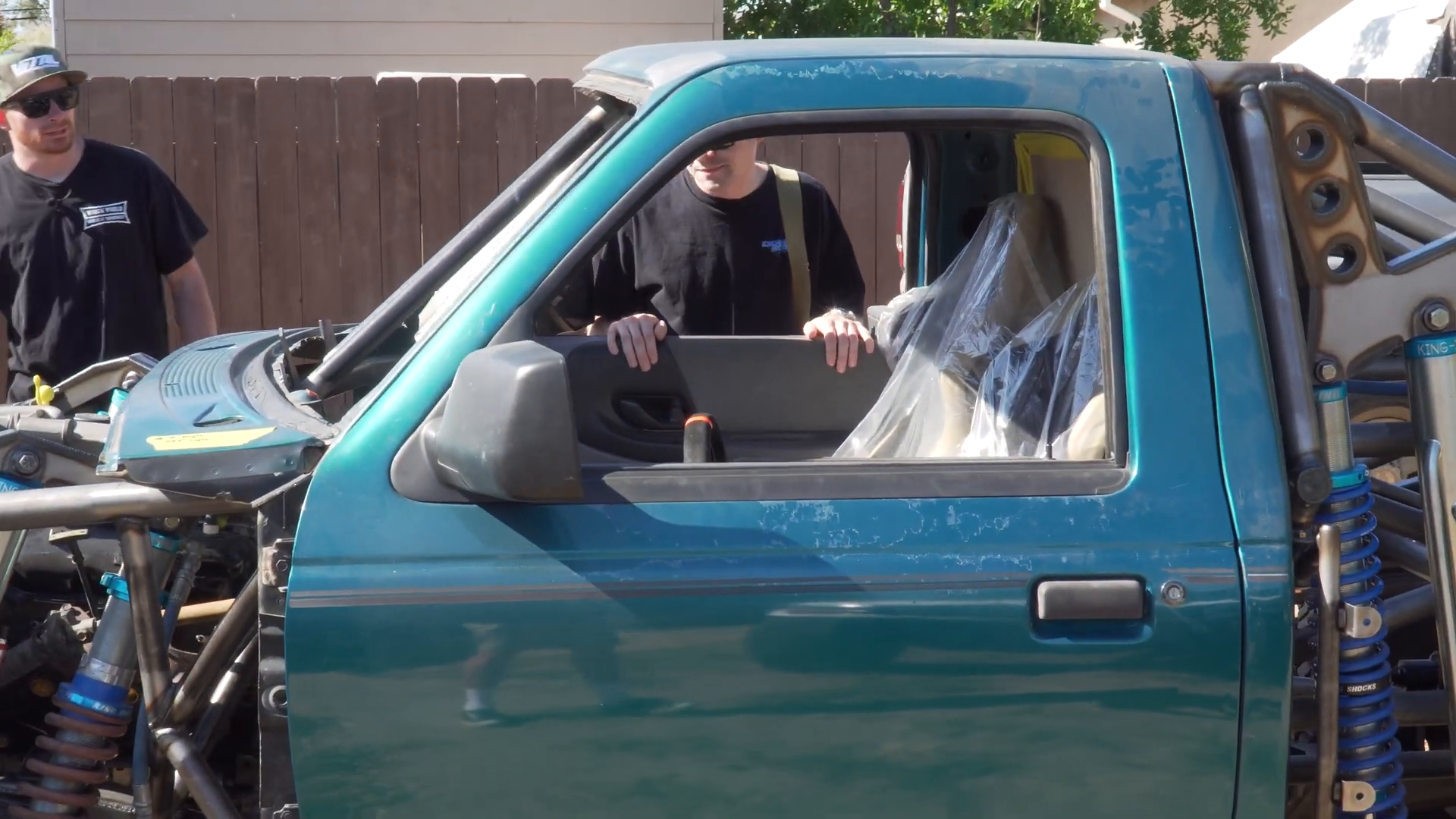
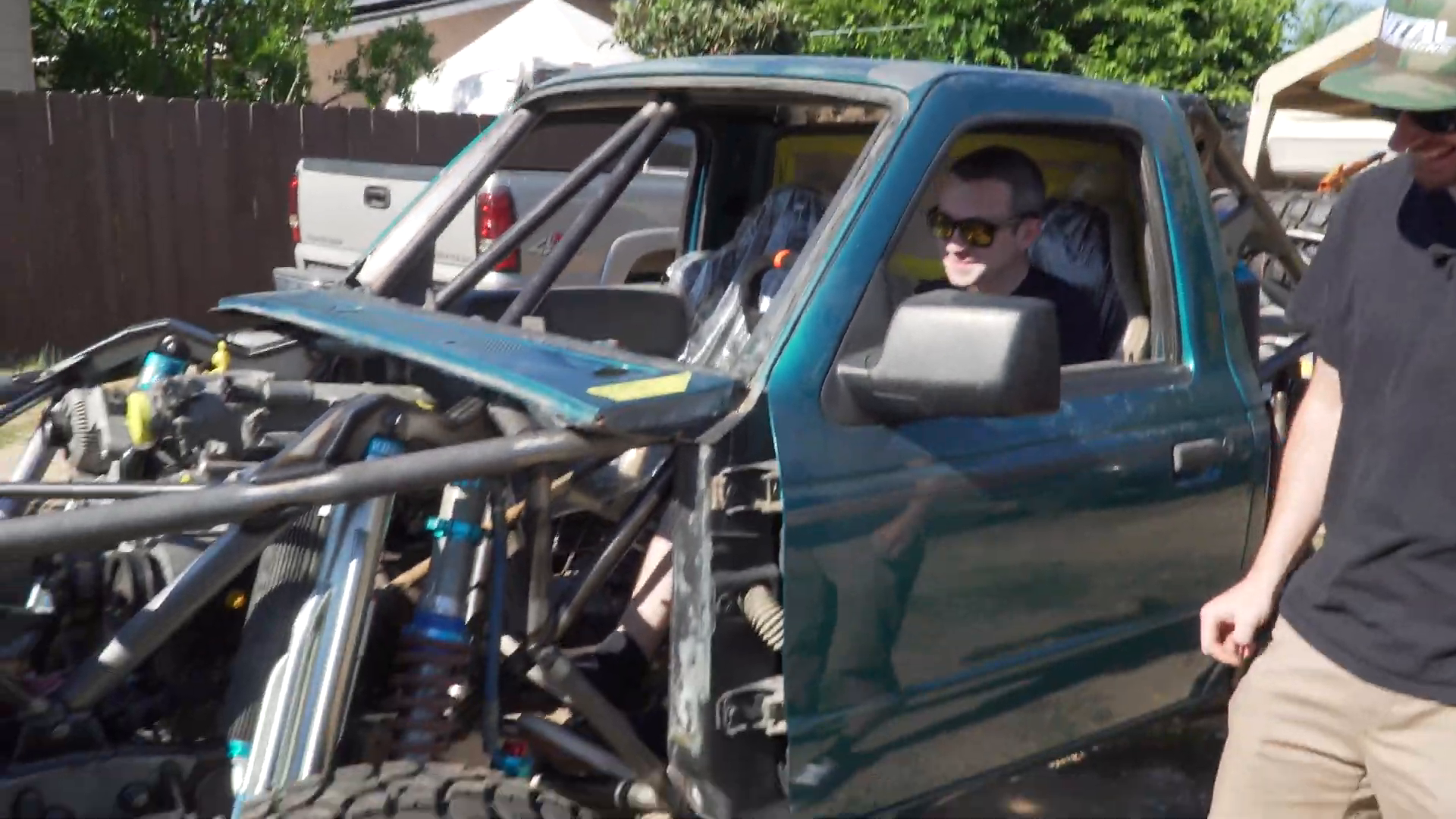
Pedal Configuration and Custom Solutions
The Ranger features a manual transmission, necessitating a three-pedal setup. With space at a premium, custom pedal fabrication is essential. This challenge presents an opportunity for innovation, allowing for pedal designs tailored to fit the available space while maintaining usability. The project’s success hinges on these custom elements, demonstrating the team’s ability to adapt standard parts to fit unique requirements.
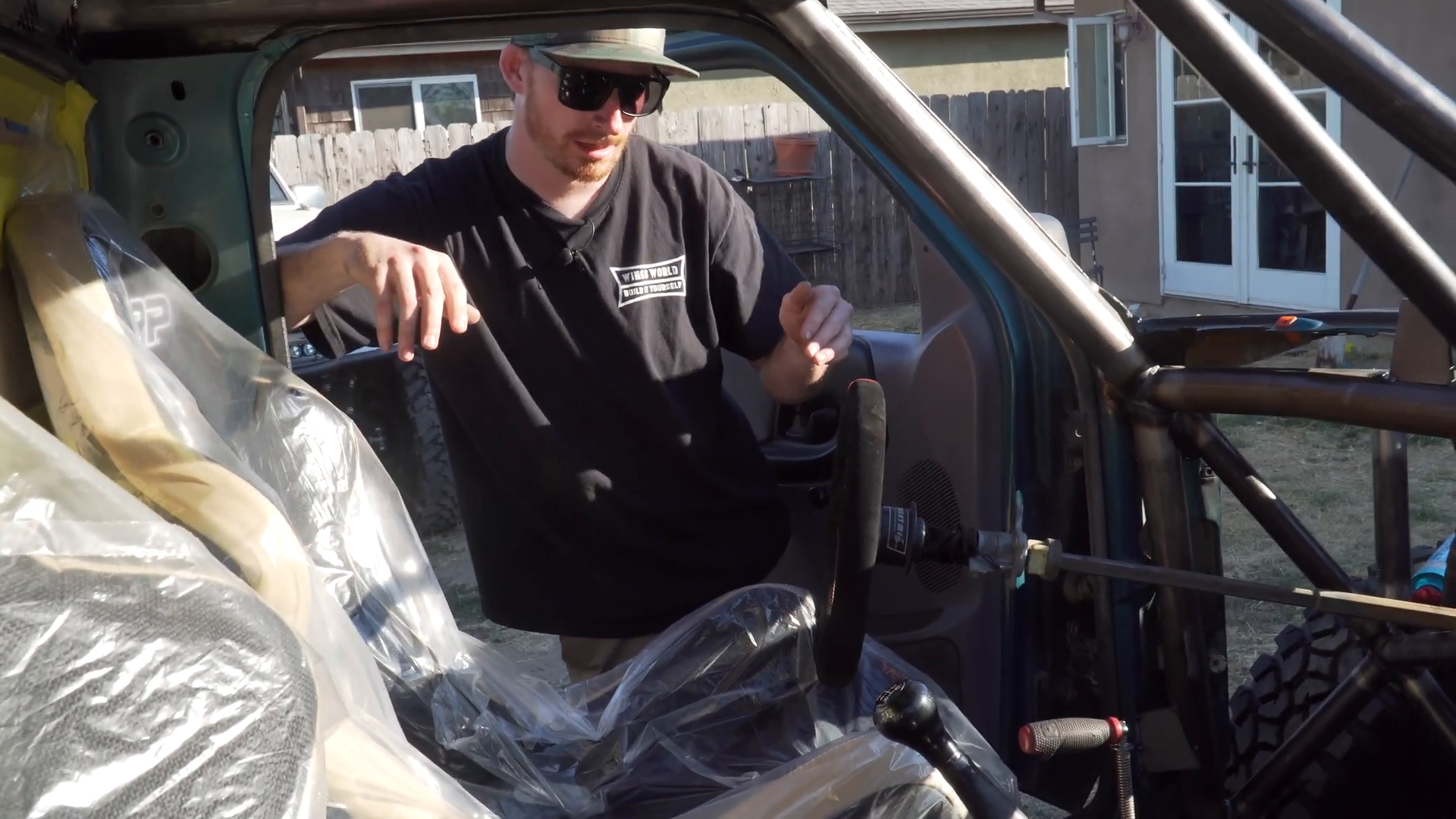
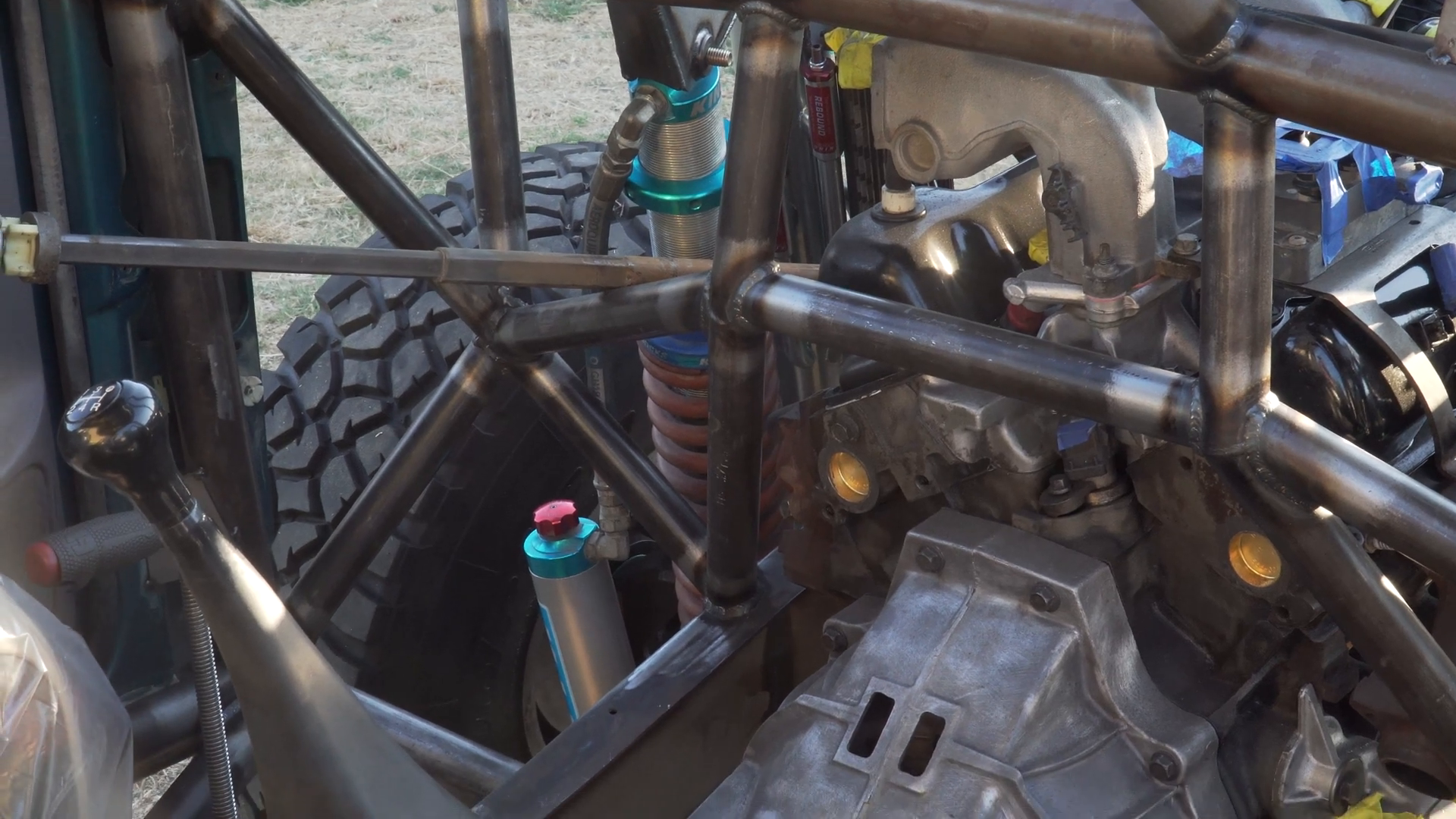
Structural Integrity and Future Prospects
Triangulation and Paneling
The build incorporates a robust tube structure to support the firewall and trans tunnel. This network of tubes is designed to maximize space while providing necessary structural support. The layout is influenced by the need to accommodate wheel travel and tire size, illustrating the importance of careful planning in custom vehicle builds. The strategic use of triangulation enhances rigidity, a crucial factor in off-road performance.
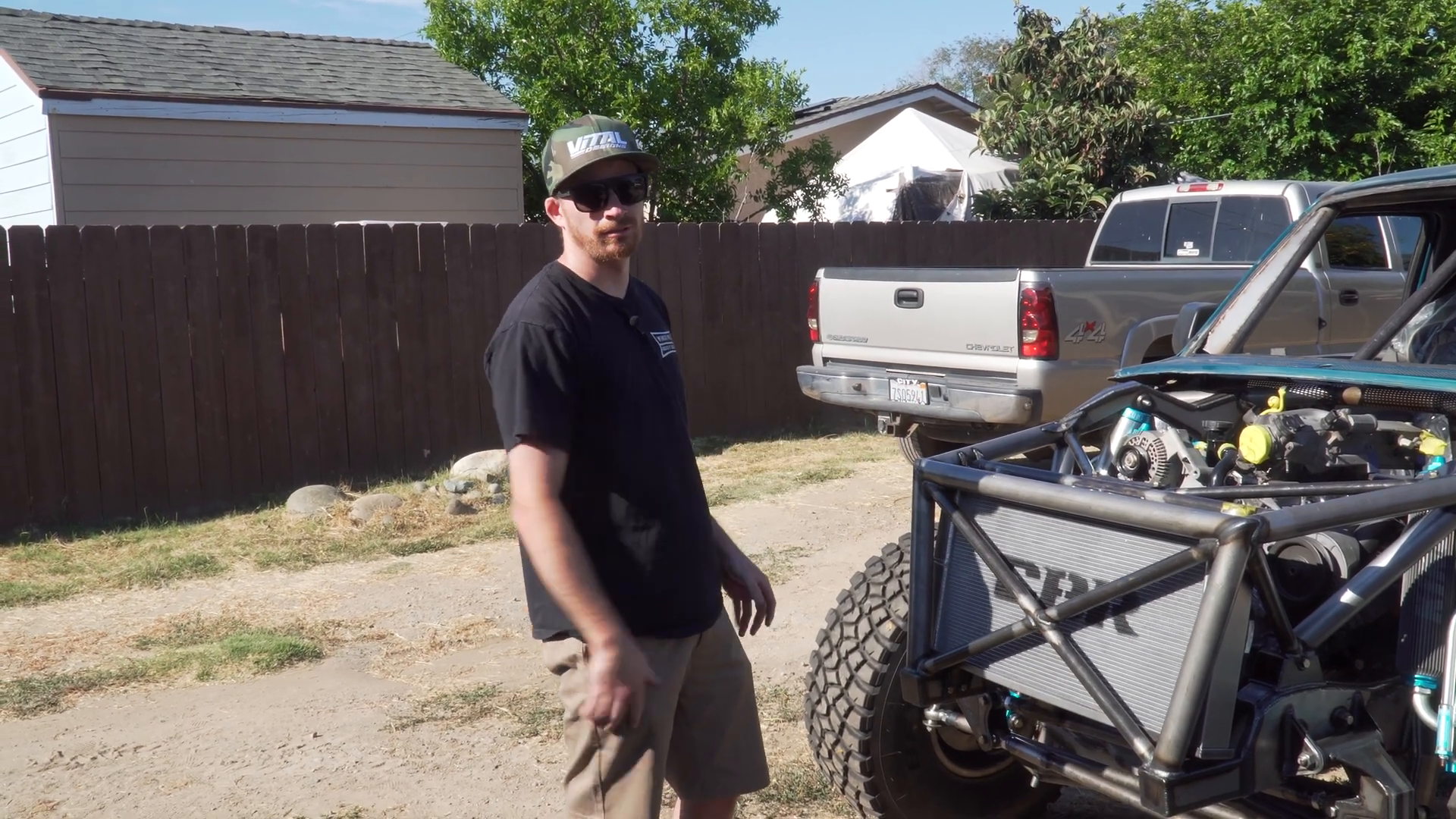
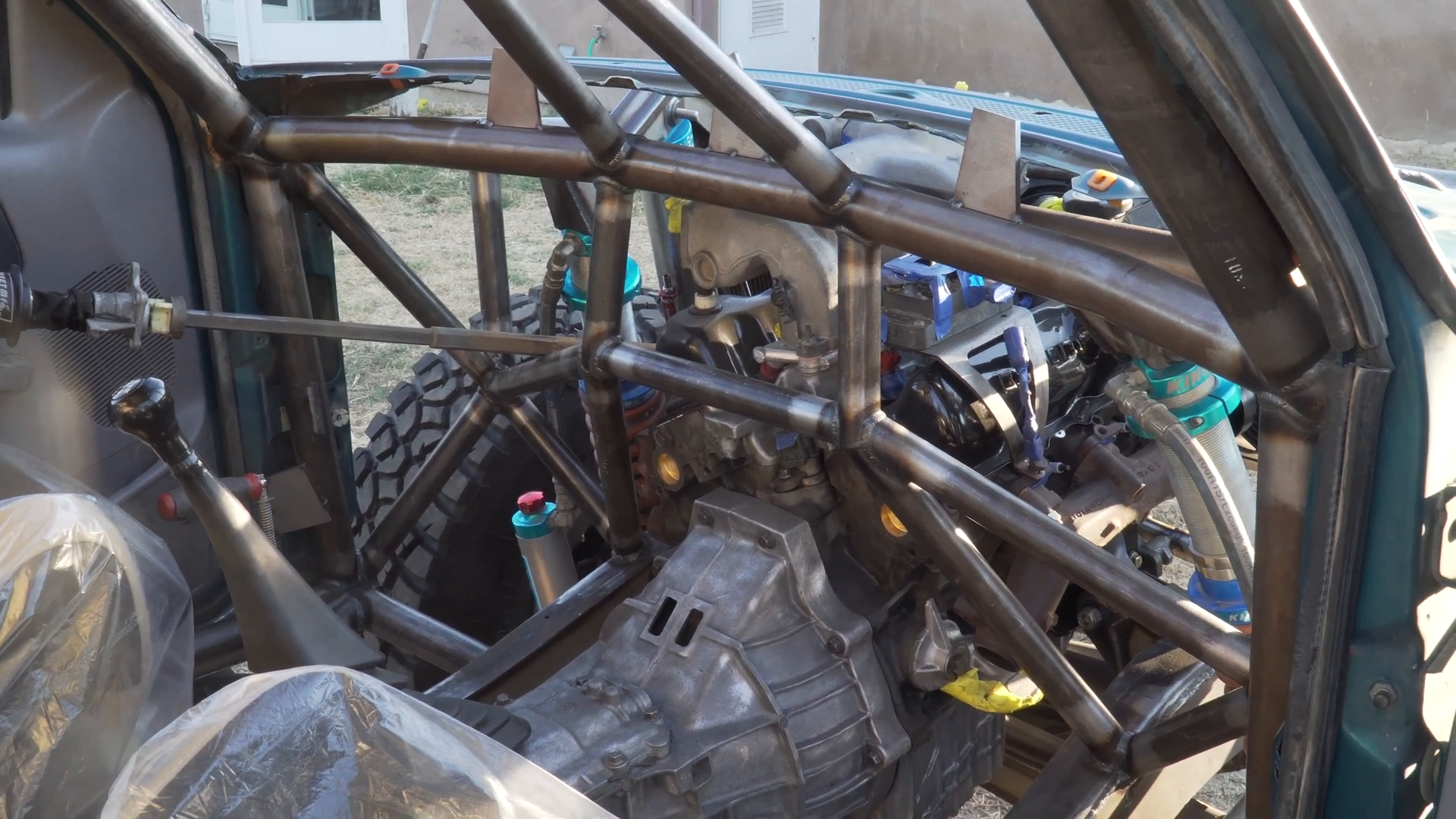
Upcoming Developments and Weight Distribution
As the Ranger progresses toward completion, attention will turn to precise weight distribution and suspension tuning. The current spring rate is tentative, subject to adjustment once the vehicle’s final weight is determined. Weighing the truck, including corner weights, will inform the final suspension setup, ensuring optimal performance across various terrains. This process highlights the meticulous attention to detail necessary in high-performance custom builds.
Broader Applications and Industry Impact
Customization and Innovation
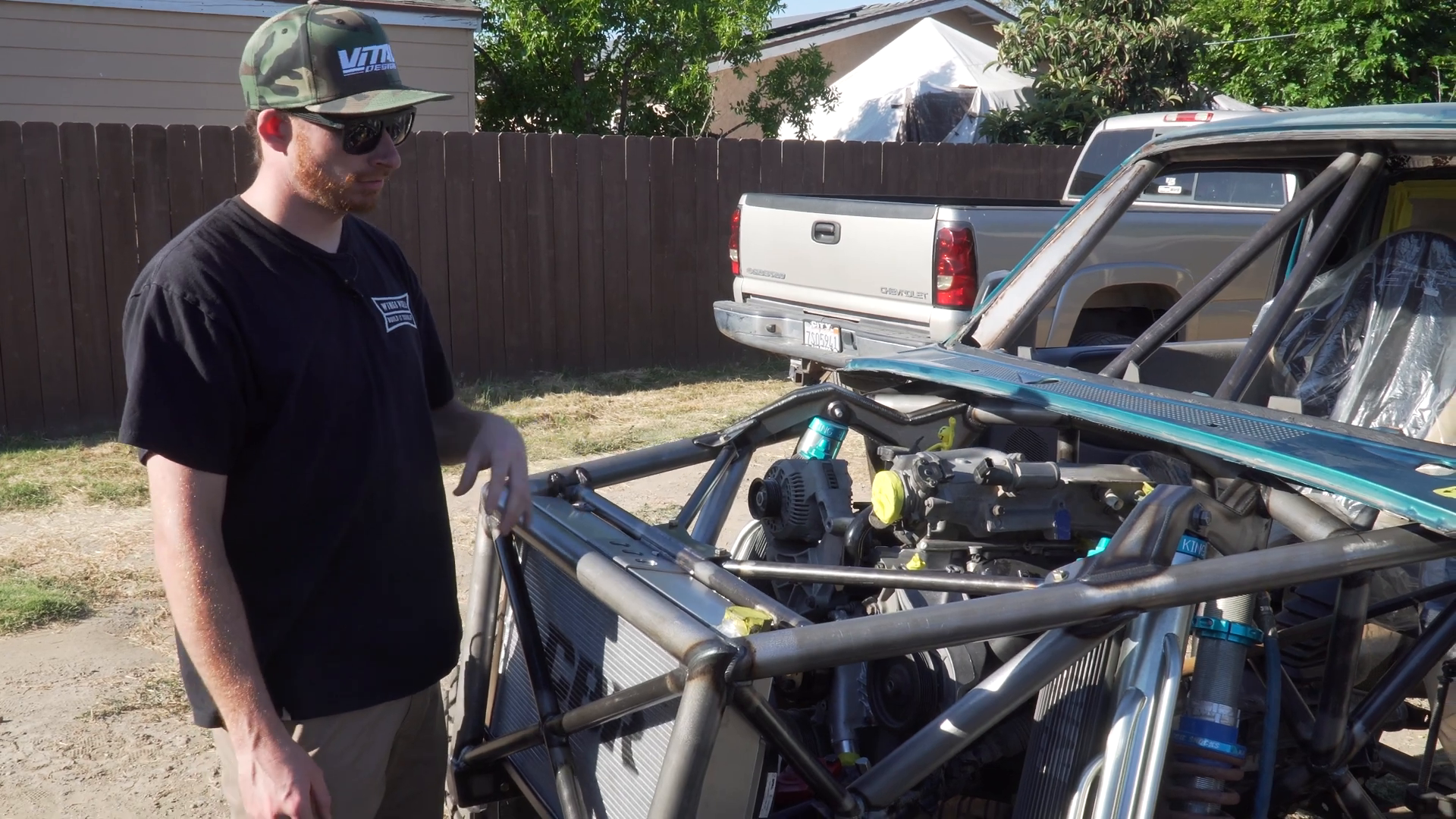
This Ranger build underscores the value of customization in meeting specific performance goals. By departing from conventional designs, the team demonstrates how innovative thinking can lead to practical solutions in custom vehicle fabrication. This approach is increasingly relevant as the automotive industry embraces personalization, allowing enthusiasts and professionals alike to tailor vehicles to their precise needs.
Future Trends in Off-Road Engineering
The trends observed in this build—such as integrated radiator protection, custom pedal assemblies, and modular shock mounts—are indicative of broader movements in off-road engineering. As the demand for versatile, durable vehicles grows, such innovations will likely become standard practices, influencing future designs and enhancing vehicle capabilities. The Ranger build serves as a case study in modern vehicle customization, setting benchmarks for efficiency and creativity.
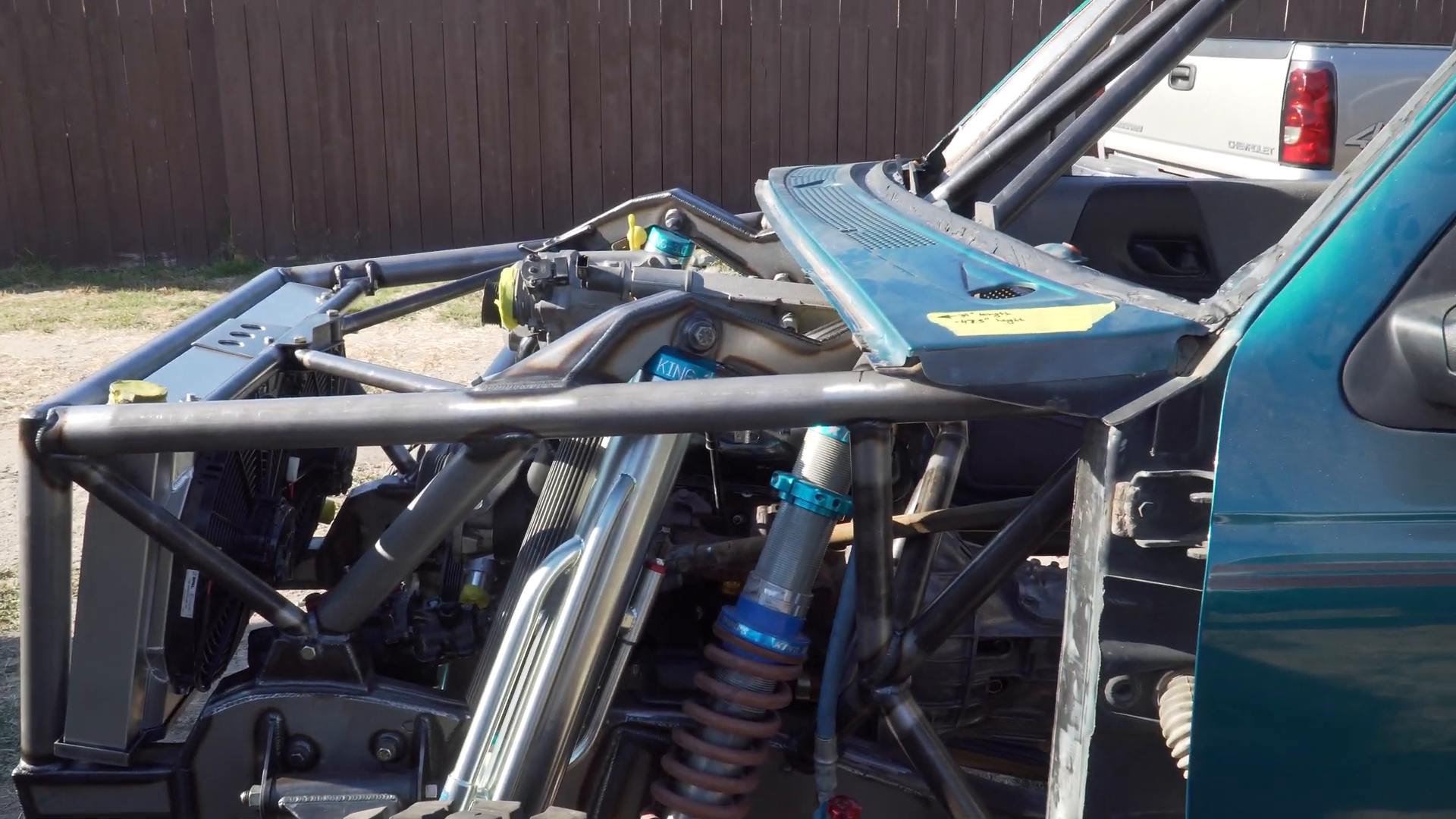
In conclusion, the Ranger build is a testament to the power of innovative engineering and the potential for customization in off-road vehicle design. Each component, from the engine cage to the steering system, reflects a commitment to pushing boundaries and achieving excellence. As this project nears completion, it will undoubtedly serve as an inspiration for future builds, showcasing the possibilities inherent in thoughtful design and execution.
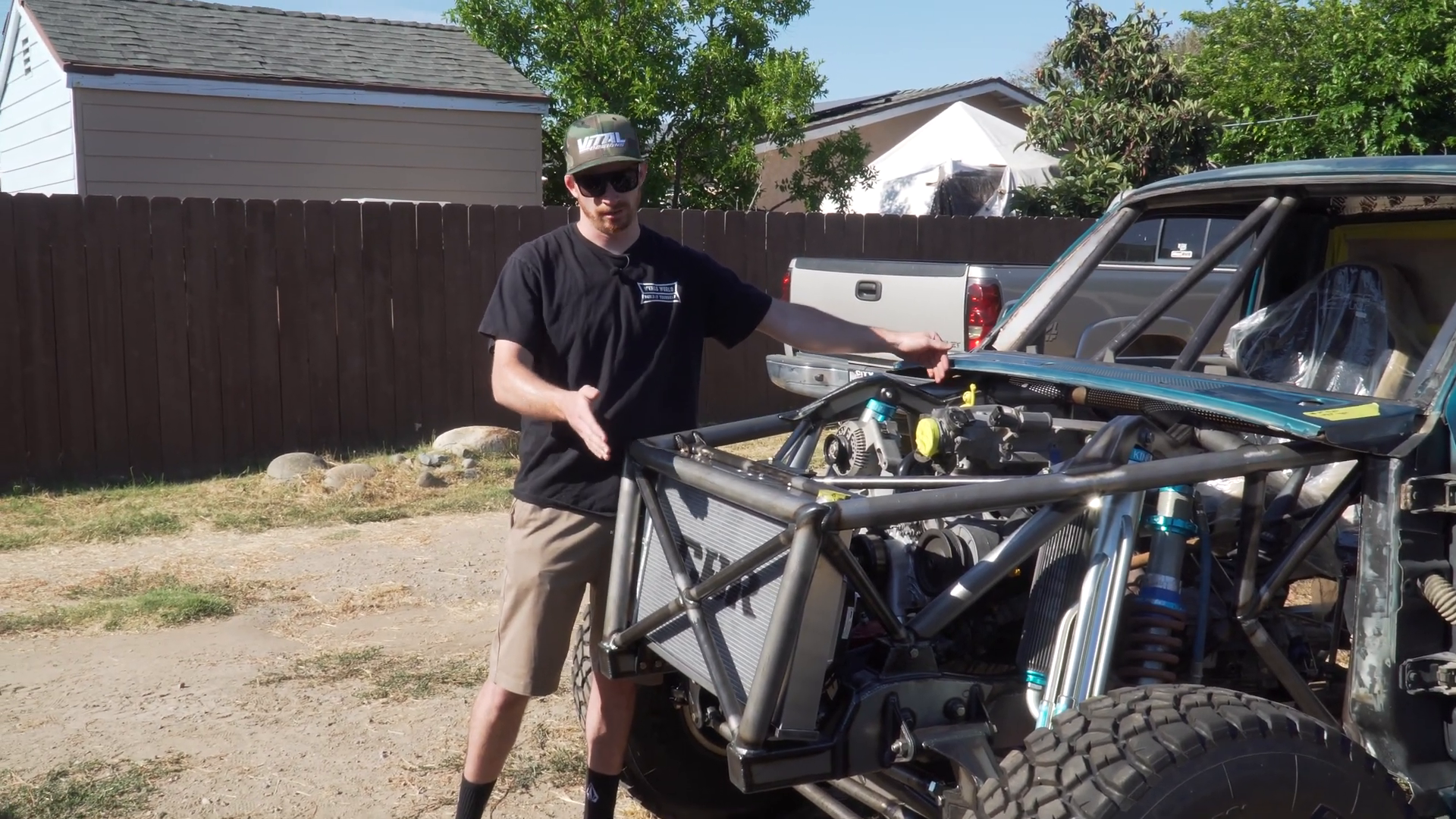
Categorized in: Trucks