Ranger Prerunner Build Part 4: Engineering Insights for the Prerunner Project
The prerunner project continues to evolve, with the team making significant progress on the Ranger’s modifications. Bill, a key figure in the build, has been instrumental in executing the updates. The focus of the recent work has been on the plate structure and shock mounts, which are critical to the vehicle’s performance and durability.
Since the last update, the team has made strides in finalizing the fuel cell cradle, which now features a new tube integration for enhanced structural integrity. The cradle design is unique, ensuring that the project stands out while maintaining functionality. This balance of aesthetics and performance is vital in automotive builds, especially in off-road vehicles like prerunners.
Design and Fabrication Techniques
Plate Work and Structural Integrity
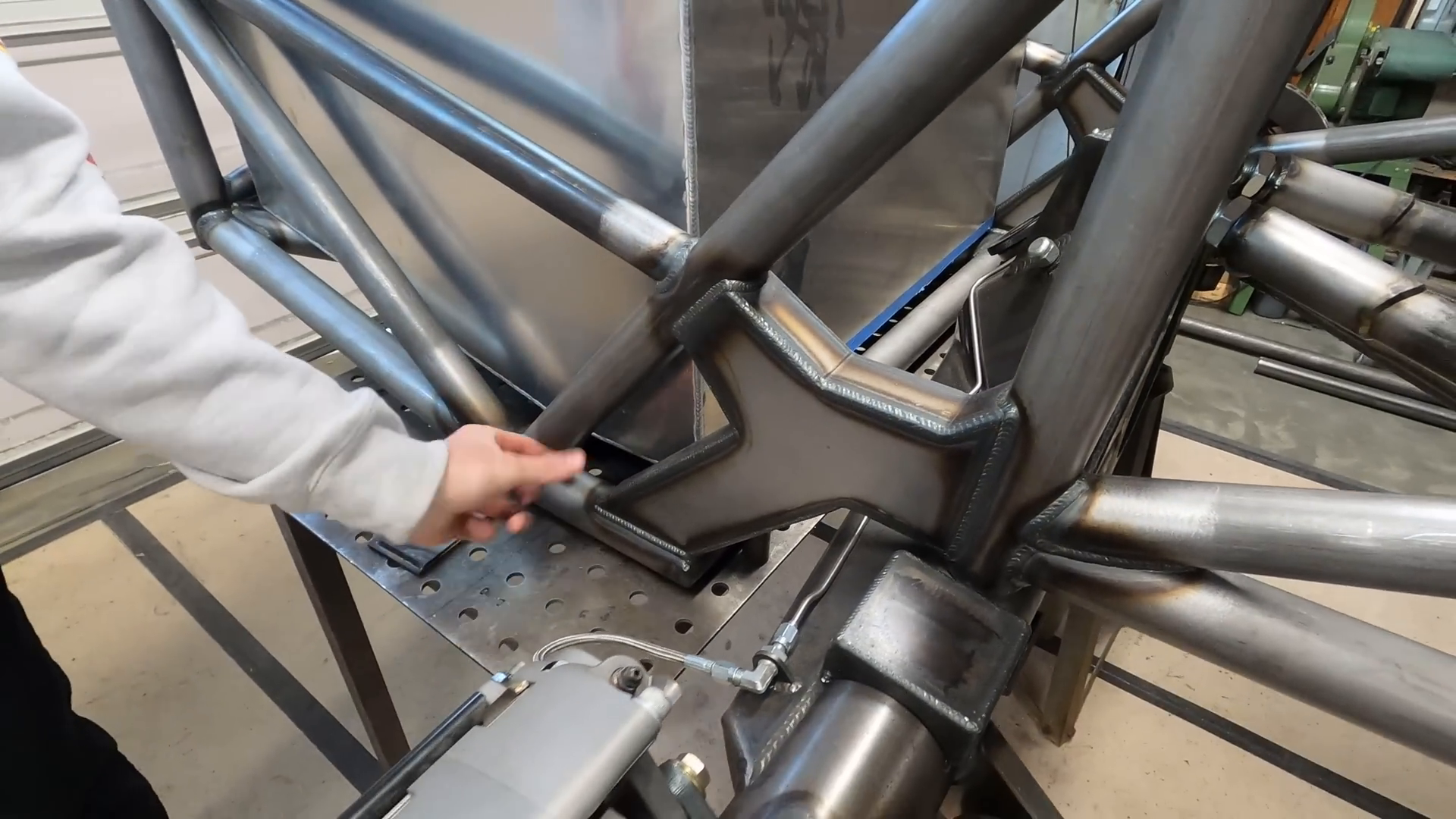
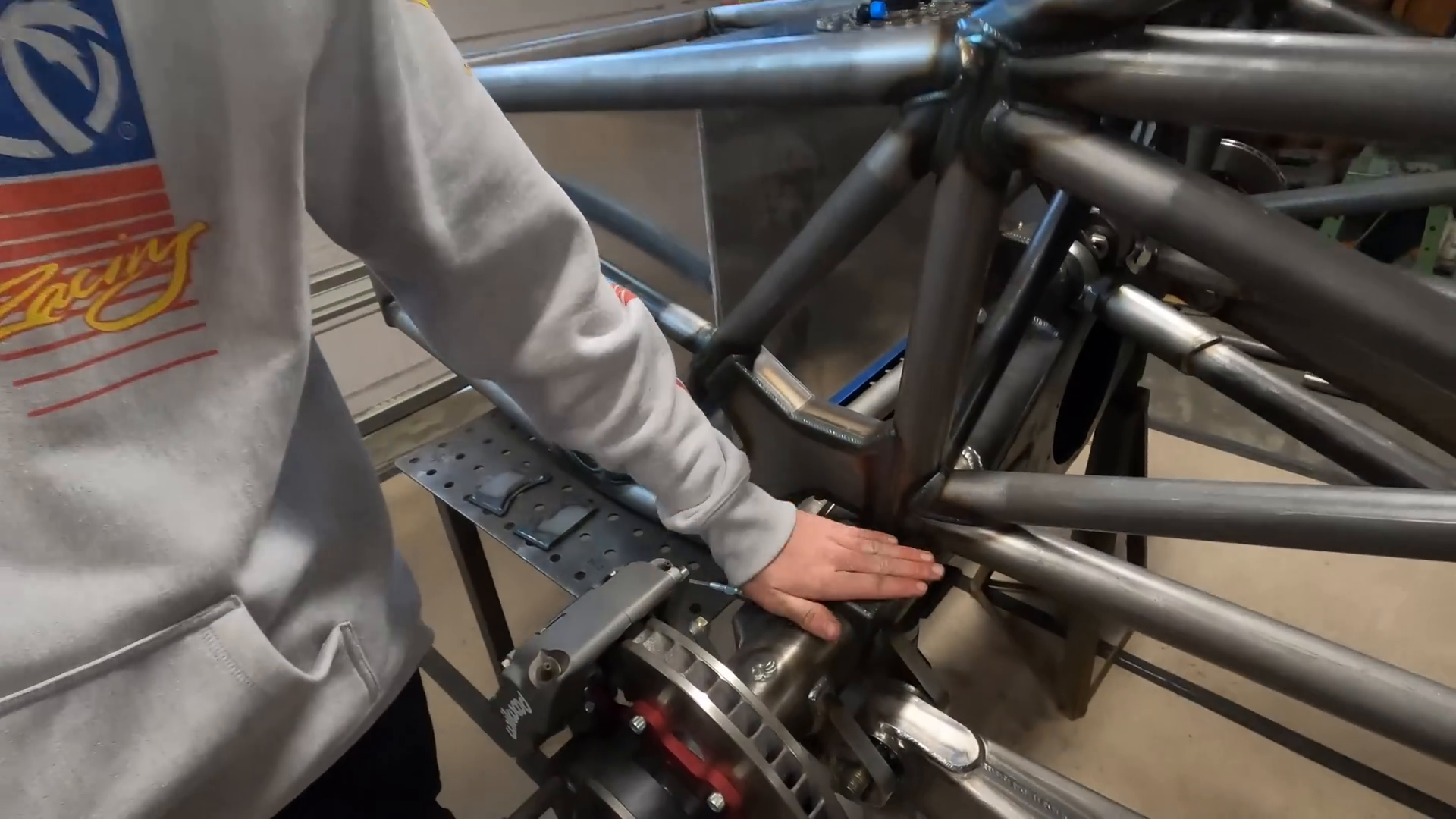
The team began by determining the shape and design of the necessary plate structures. Using Ram Board, a versatile material for creating templates, they sketched out potential designs. This approach allows for flexibility and creativity, ensuring the final product not only fits perfectly but also complements the overall design vision.
For the shock mounts, the importance of using the full stroke of the shocks was emphasized. The bypass shocks in use are position-sensitive, meaning they have different zones that the piston traverses. Ensuring that these zones are used correctly is crucial for optimal performance. Off-the-shelf shocks typically require careful consideration of setup to maximize their effectiveness.
Advanced Fabrication Techniques
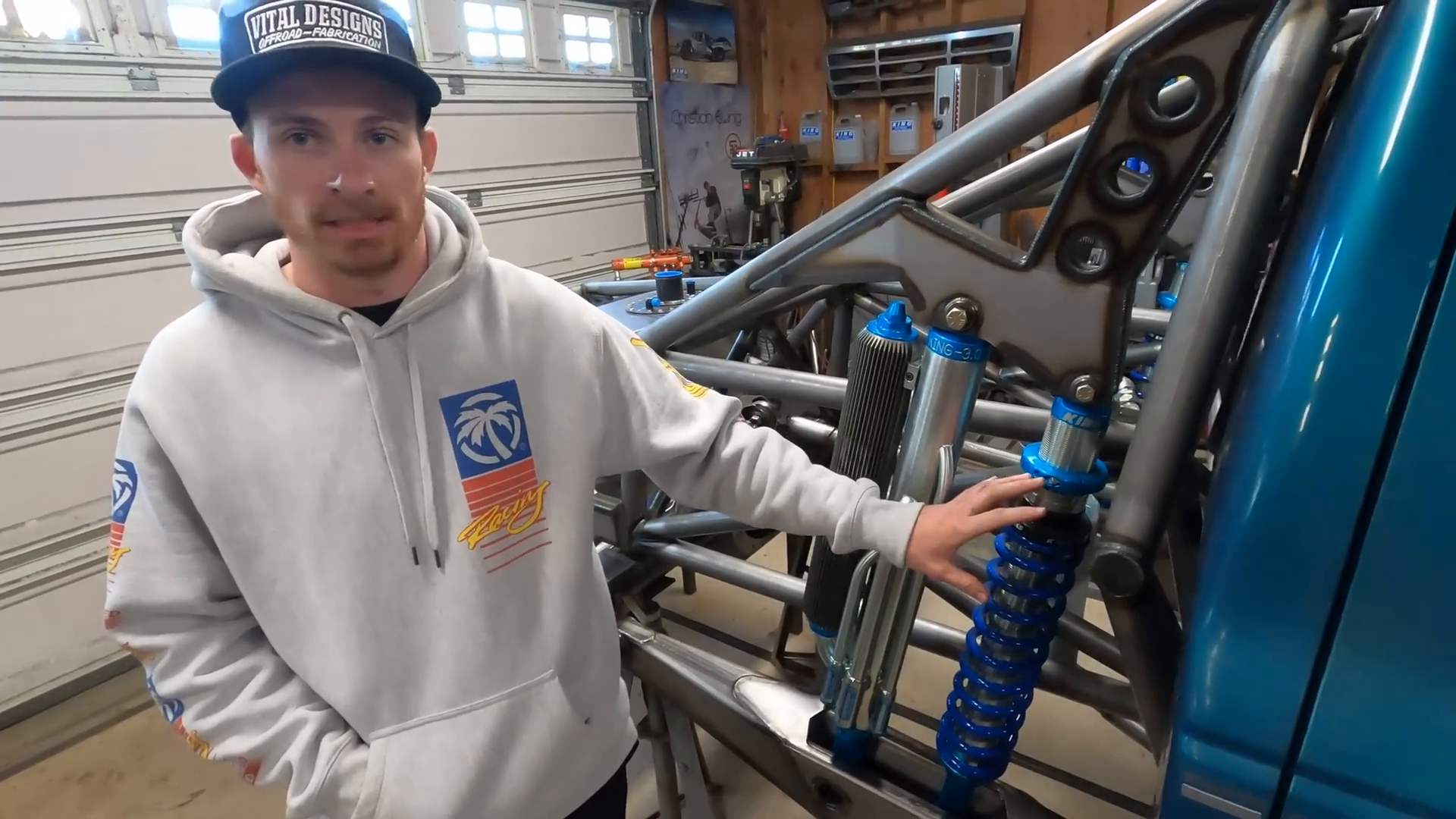
One innovative technique mentioned is the use of computer-aided design (CAD) to translate hand-drawn templates into precise digital models. This process involves photographing the Ram Board templates, uploading them into design software like Fusion 360, and tracing them to create detailed models that can be cut accurately. This method combines traditional craftsmanship with modern technology, allowing for precise fabrication of components that may not initially be modeled in CAD.
Shock Mounts and Bump Stops
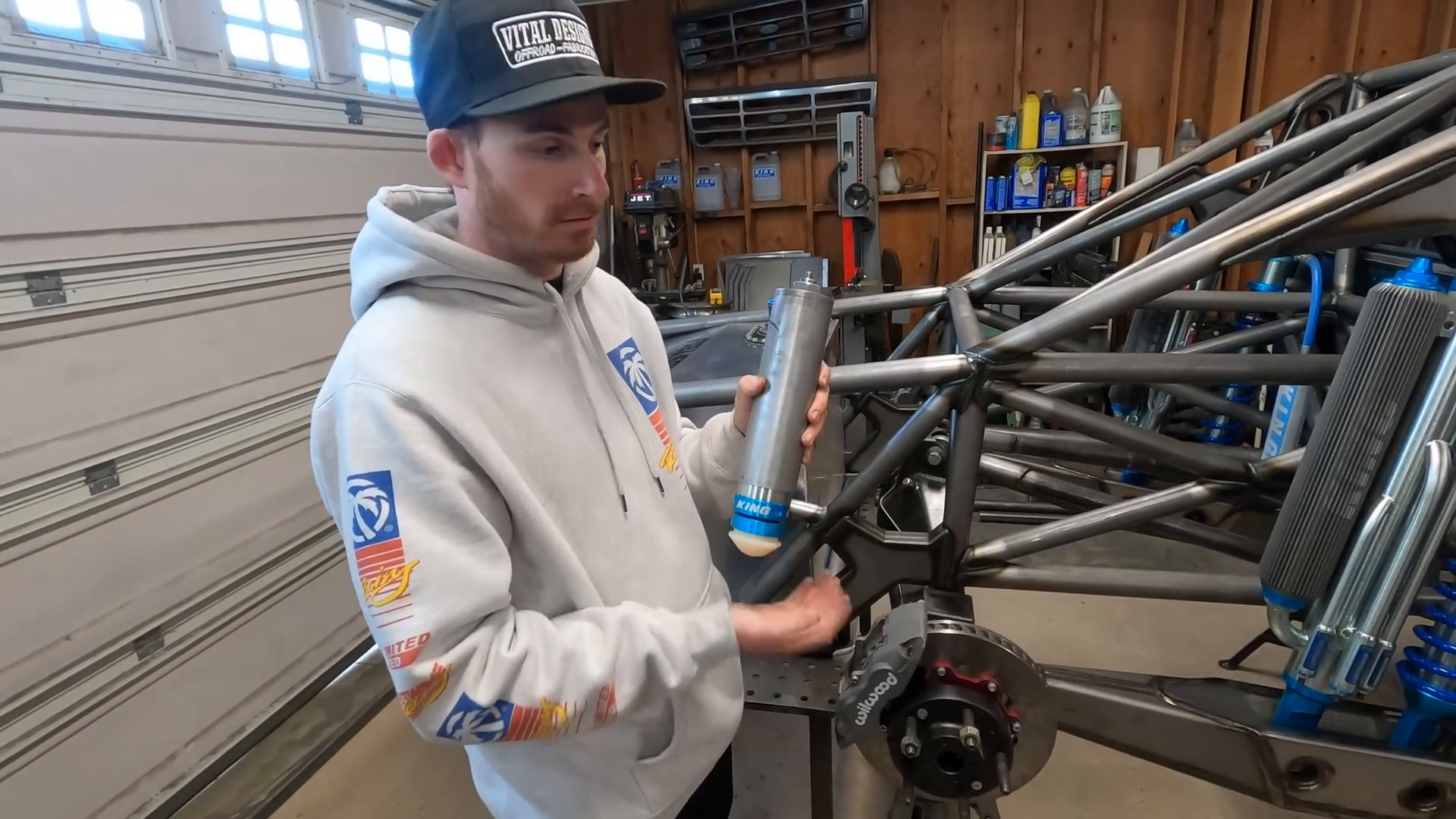
Engineering Considerations
The newly designed shock mounts are robust and aesthetically pleasing, made possible through careful planning and digital modeling. Weld washers were employed to reinforce the bolt holes, preventing wear and ensuring long-term reliability. This attention to detail is crucial in high-stress components like shock mounts.
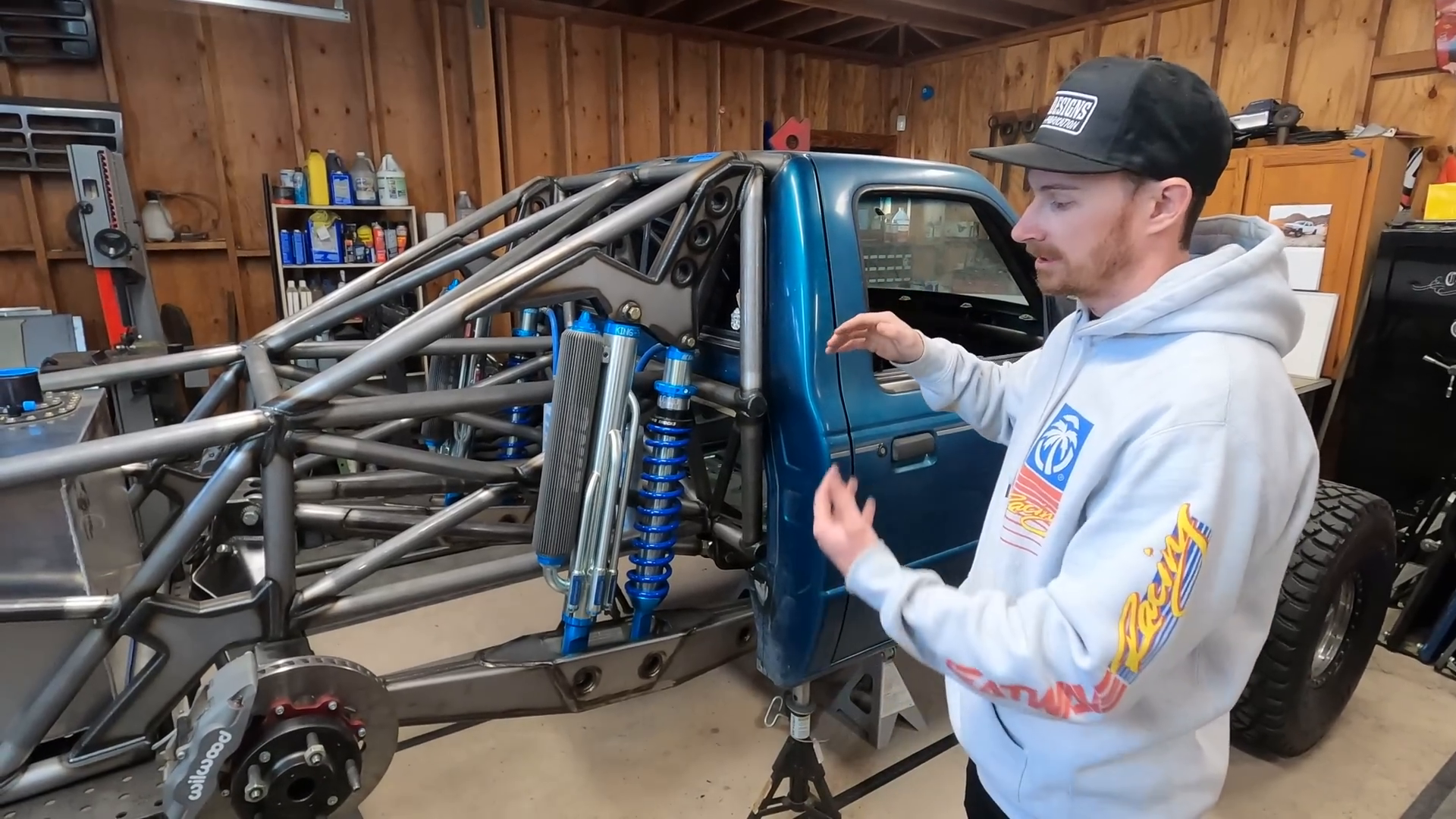
Additionally, the bump stops were designed with a focus on durability. The team included a center rib in the design to prevent deformation from repeated impacts. This strengthening measure ensures that the bump stops effectively protect the shocks from fully collapsing, which could lead to damage over time.
Custom Modifications and Adjustments
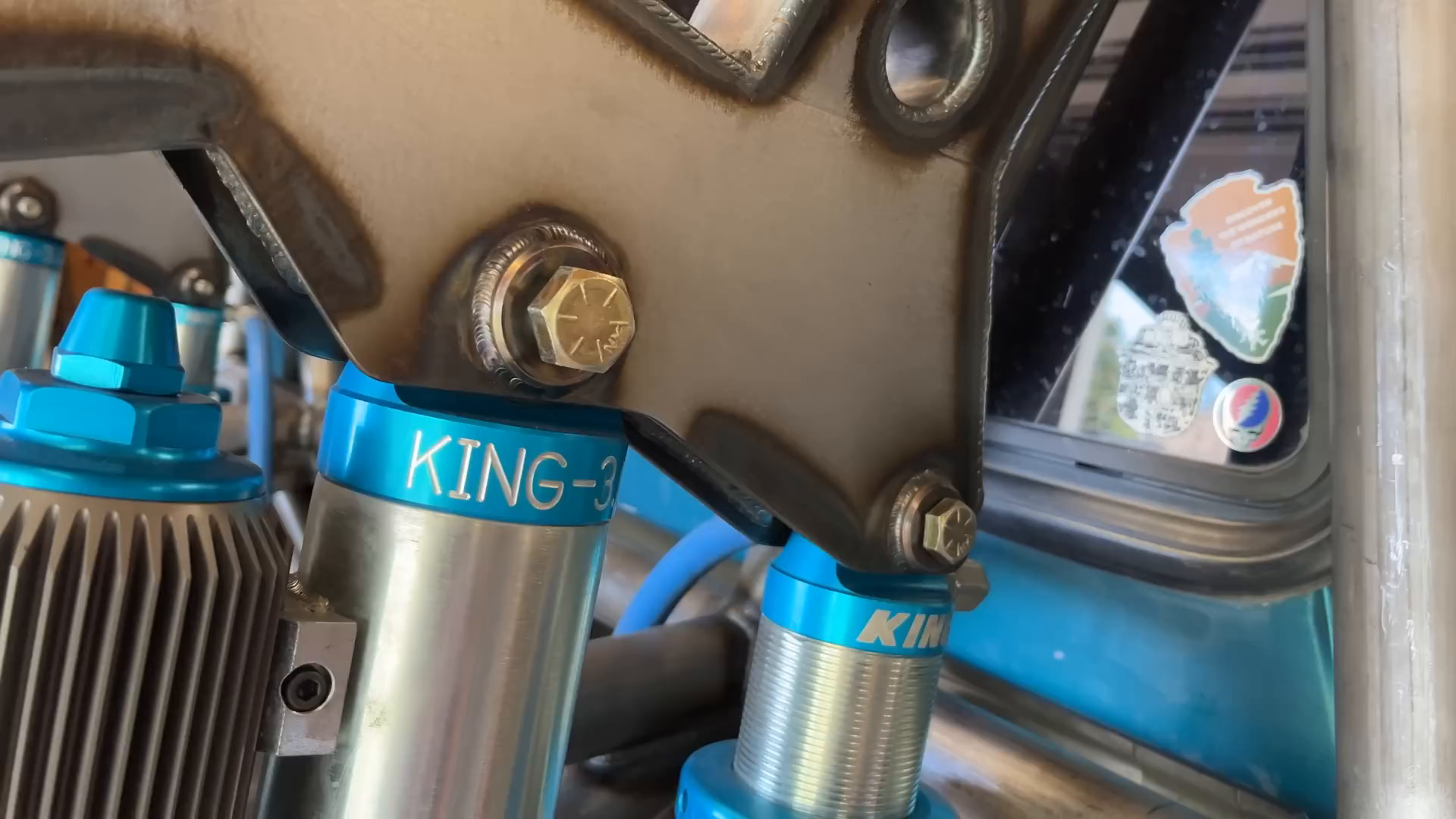
Throughout the process, adjustments were made to ensure the best possible alignment and performance. For example, the trailing arms were repositioned to improve the alignment of the shocks and provide additional clearance for future upgrades. This foresight allows for flexibility in the build, accommodating potential changes in shock size or configuration down the line.
Integrating Personal Style and Functionality
One of the project’s goals is to create a prerunner that not only performs exceptionally well but also reflects the unique style and preferences of its builders. By customizing the plate work and tube structures, the team has managed to create a distinctive look that sets the vehicle apart from others while maintaining its practical capabilities.
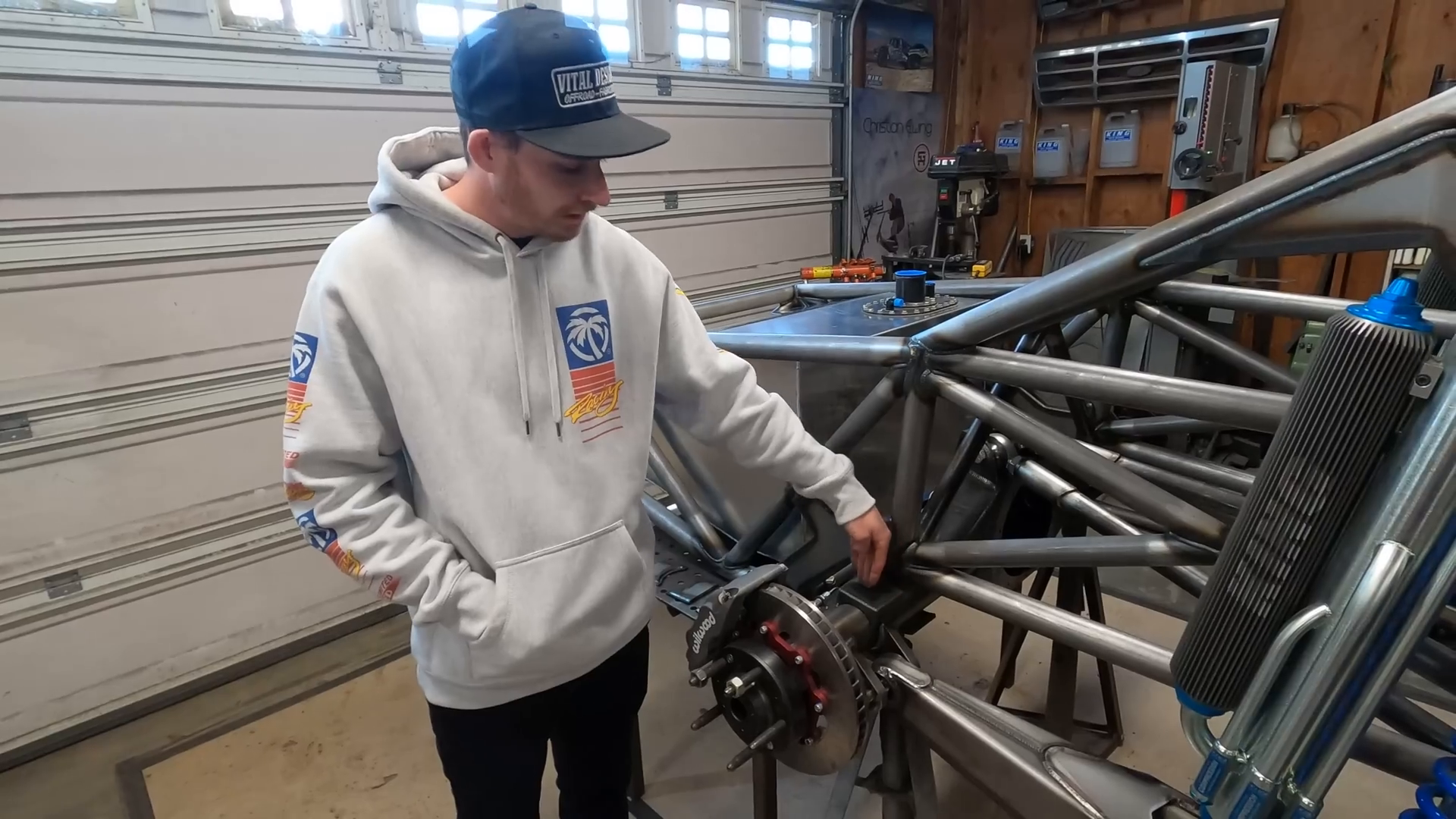
The integration of personal style into a functional build is a hallmark of custom automotive projects. It requires a deep understanding of both engineering principles and aesthetic design, allowing the builder to achieve a harmonious blend of form and function.
Future Steps and Considerations
Moving forward, the team aims to complete the rear of the truck, ensuring all components are finalized and fully functional before the vehicle is placed on its own weight. This involves additional bracing and welding to ensure the structural integrity of the frame and suspension components.
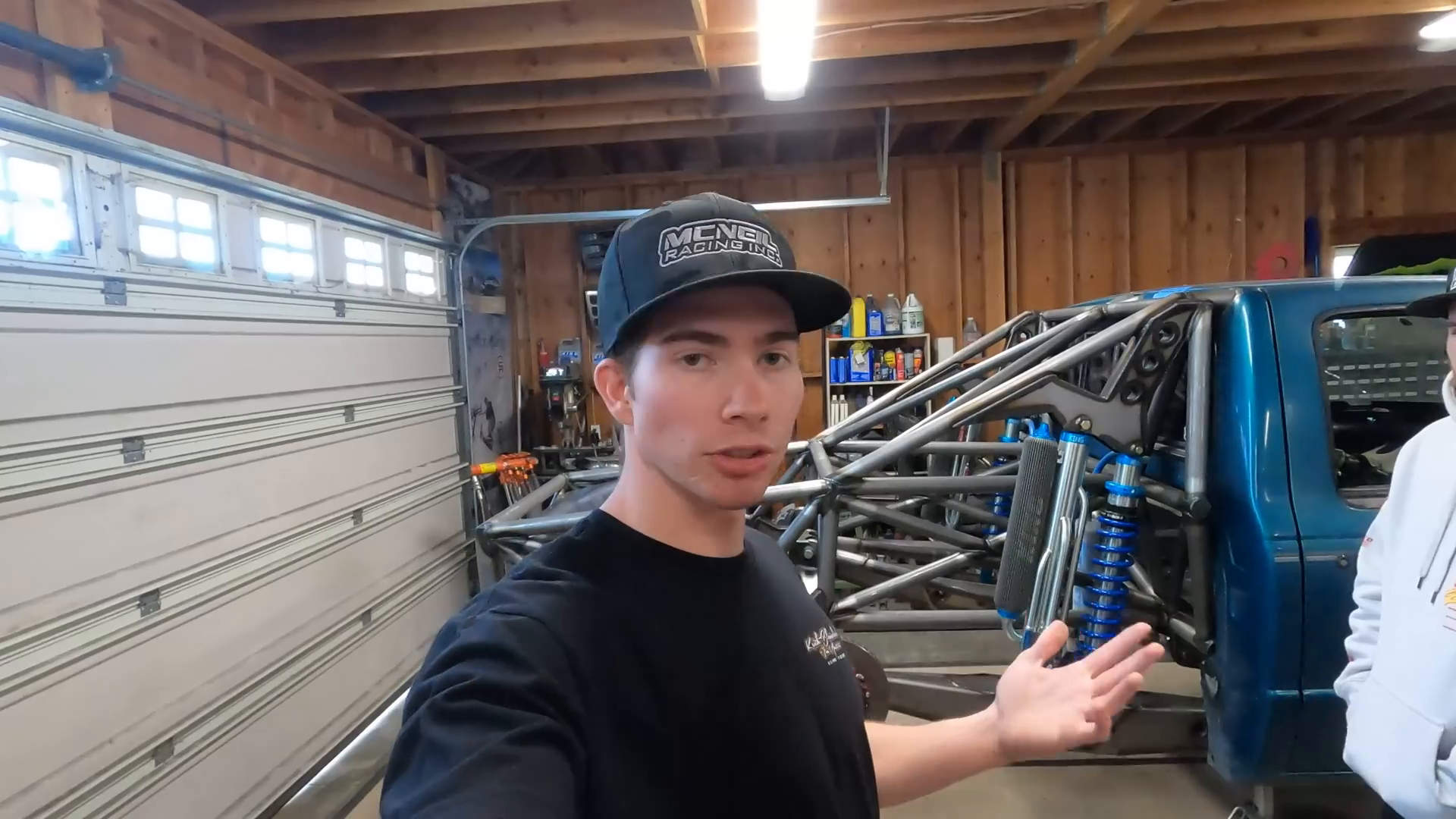
Attention will also be directed towards the sway bar setup, which will be mounted in a unique position to maximize packaging efficiency and performance. This innovative approach highlights the team’s commitment to pushing the boundaries of conventional design and engineering solutions.
As the project progresses, the importance of meticulous planning and execution becomes increasingly evident. Each decision and modification is carefully considered to ensure that the final product not only meets but exceeds the expectations of its builders and potential users.
Categorized in: DIY, Fabrication, Ford