Ranger Prerunner Build Part 8: Chassis, Suspension, and Interior Modifications Explained
The current project revolves around a detailed update on the build of a Ford Ranger prerunner, a custom off-road vehicle. This type of vehicle is often used in desert racing and is noted for its ability to handle rugged terrains. The prerunner is being extensively modified, focusing on both performance enhancements and aesthetic improvements. The build involves fabricating and installing custom components, optimizing its suspension, and retrofitting engine components, among other things. This particular article will delve into the specifics of the modifications made to the chassis, suspension, steering, and other pivotal parts of the vehicle.
Chassis and Structural Modifications
Enhancements and Reinforcements
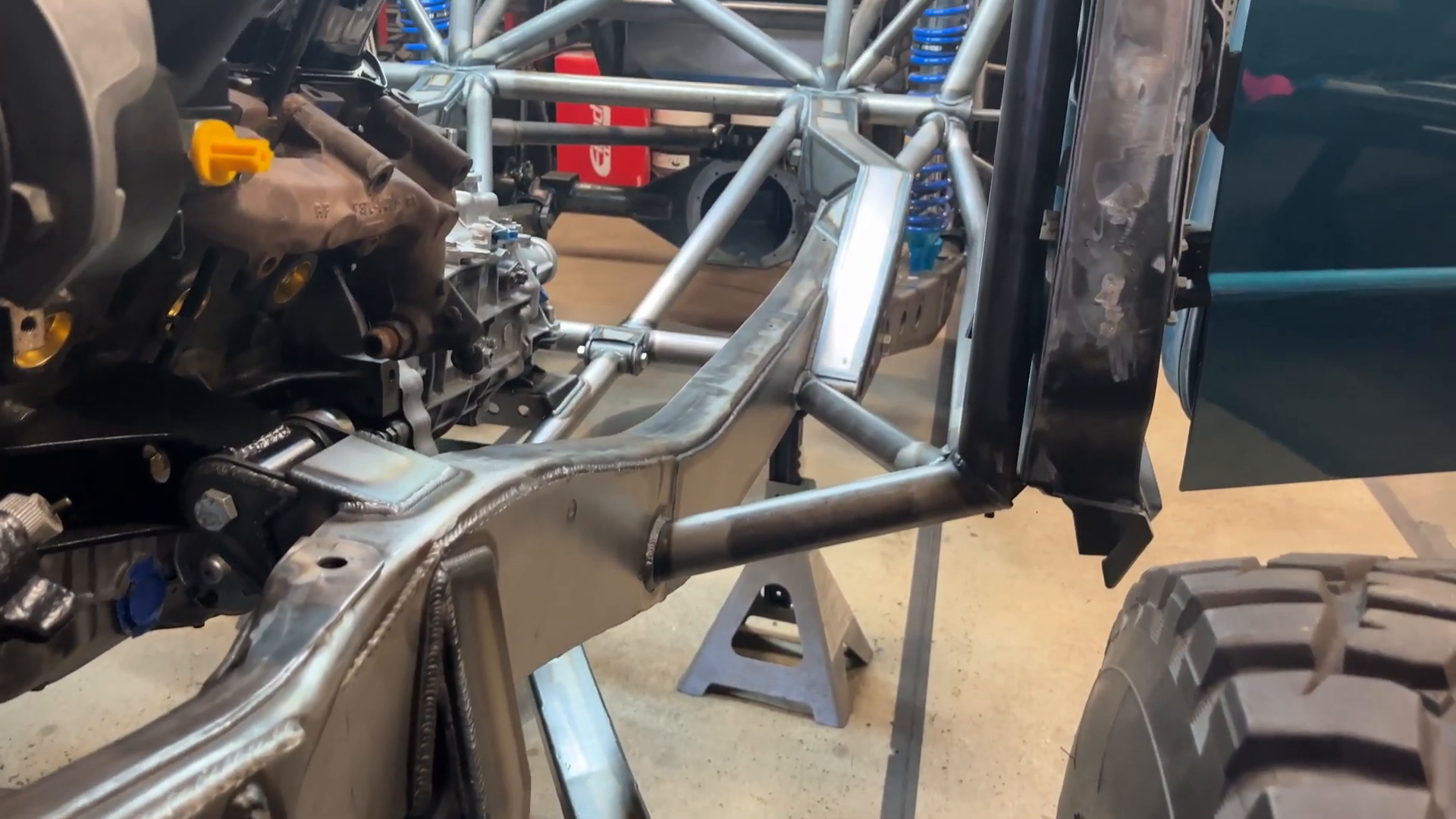
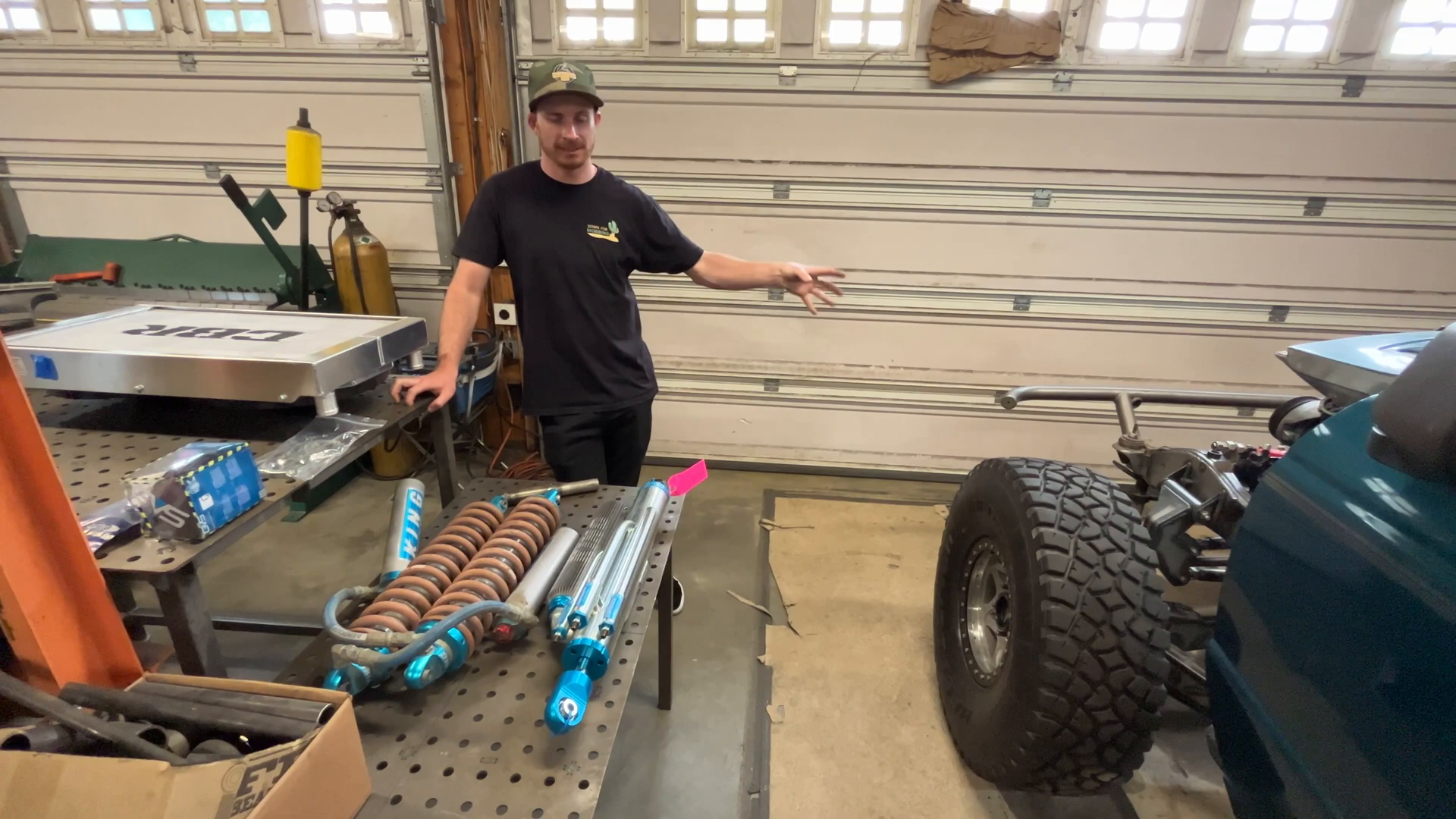
The structural integrity of the Ford Ranger has been a significant focus during the build. Initially, the front of the truck was stripped down to its factory firewall and frame rails. The primary upgrades included the addition of a custom beam kit, which has now been fully assembled and installed. This kit enhances the vehicle’s off-road capabilities by allowing for greater wheel travel and improving overall durability.
Building the Cross Member
A new tubular cross member has been crafted to replace the factory variant, which was deemed a restriction for the new suspension system. This custom cross member is fabricated using inch and three-quarter 120-wall tubing, providing a robust and flexible platform for the engine and suspension attachments. This change facilitates better handling and provides greater support for the modified engine placement, which has been moved back by approximately six inches for optimal weight distribution and center of gravity.
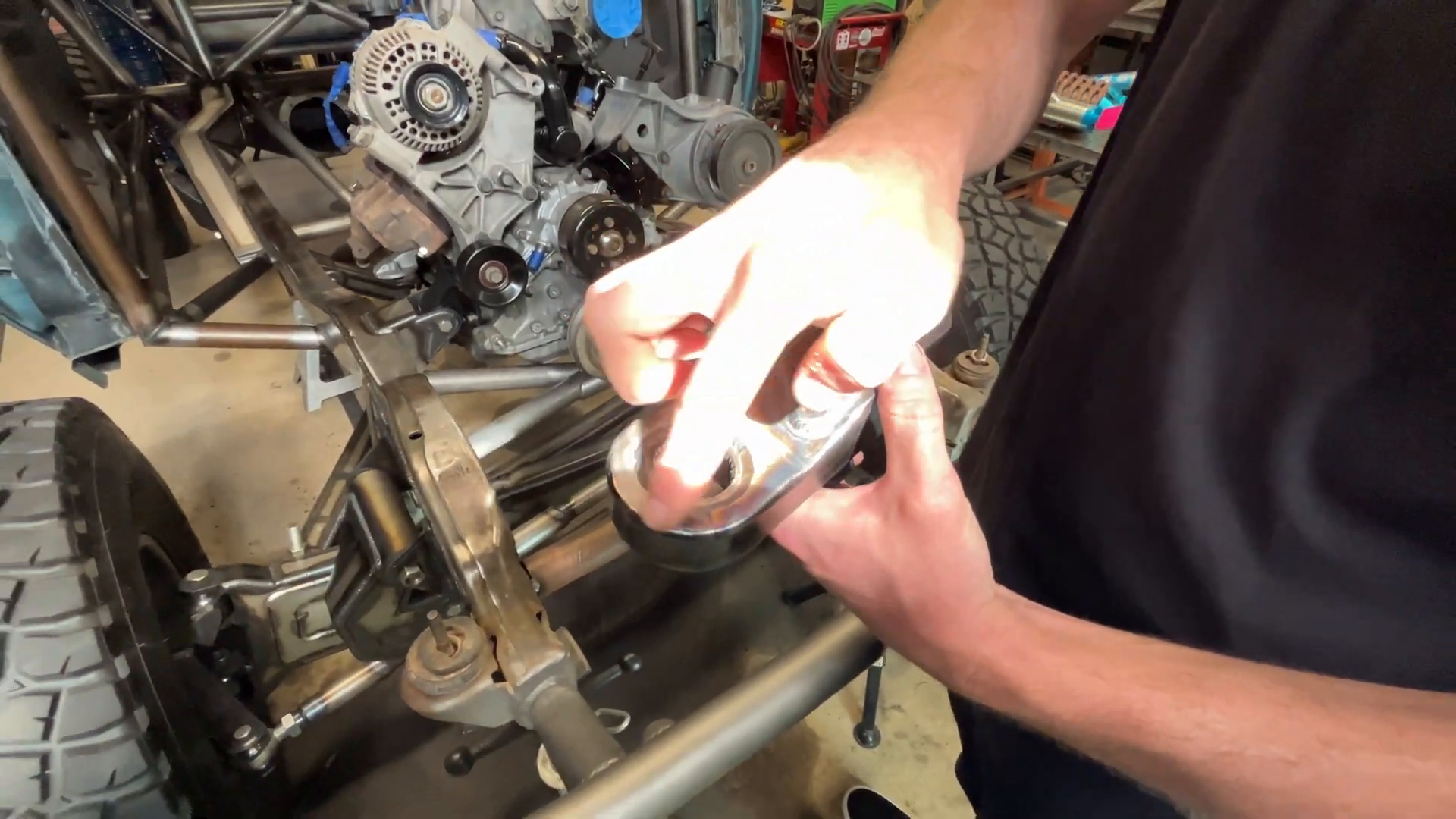
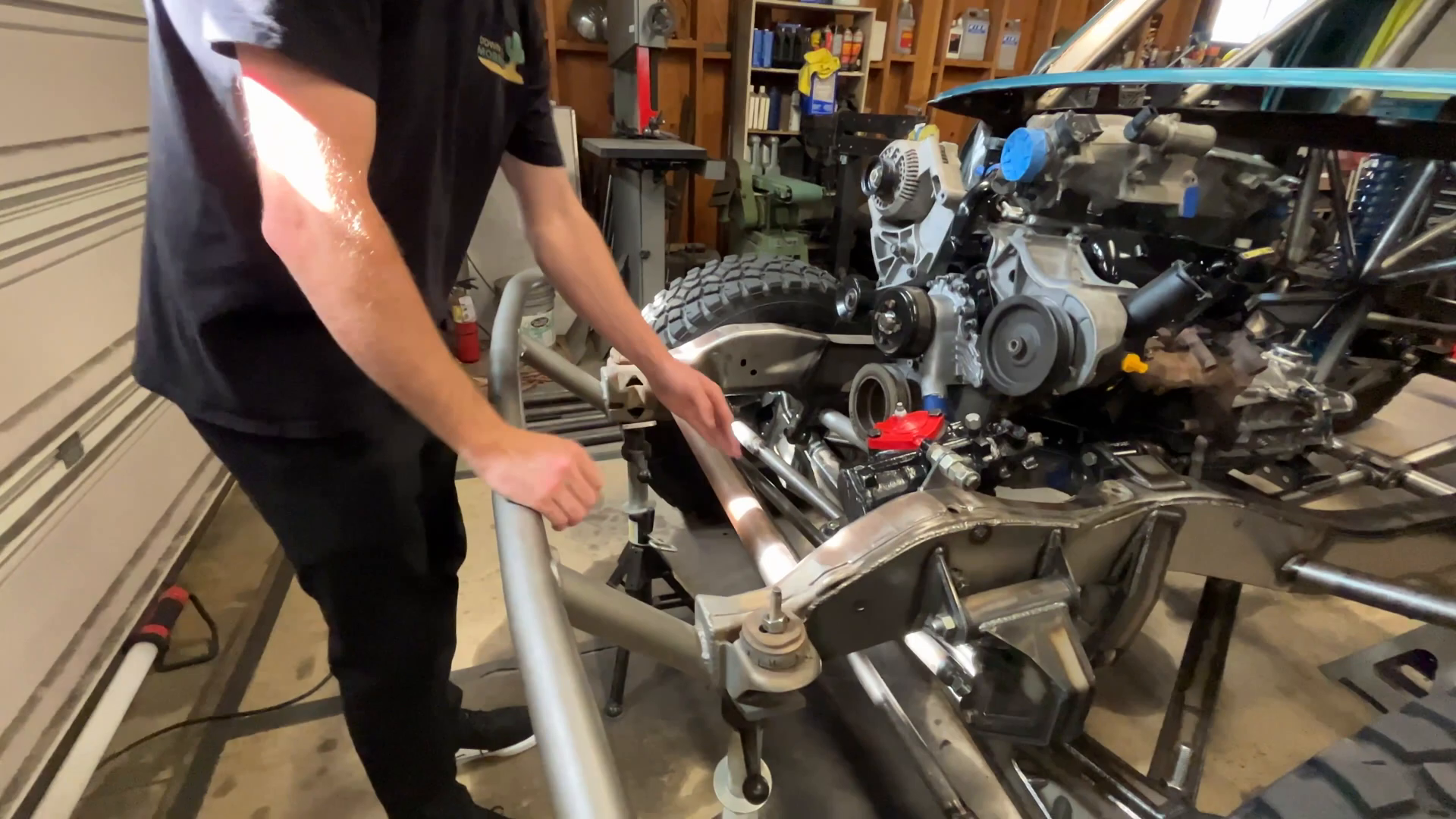
Firewall and Engine Positioning
With the engine shifted back, significant alterations were made to the firewall to accommodate the new setup. This adjustment not only optimizes weight distribution but also enhances cockpit ergonomics, allowing for a more comfortable and practical driver experience. The backside of the transmission was previously constrained, requiring a two-piece drive shaft, but with the new positioning, a single-piece drive shaft is now feasible.
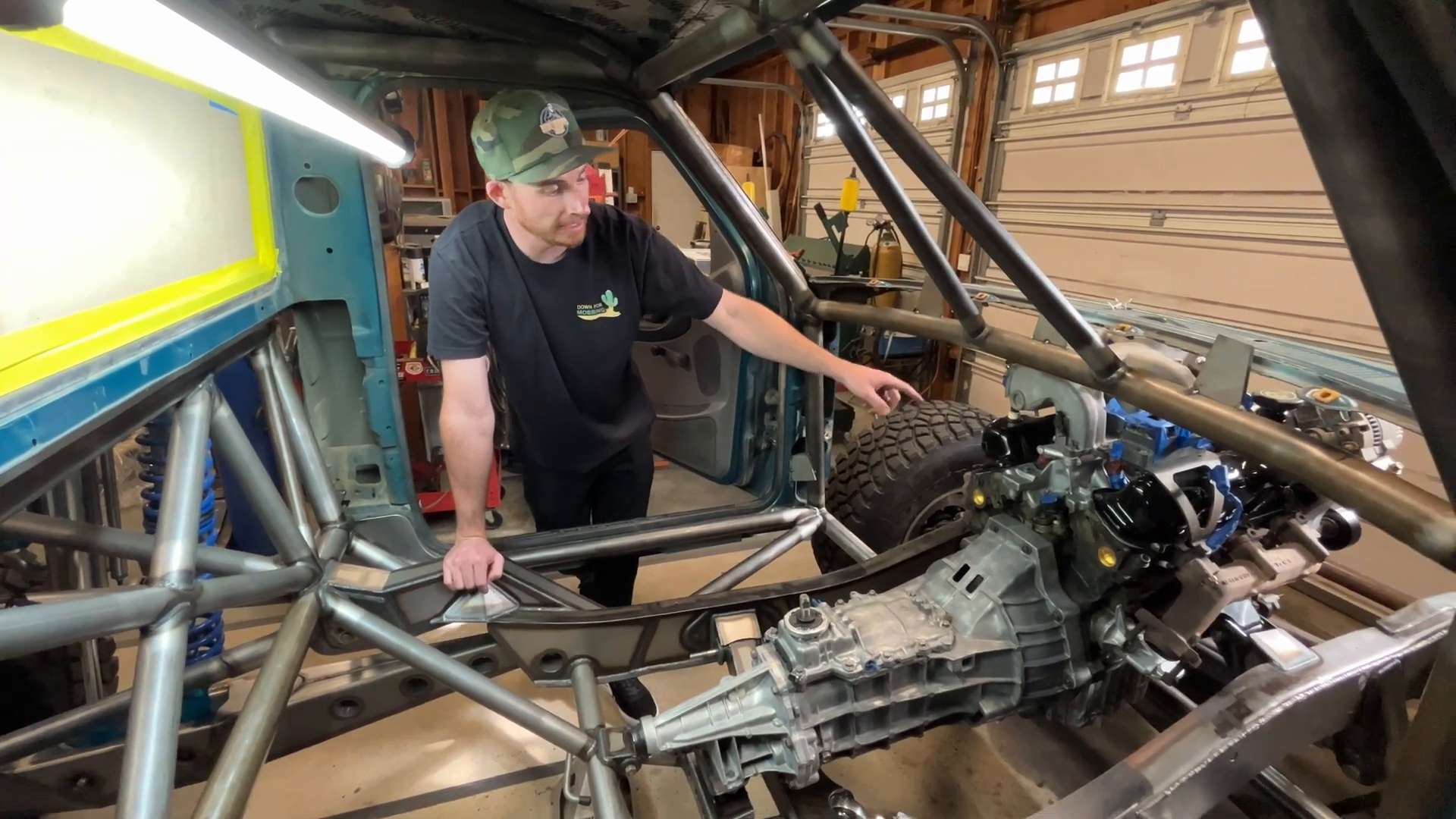
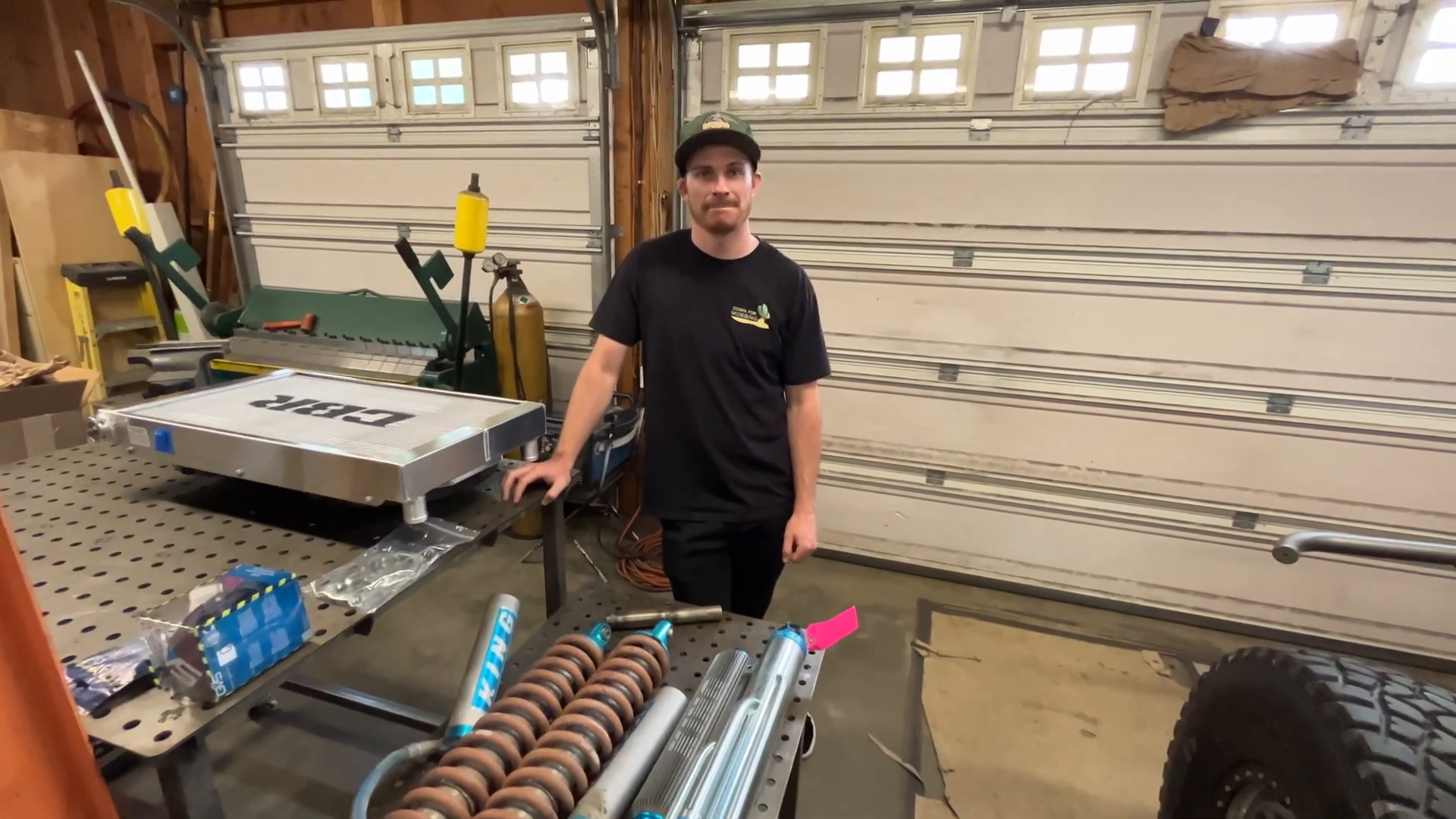
Suspension and Steering Systems
Custom Steering Setup
The steering system has undergone a thorough revamp to improve precision and durability. The steering box was repositioned to accommodate the straight tie rods, which were fabricated using inch and a quarter 250-wall tubing for enhanced strength. The custom pitman arm was hand-built to provide a double shear configuration, ensuring the steering system’s robustness. This setup minimizes deflection and maintains steering stability across different terrains.
Beam Suspension System
The prerunner now sports a center-mounted radius arm setup, facilitating improved suspension geometry and handling characteristics. The design ensures minimal bump steer and optimal caster angles throughout the suspension cycle, important for maintaining control over uneven surfaces. Custom beam mounts, designed in SolidWorks, were adjusted during assembly to ensure a perfect fit, underscoring the importance of precision in custom builds.
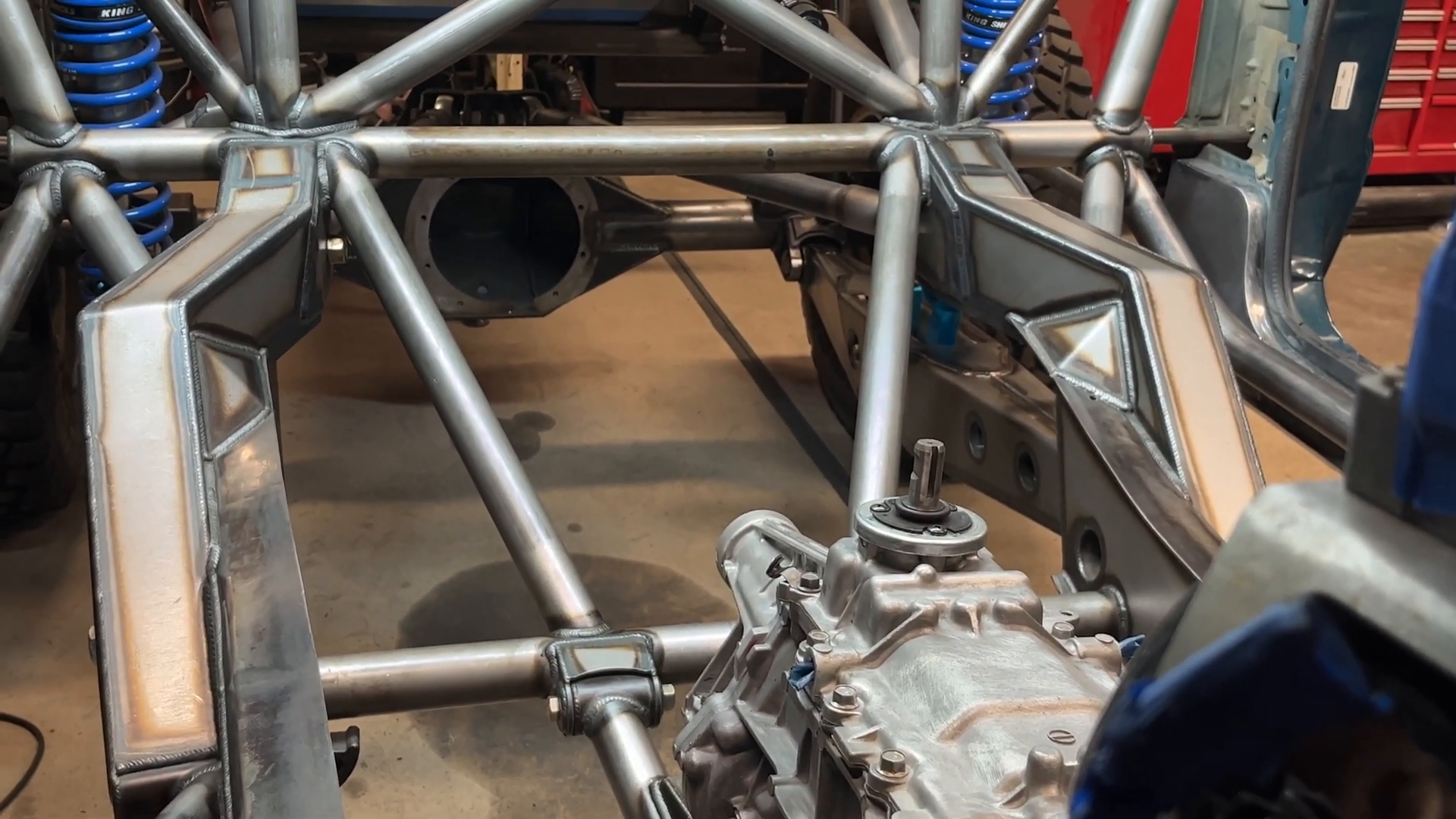
Cab Interior and Controls
Driver Ergonomics
Inside the cab, modifications were made to improve driver ergonomics. The repositioning of the engine and transmission resolved prior issues with the shifter’s reach, aligning it more naturally with the driver’s seating position. This change, alongside new pedal placements, offers a more intuitive and comfortable driving experience, crucial for long off-road excursions.
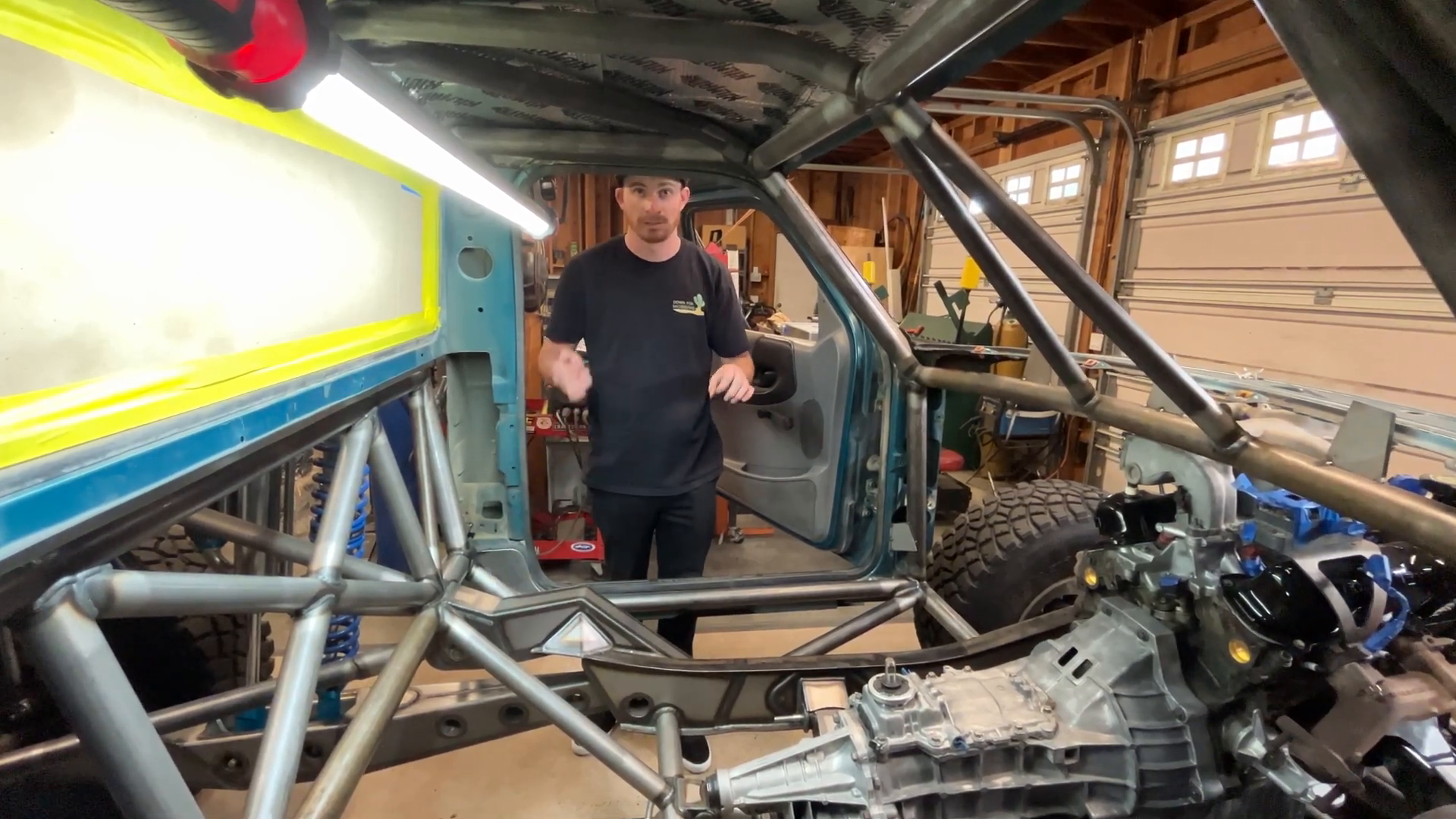
Custom Interior Fabrication
The interior is being reimagined with custom panels and seat mounts to accommodate the vehicle’s new layout. The removal of the factory flooring and firewall allows for a bespoke interior solution that is both functional and visually appealing. These adjustments will also ensure that all mechanical components are easily accessible for maintenance and adjustments.
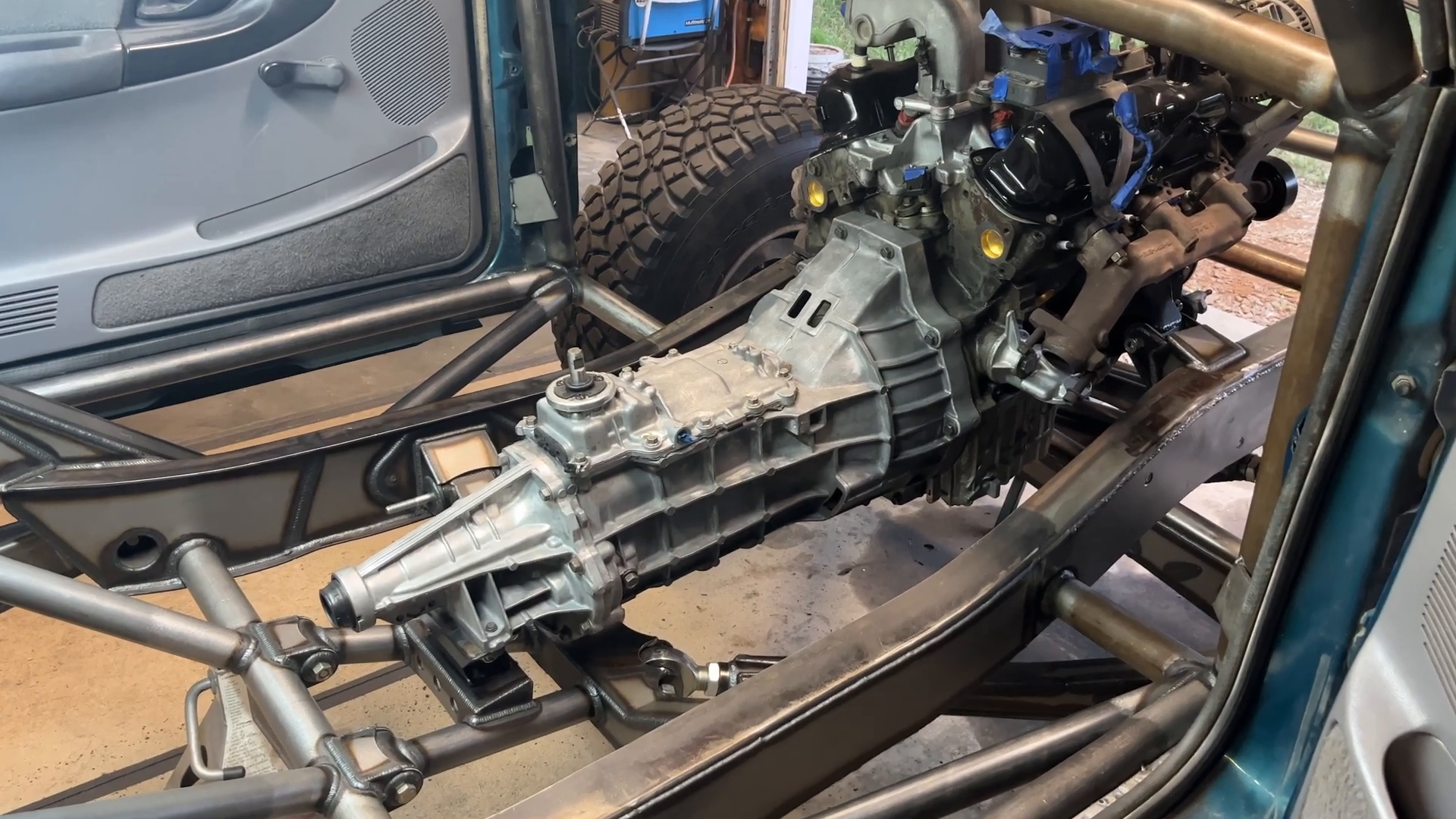
Rear Assembly and Storage Solutions
Storage and Weight Distribution
The rear section of the prerunner has been meticulously planned to ensure optimal weight distribution and utility. A Jack mount has been strategically placed to balance weight distribution, and custom containers for fluids and other essentials have been crafted to fit within available spaces. These elements are designed to be both practical and aesthetically pleasing, contributing to the vehicle’s overall efficiency and balance.
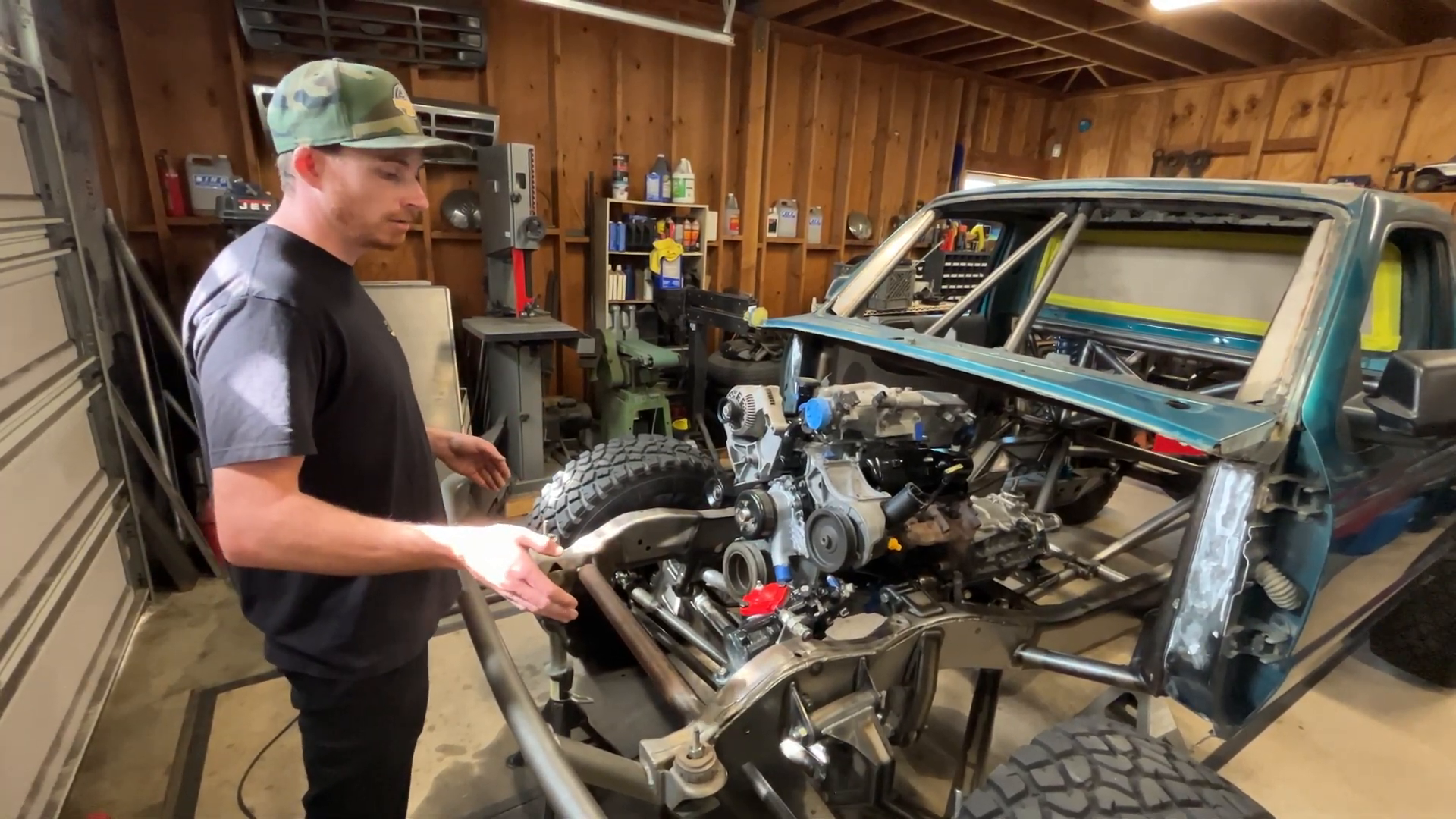
Fuel System and Electronics
The new fuel system is positioned at the rear, a choice made to improve weight distribution and ensure stability during high-speed maneuvers. Additionally, the fuel pump and filters have been discreetly integrated into the frame rails, leaving room for future electronic upgrades and facilitating easy access for maintenance tasks. The battery setup is designed to provide balanced power distribution, with considerations for future electronic enhancements.
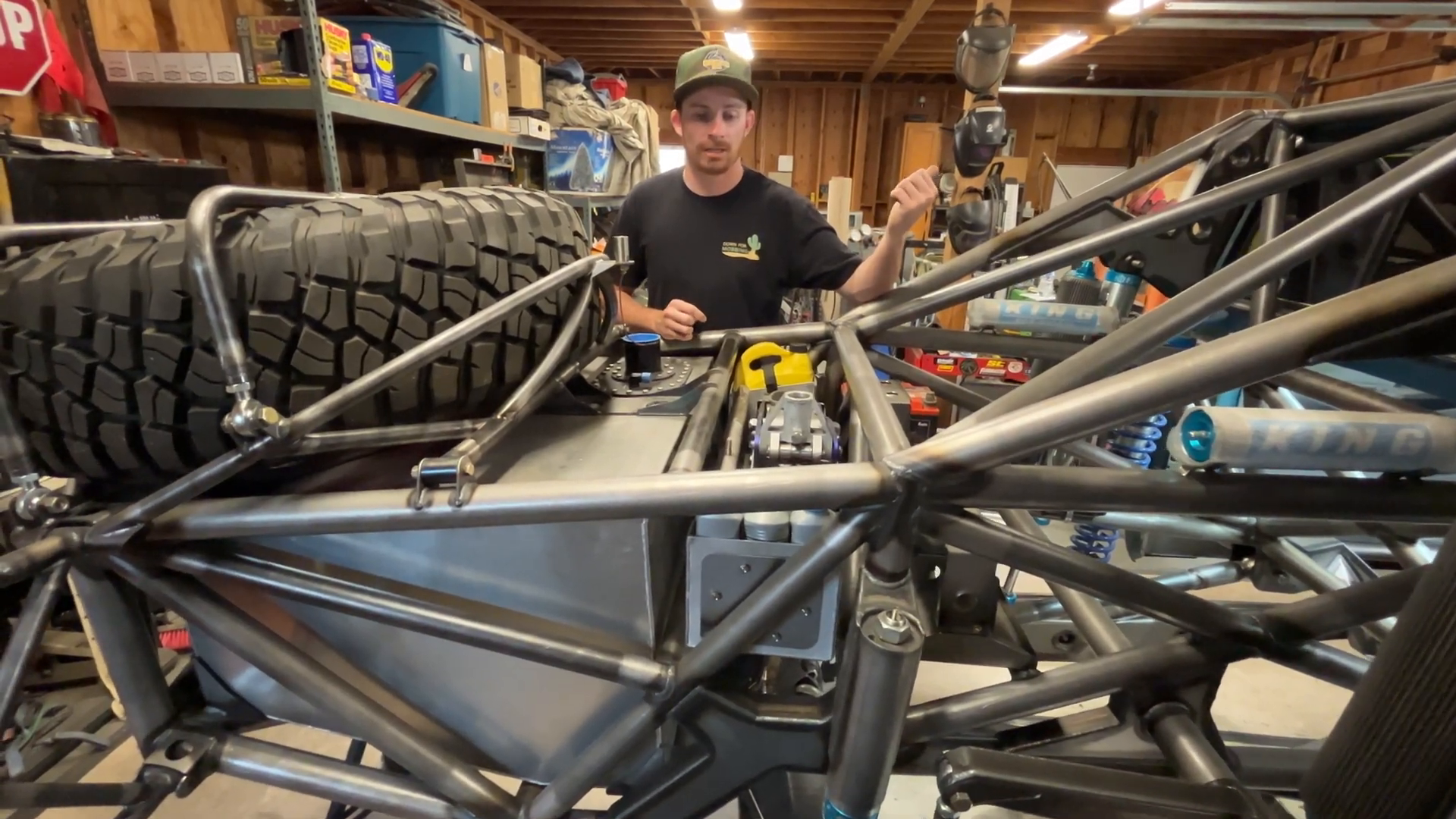
Challenges and Considerations
Engineering and Design Challenges
The project has faced various engineering challenges, particularly concerning space constraints and component clearance. The narrow track width of the ranger required precise engineering to ensure that components like the suspension and steering systems fit correctly without sacrificing performance or safety. These challenges necessitated innovative solutions, such as clocking the top caps of shock absorbers to prevent hood interference.
Future Considerations
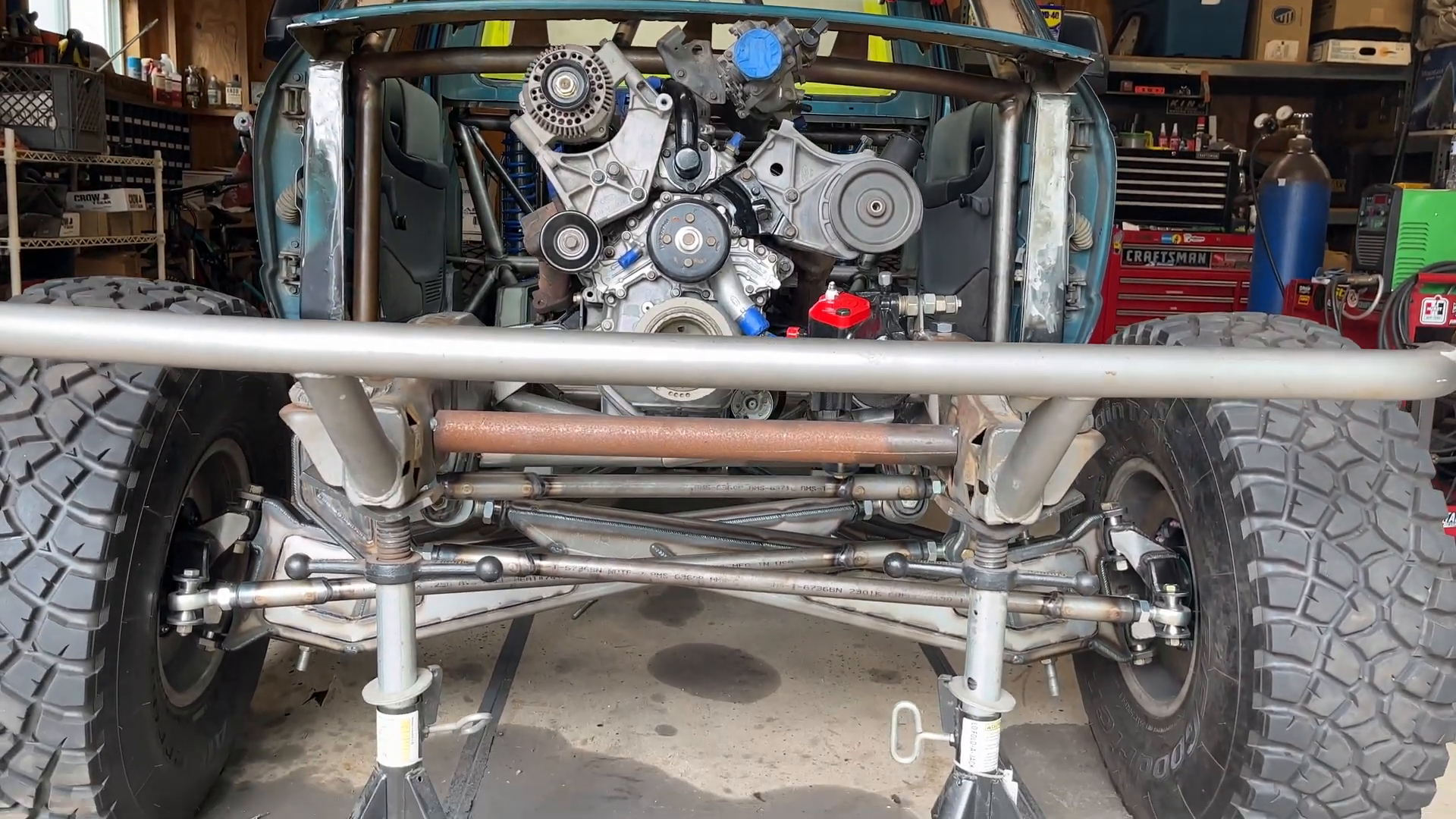
While the current build is focused on maximizing the performance of the existing V6 engine, considerations have been made for future upgrades. The radiator and engine mounts are designed to accommodate a potential V8 engine swap, ensuring that the vehicle remains versatile and adaptable to future needs. This forward-thinking approach ensures that the truck can evolve alongside the owner’s ambitions and requirements.
This comprehensive build process showcases the intricacies involved in crafting a high-performance prerunner. Attention to detail, precise engineering, and a commitment to quality have driven the modifications, resulting in a vehicle that is not only capable of conquering the harshest terrains but also tailored to the specific needs and preferences of its owner. As the build progresses, it will continue to push the boundaries of custom automotive engineering, setting new standards in the off-road community.
Categorized in: Trucks