Ranger Prerunner Build Part 5: Rear-End Modifications and Enhancements
In the latest update on a custom Ford Ranger build, the team at Vital Designs, led by Christian, has been working diligently on the truck’s rear half. This project involves intricate modifications and custom designs aimed at enhancing the vehicle’s performance and functionality. The focus of this update includes installing bump stops, a sway bar, a fuel cell, and preparations for the jack and bedsides. Each component requires careful consideration of design, functionality, and ease of maintenance.
Installing the Bump Stops
Mounting and Design Considerations
The installation of bump stops is a crucial element in absorbing shock and protecting the suspension system during off-road excursions. The team opted for a simple, clean boxed mount design. The bump stops were mounted without the Delrin pad initially to facilitate better alignment. Once the shocks were fully bottomed out, the pads were reattached to ensure proper spacing between the bypass and the coilovers. This meticulous setup ensures that nothing bottoms out, providing a more reliable and efficient suspension system.
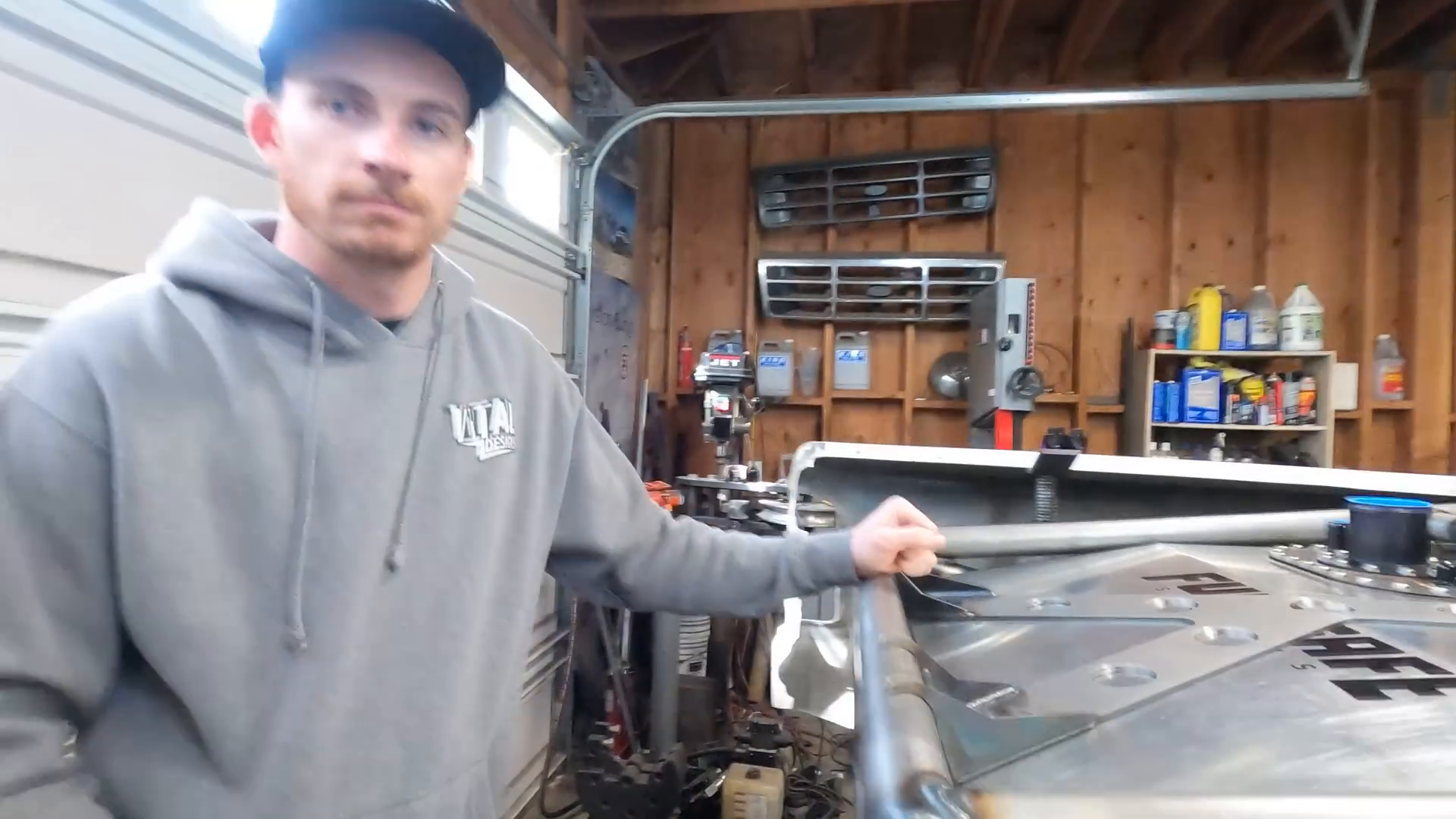
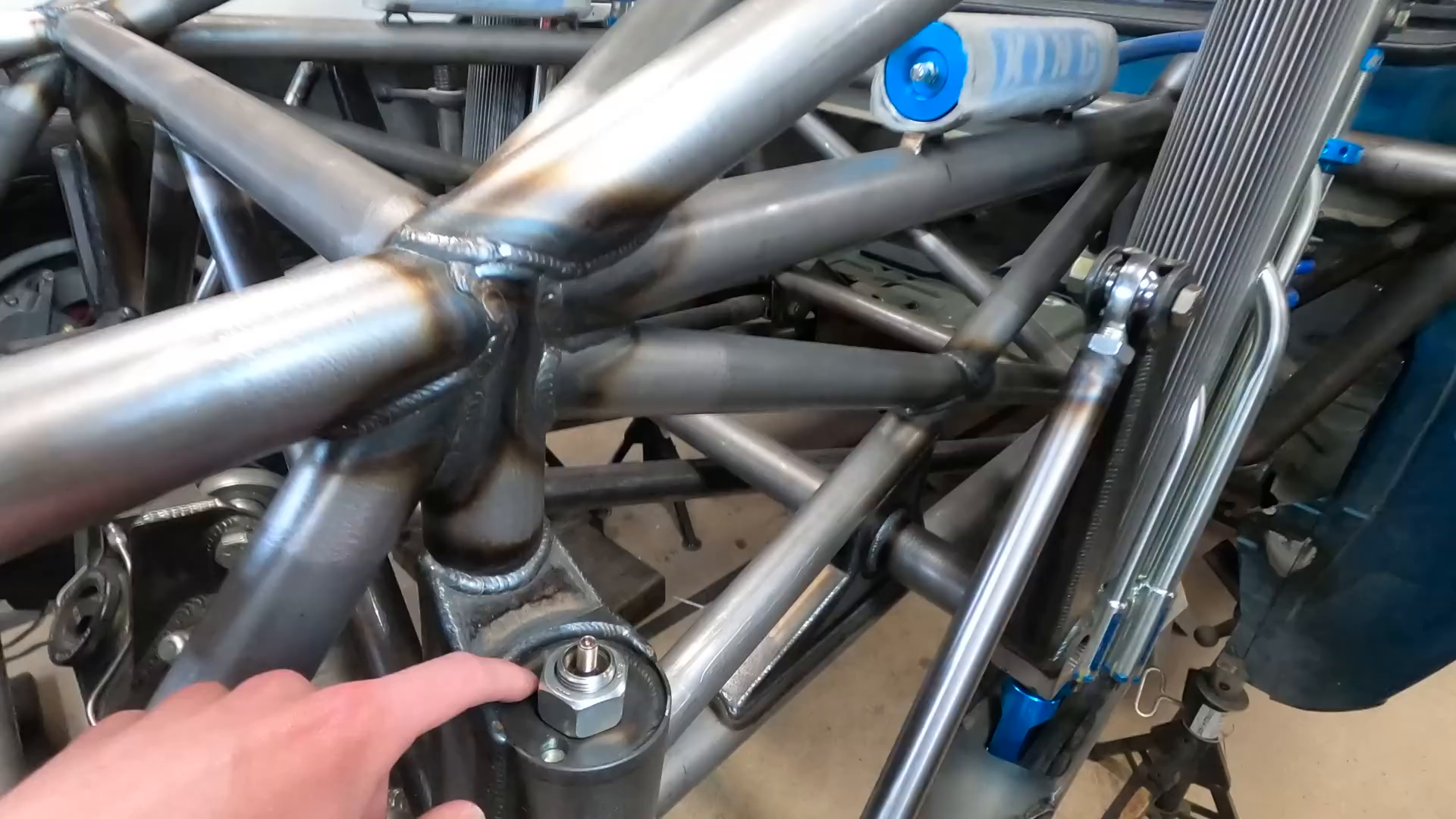
Challenges and Solutions
One of the challenges faced was maintaining the alignment and stability of the bump stops during installation. By removing the Delrin pad, the team could achieve a more precise fit, reducing the potential for misalignment. This method simplifies the process, especially for those tackling such modifications for the first time. Additionally, the bump stops were designed to be a consumable, replaceable part, allowing for easier maintenance and increased longevity of the suspension system.
Custom Sway Bar Installation
Addressing Packaging Constraints
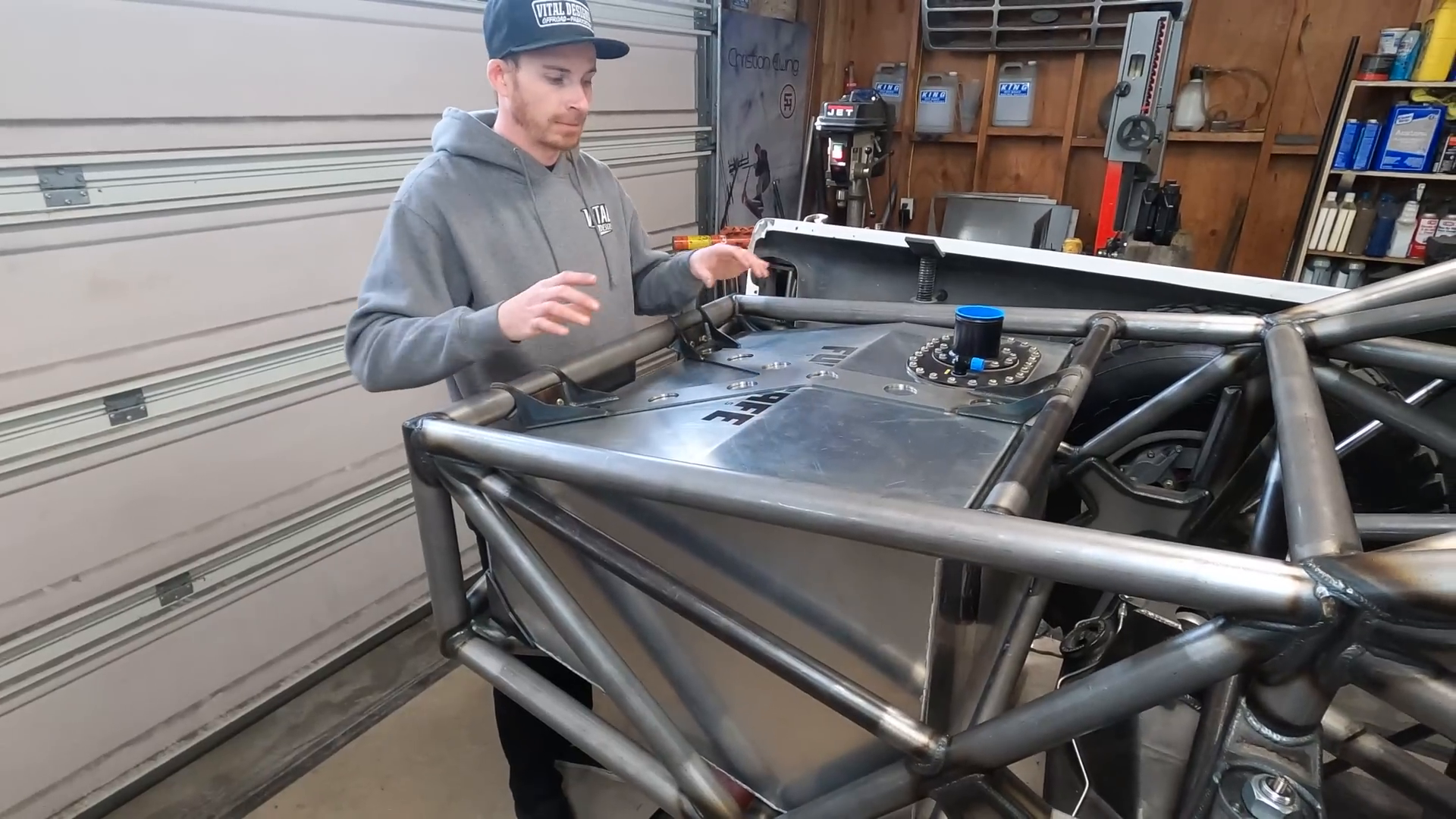
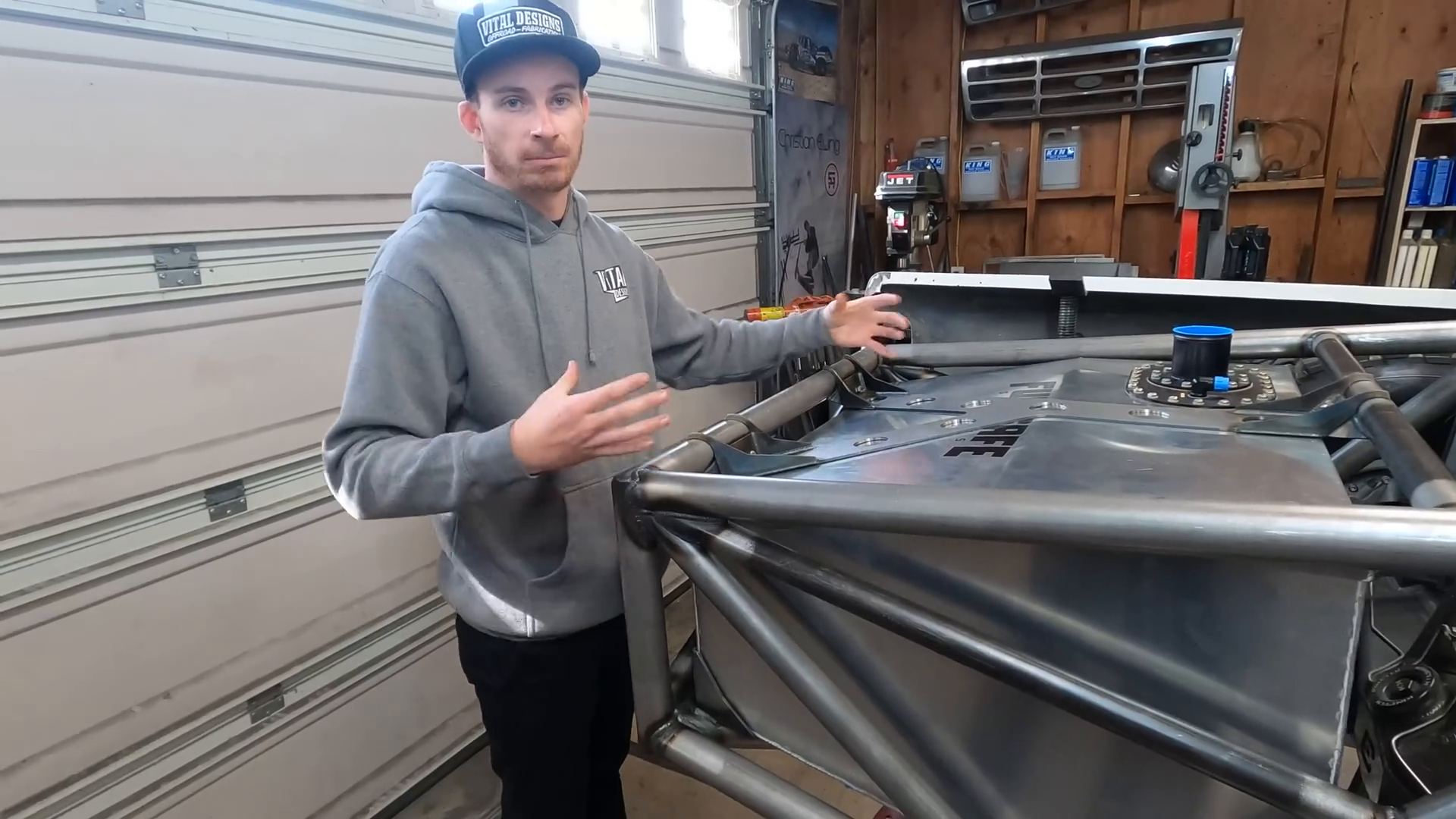
The sway bar’s installation was another complex task, primarily due to the limited space available. The decision to mount the sway bar at the front was driven by packaging constraints, as the original design concept had to accommodate spare tires on the sides of the fuel cell. This change necessitated a unique approach to fitting the sway bar within the available space.
Design and Functionality
To ensure optimal performance, the sway bar’s design had to align with the overall aesthetics and functionality of the truck. The team used a two-inch, 120-wall tube to mount the torsion bar, incorporating Delrin bushings for smooth motion. The sway bar’s performance is affected by the torsion bar’s rate, arm length, and angle, all of which were carefully considered to prevent binding and ensure maximum wheel travel.
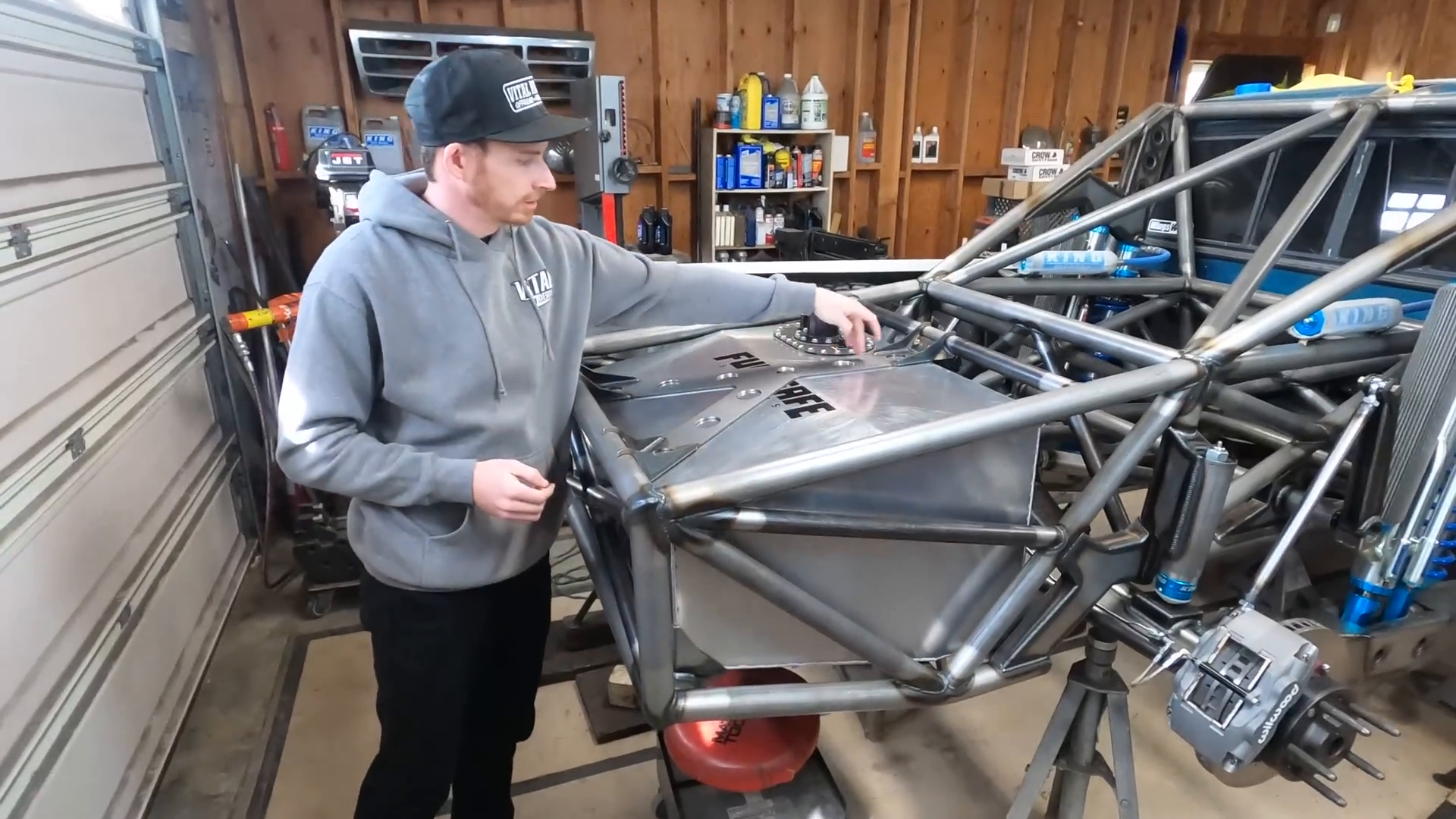
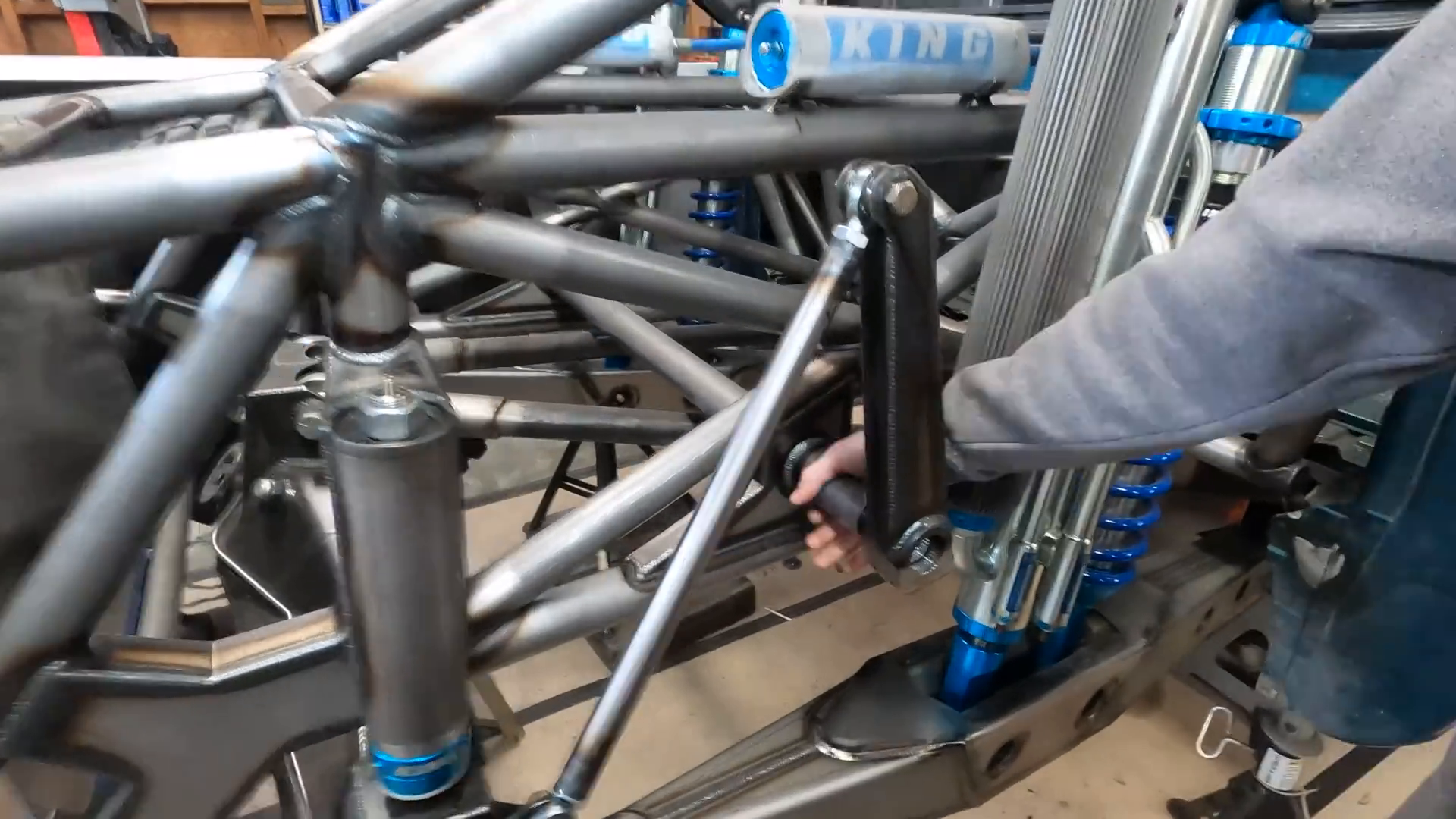
Fuel Cell Mounting
Design Approach and Challenges
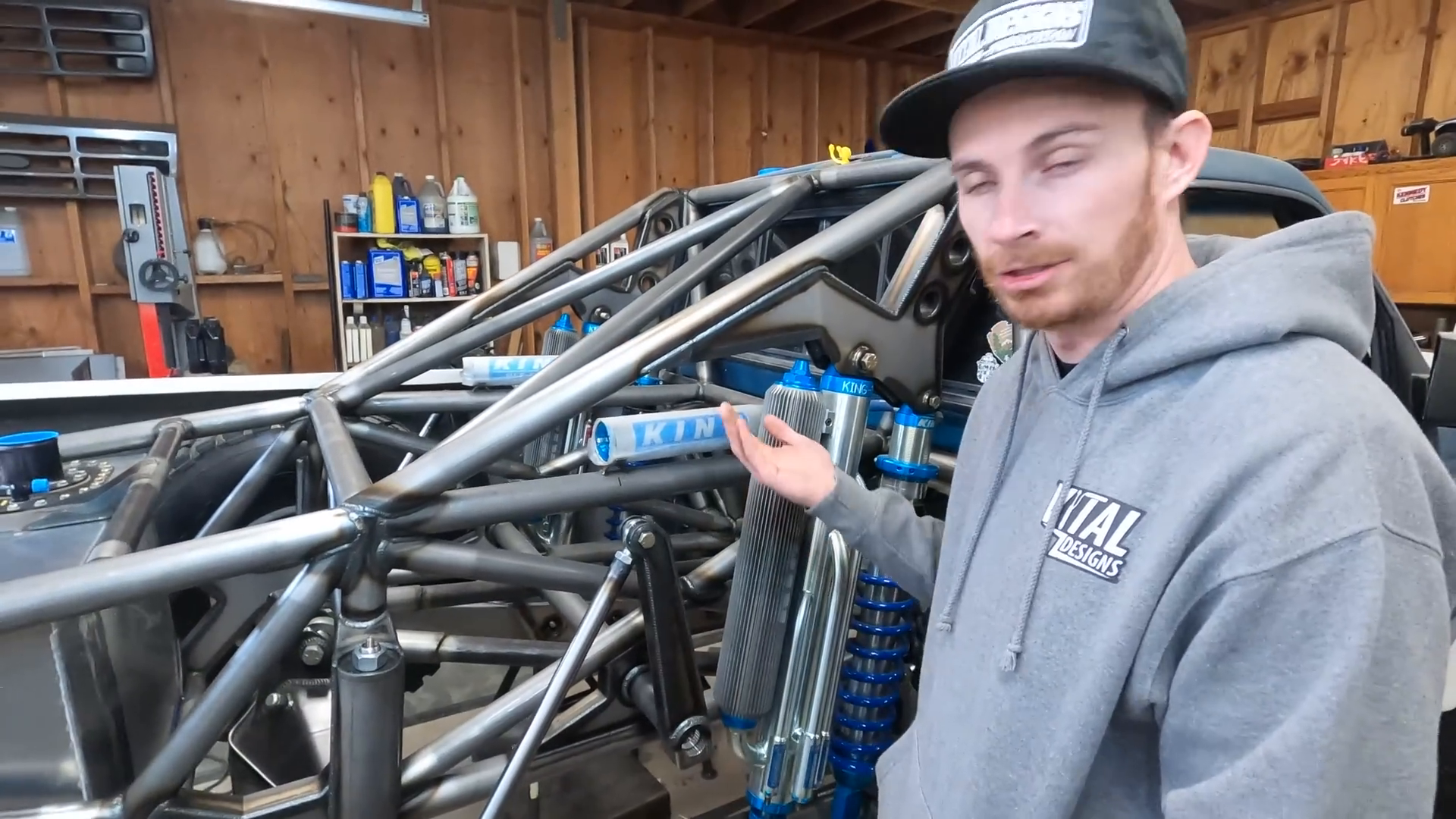
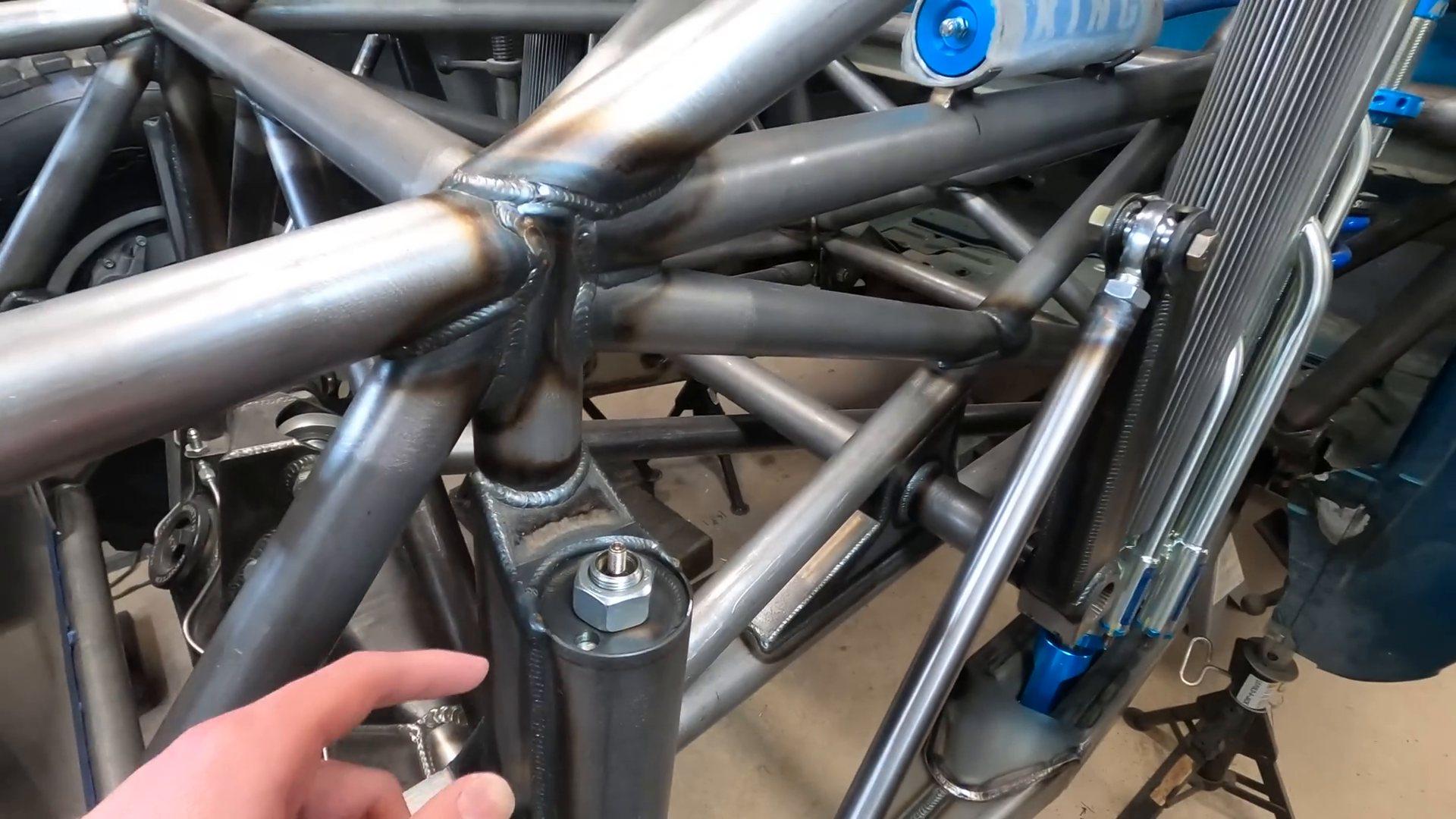
The fuel cell, another essential component, was mounted using a plate-based design, departing from the traditional tube structure. This decision was made to simplify the installation and improve the packaging within the truck’s rear end. Proper placement and support for the fuel cell are critical, as any structural weakness could lead to failure over time.
Ensuring Durability
The fuel cell’s bottom is supported by the truck’s structural tubes, preventing it from bowing out due to the load. This approach ensures the longevity of the fuel cell, protecting the plastic bladder from stress and potential cracking. The design also facilitates easy removal for maintenance, reflecting the team’s focus on practical, user-friendly solutions.
Additional Modifications and Future Plans
Coilover Reservoir Mounting
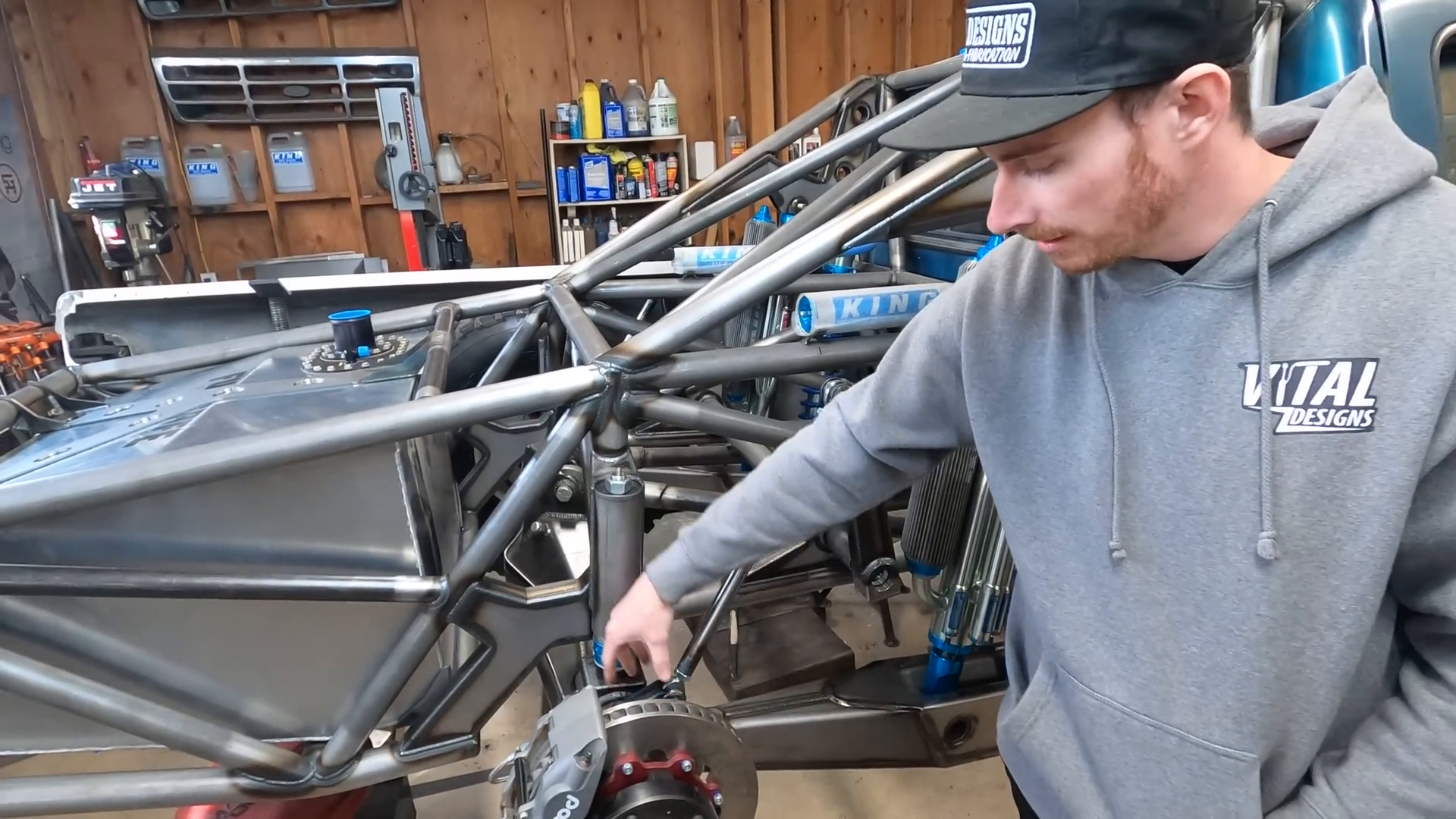
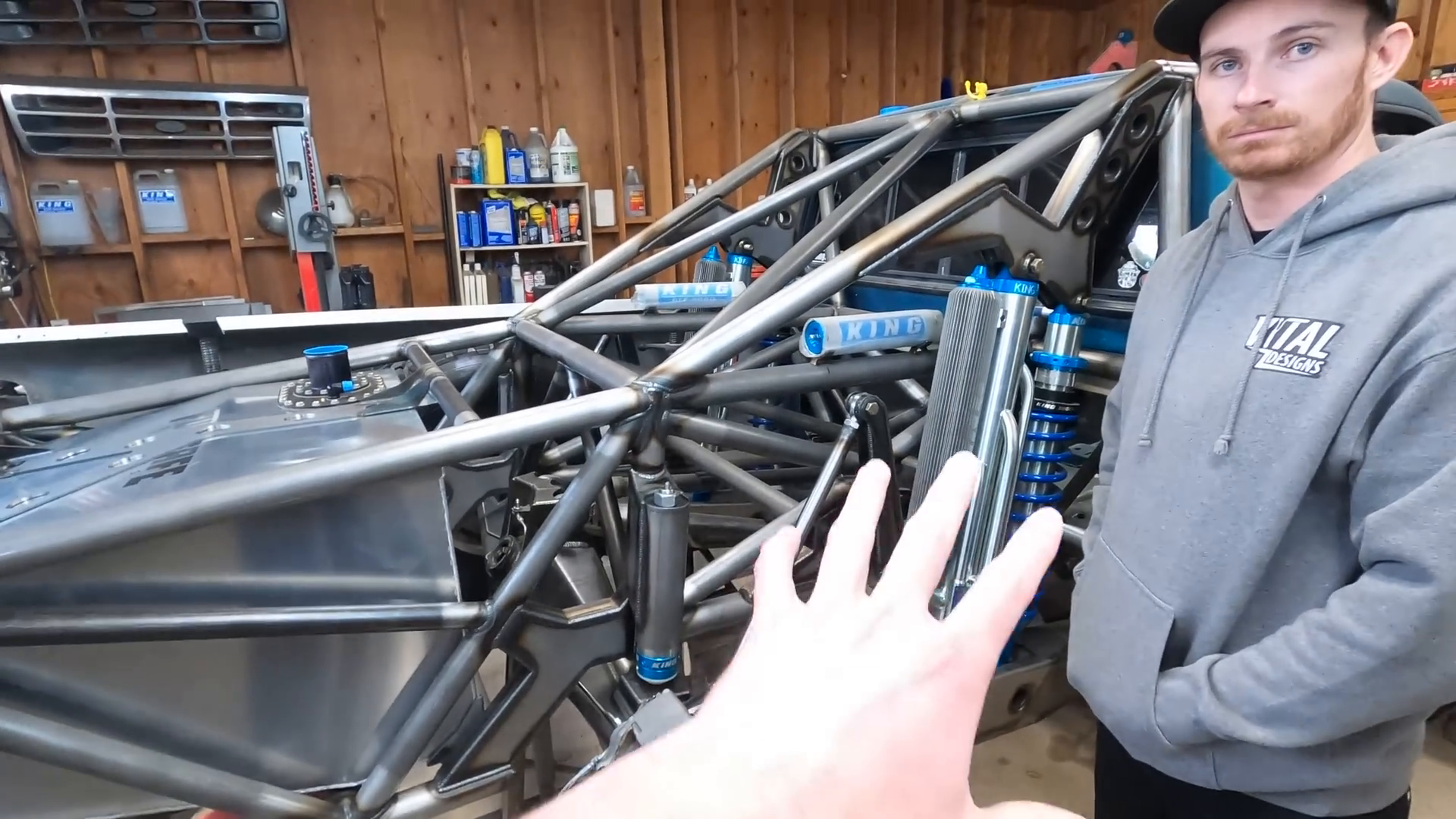
The team has also mounted the coilover reservoirs using clamp-style mounts, which are preferred for their durability and clean appearance. This method prevents damage to the reservoirs and ensures they remain securely attached to the chassis.
Jack and Bedside Mounting
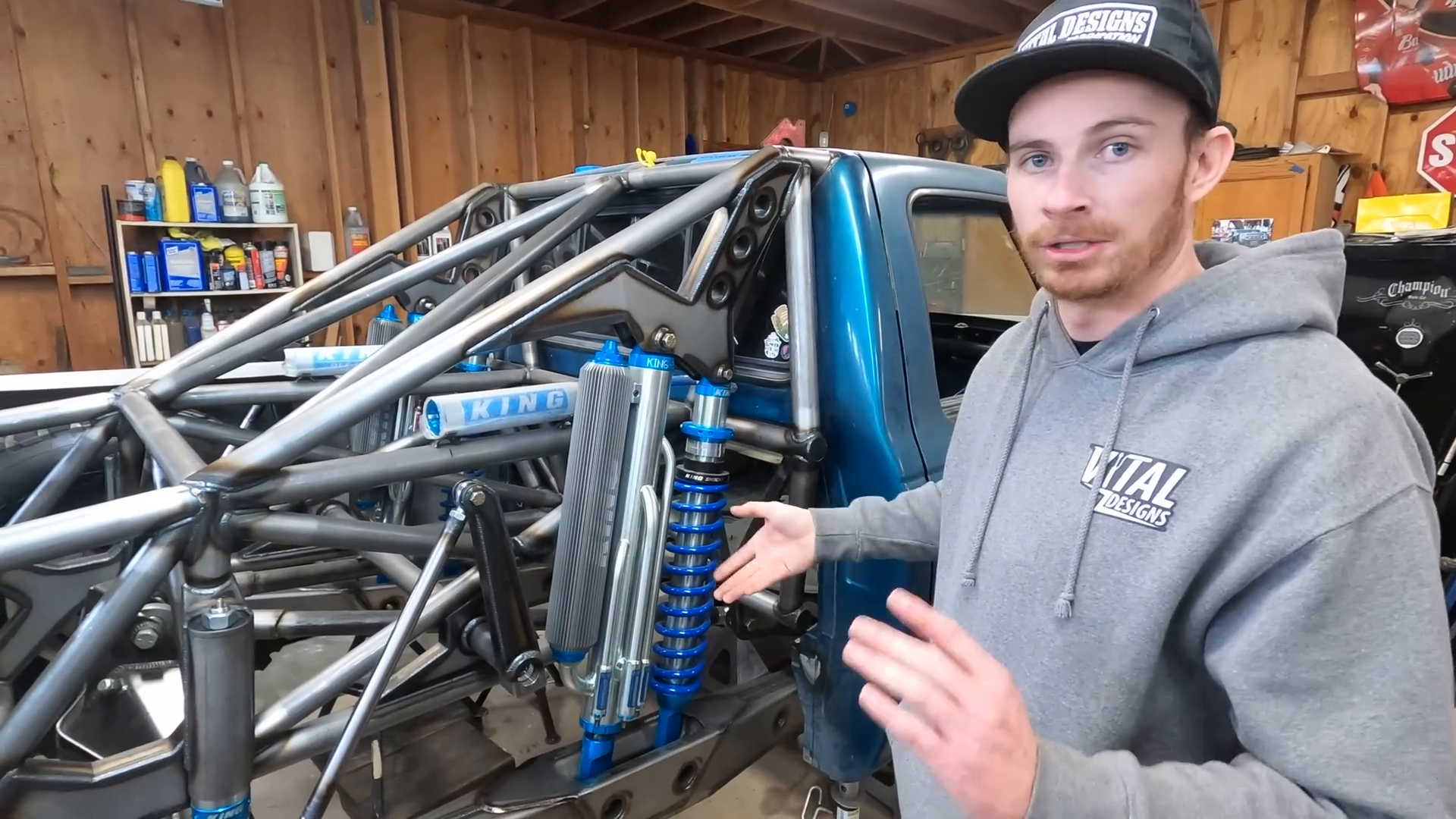
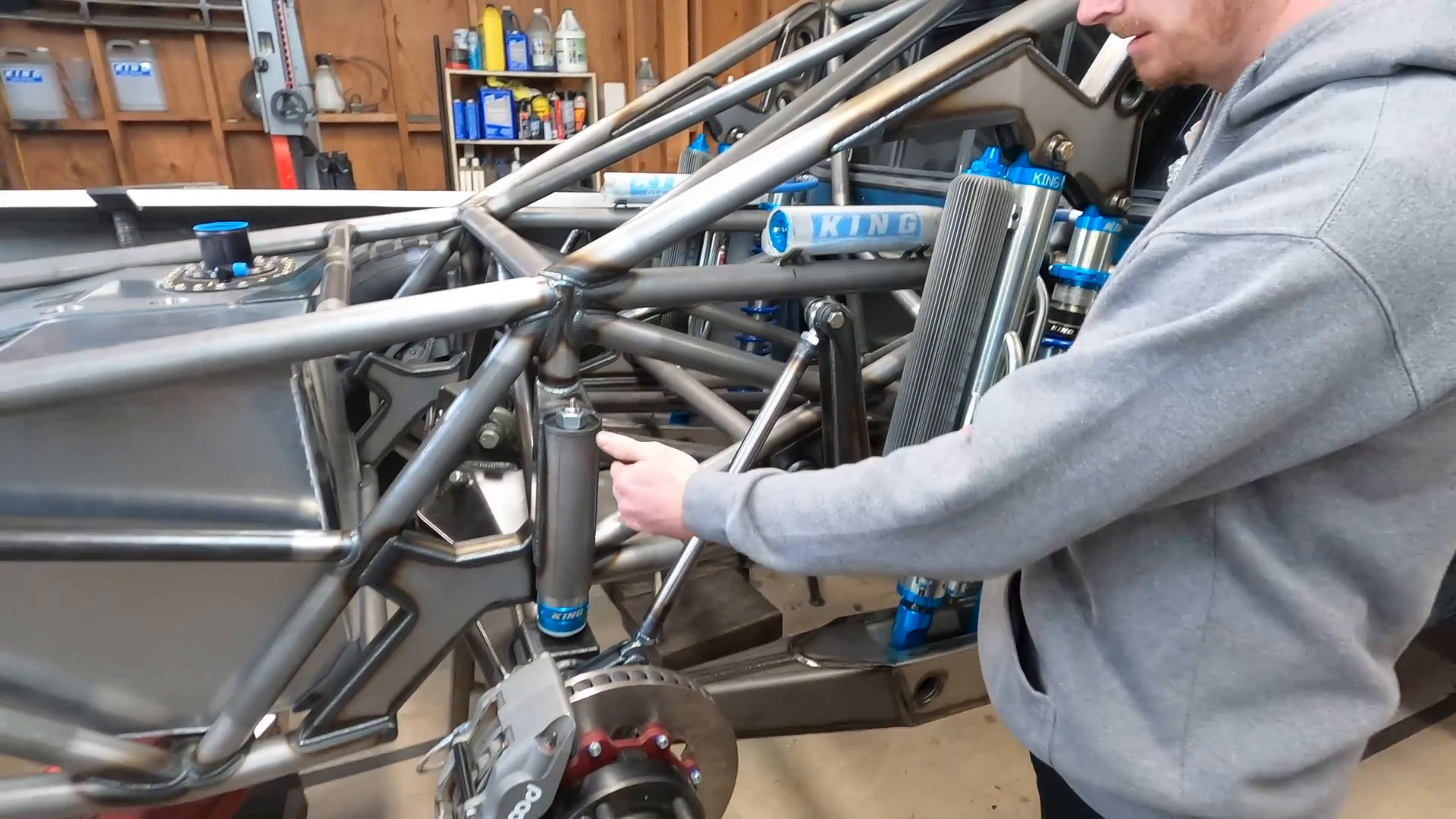
Christian has initiated the design for a jack mount, which will be discreetly housed in a sealed compartment. This design protects the jack from environmental wear while keeping it easily accessible. Additionally, the truck will soon feature mounted bedsides, which are being designed to seamlessly integrate with the rest of the vehicle.
Looking Ahead
As the build progresses, the focus will shift towards finishing the cab and starting work on the front end. The goal is to complete the major structural elements before delving into the more intricate details, such as panel work and final touches. This approach allows for significant strides in the project’s development, keeping the build on track for future testing and validation.
The meticulous work being done on this Ford Ranger is a testament to the importance of combining design aesthetics with functional engineering. As the build continues, it will serve as a valuable reference for those interested in custom vehicle modifications, offering insights into the challenges and solutions involved in such a complex project.
Categorized in: DIY, Fabrication, Ford, Prerunners