Inside an Built for Dirt’s Off Road Fabrication Shop
@BuiltForDirt‘s fabrication shop serves as a hub for various projects, particularly those related to Jeep and off-road vehicle modifications. This space provides a deep dive into the various tools, machinery, and methods employed by the skilled fabricators who work there. From welding to cutting, the shop is equipped with state-of-the-art machinery and seasoned professionals who are dedicated to bringing innovative projects to life.
The Fabrication Area: A Closer Look
Metal Stock and Storage
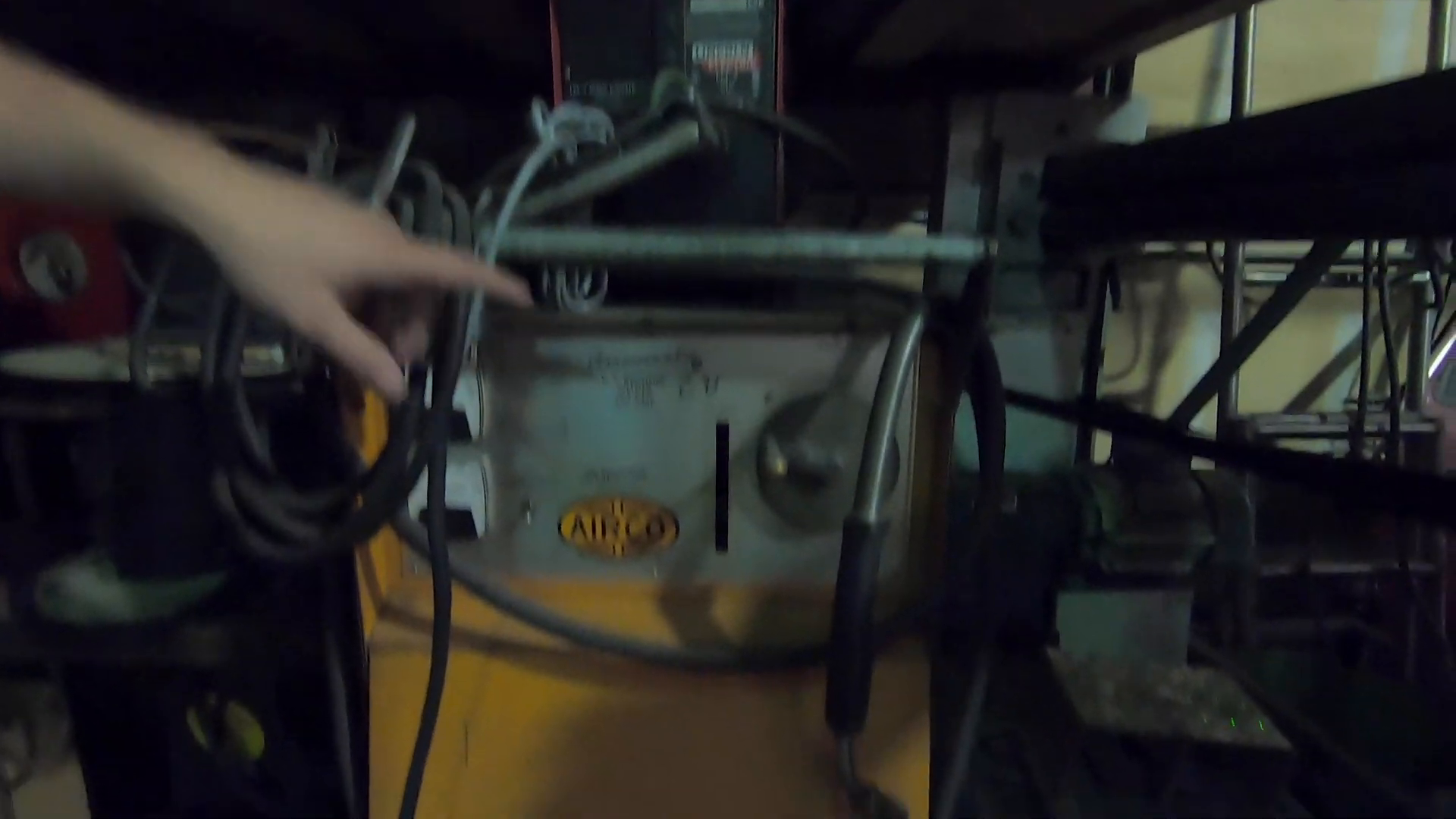
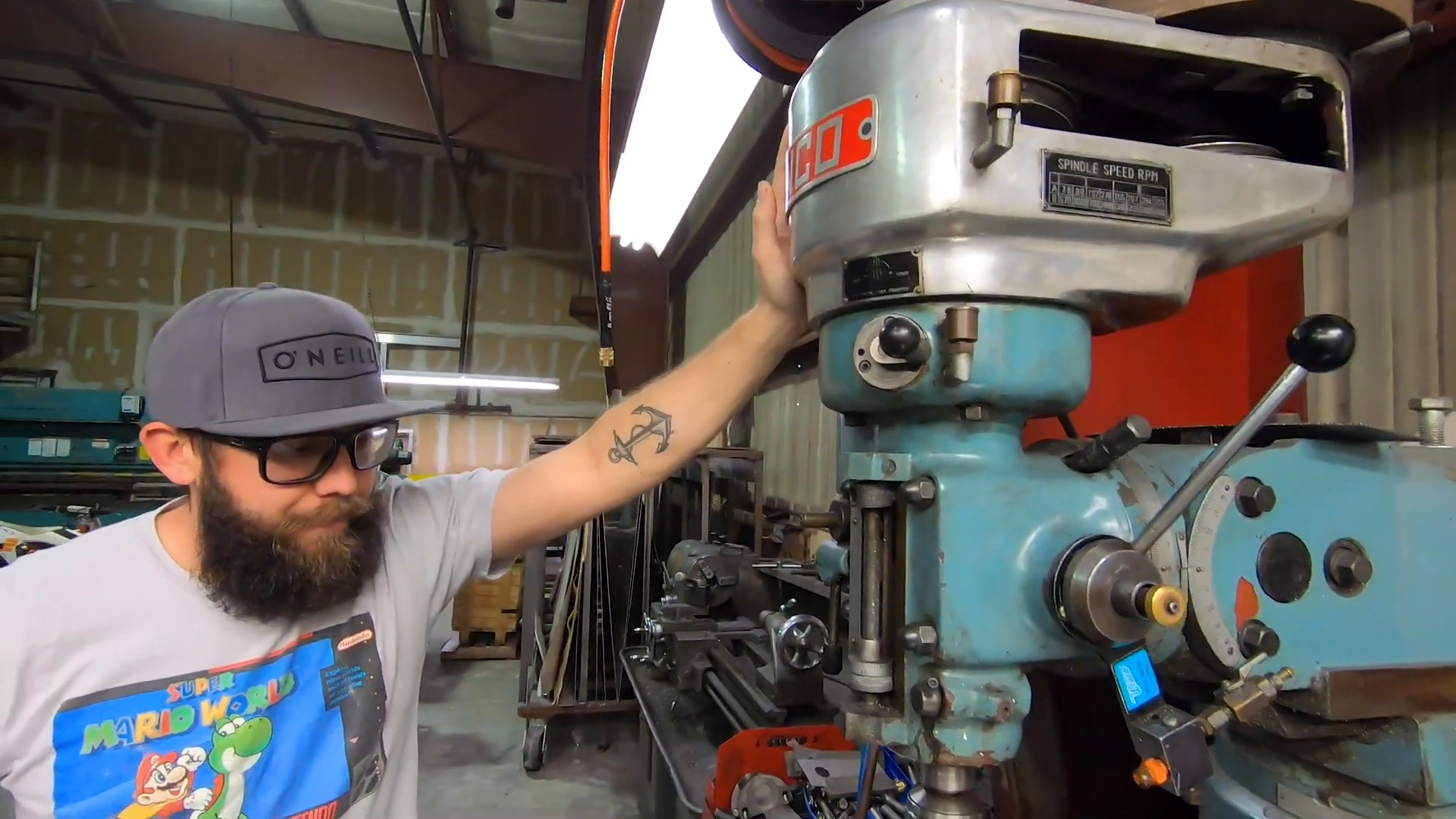
The shop houses an impressive steel rack that primarily contains stainless steel used in the wine industry. While the primary material is stainless steel, the shop also stocks mild steel for diverse projects. This variety allows the team to respond swiftly to emergency projects, ensuring they have the right materials on hand for a wide range of tasks.
Welding Stations and Equipment
The shop is equipped with several welding stations, each designed for specific tasks. The Miller Dynasty 210 and 280 TIG welders are central to the shop’s operations, enabling precise and powerful welding solutions. These machines are paired with wireless foot pedals, reducing clutter and risk in the workspace. The shop boasts advanced water-cooled setups to keep torches cool during extensive welding sessions, enhancing efficiency and safety.
Tools of the Trade: Bandsaws, Grinders, and More
Bandsaw and Cutting Tools
Material cutting begins at the shop’s bandsaw, an old but reliable DoAll machine. Known for its durability, this bandsaw handles a significant volume of material, proving its worth time and again. The availability of both mild and stainless steel rollers ensures that materials are cut accurately and efficiently, ready for further processing.
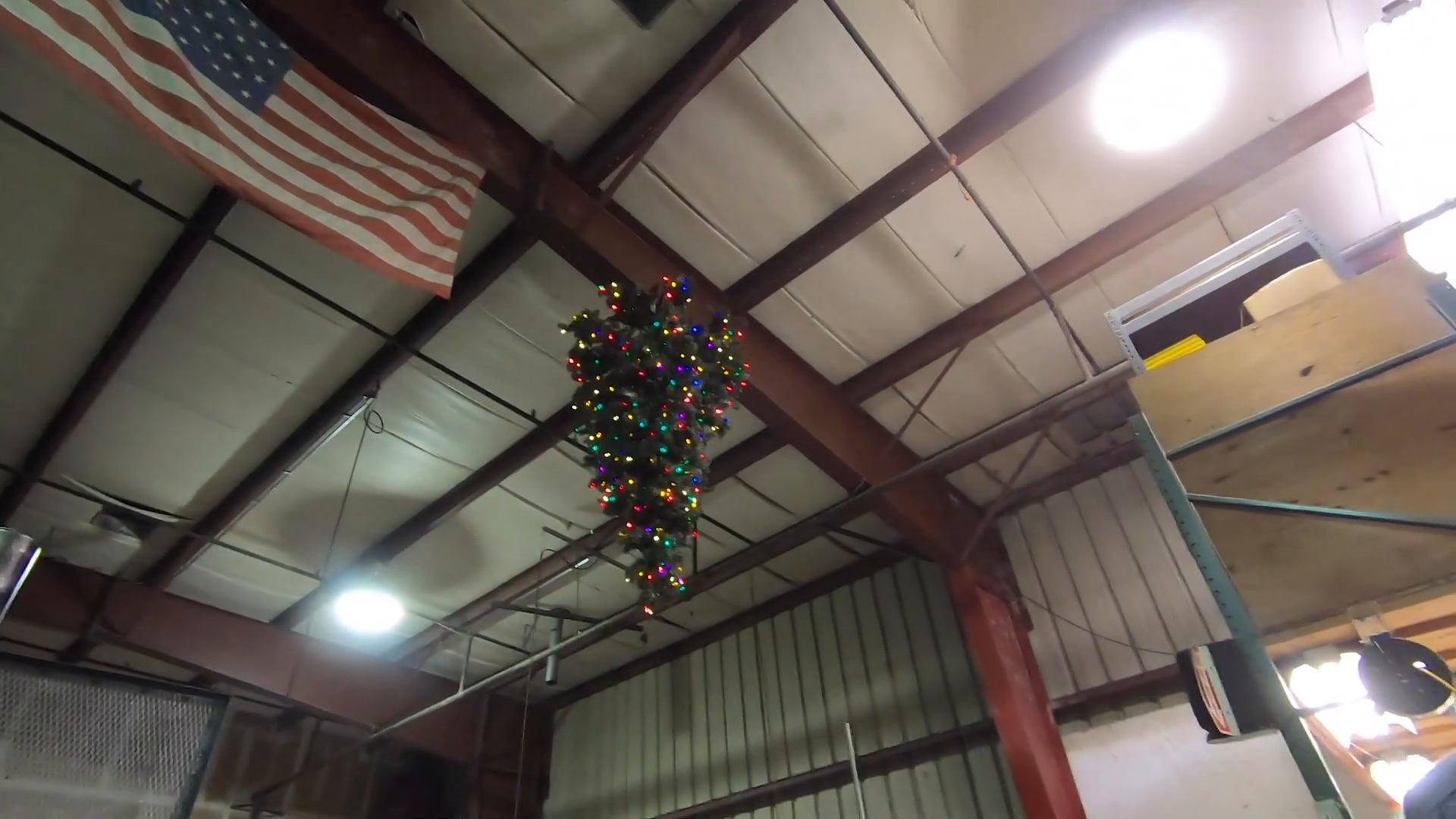
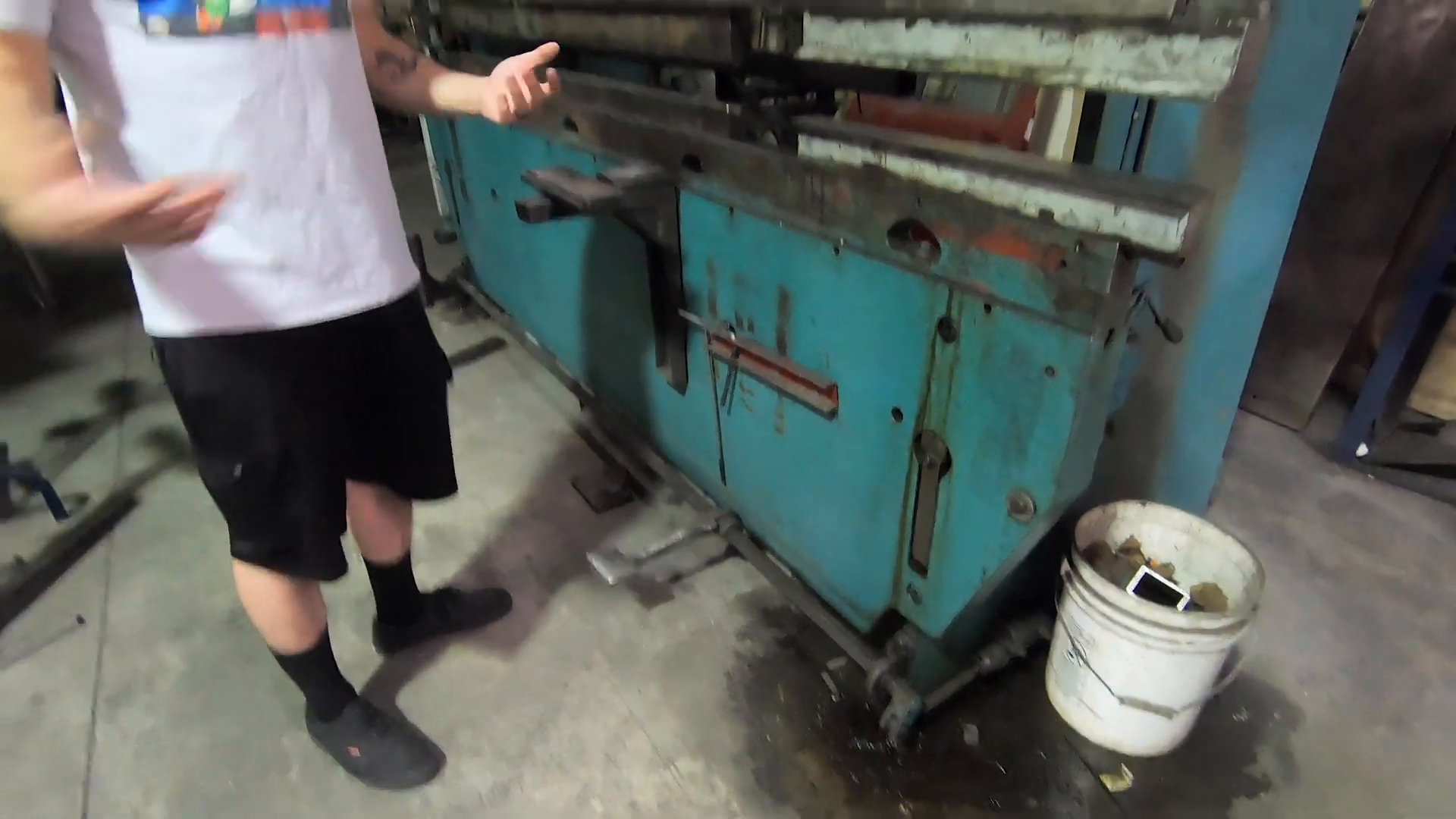
Grinding and Deburring
The shop includes dedicated stations for grinding and deburring, equipped with belts and disc sanders reserved for mild and stainless steel. This separation of materials prevents cross-contamination, preserving the integrity of each project. Additionally, a buff wheel is on hand for deburring sharp edges, primarily on stainless steel components, while maintaining a keen edge on tungsten used in welding.
Advanced Machinery for Precision Fabrication
Jig Tables and Innovative Solutions
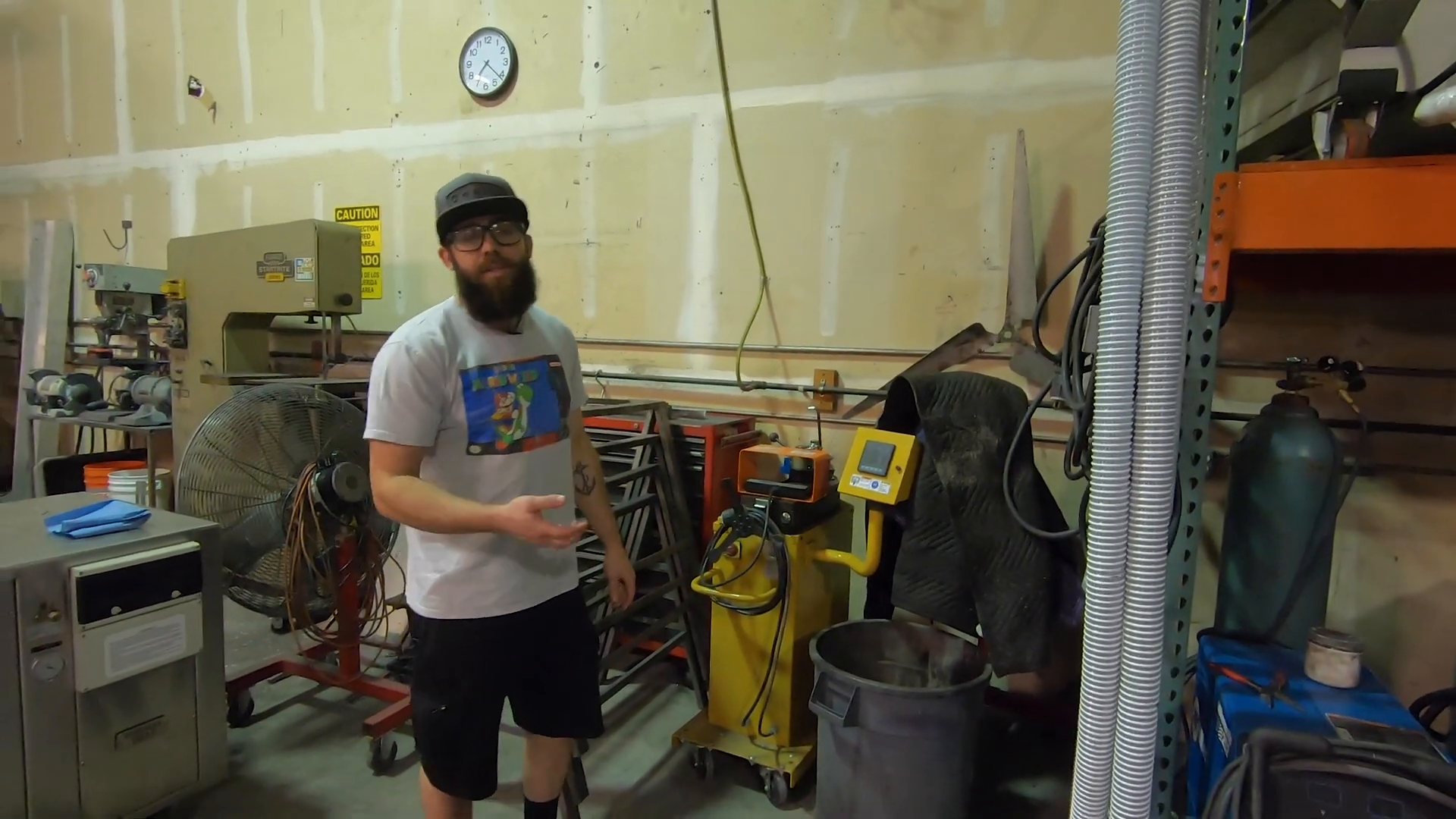
Central to the shop’s operations is a versatile jig table. This tool is essential for maintaining the accuracy of fabricated parts, ensuring each project is built to exact specifications. The table’s integrated grounding system simplifies welding operations, removing excess cables from the workspace and enhancing safety and efficiency.
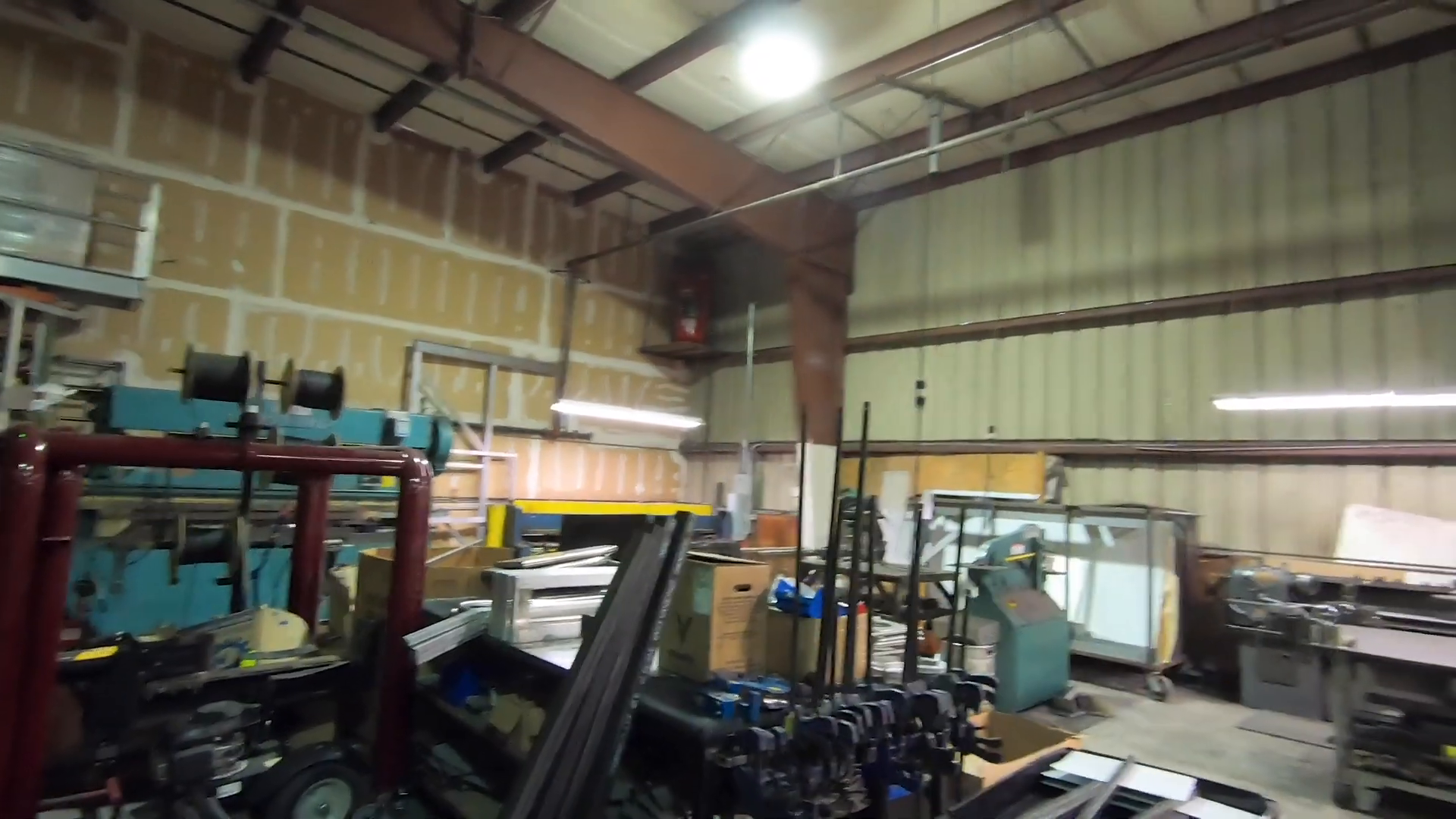
Vertical Mill and Lathes
A key piece of equipment in the shop is the Enco mill, used extensively for drilling and machining tasks. This mill, along with a lathe, provides the capability to create precise holes and cope tubes for various components. Although machining is not the shop’s primary focus, having these tools available is invaluable for specific projects that demand intricate work.
Shearing and Bending: The Backbone of Fabrication
Ten-Foot Shear and Press Brake
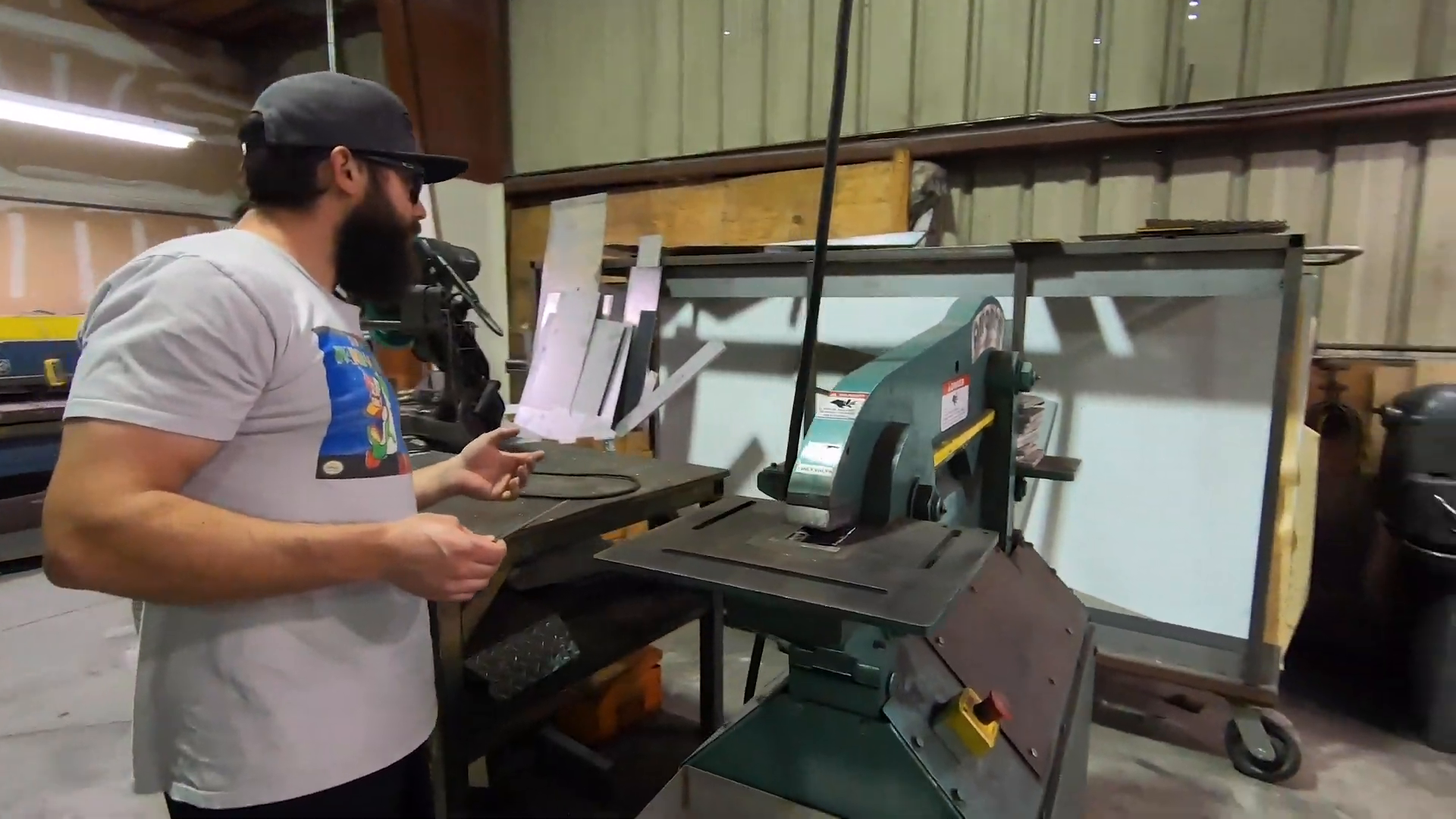
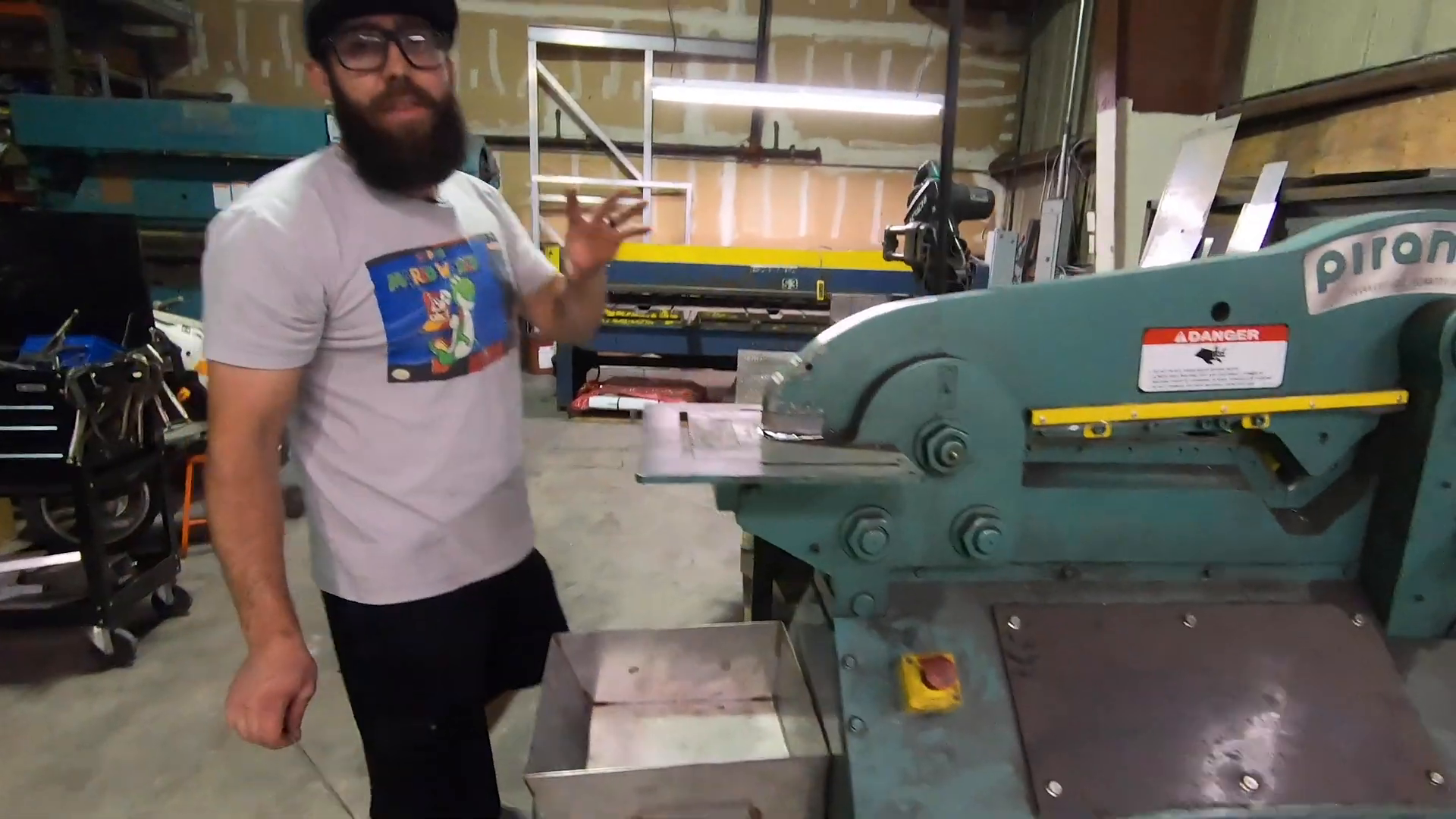
The shop features a robust ten-foot shear capable of cutting up to ten-gauge steel. This machine streamlines the preparation of materials for further fabrication, facilitating rapid and accurate cuts. Complementing the shear is a press brake equipped with multiple dies, enabling the bending of parts and brackets with precision. Despite its age and customization, the press brake remains a reliable workhorse.
Slip Roll and Ironworker
For projects requiring rolled sheet metal, the shop houses a four-foot slip roll. Though not frequently used, this tool is invaluable for creating smooth, rounded corners on metal panels. The Piranha ironworker further enhances the shop’s capabilities, allowing for quick and efficient cuts on thick metal, significantly reducing manual labor and time.
Modern Enhancements and Reliable Machinery
Tubing Bender and Welding Machines
The shop’s tubing bender, an RBD 250 from Bailey, is a crucial tool for creating consistent bends in metal tubing. Its programmable interface simplifies the bending process, ensuring accurate and repeatable results. Additionally, the shop is equipped with Miller Matic 252 wire feed welders, set up for both mild and stainless steel, and ready for aluminum projects when needed.

Compressed Air and Miscellaneous Tools
Two air compressors, including an Ingersoll Rand and a Husky model, supply the shop’s pneumatic needs. These compressors are strategically positioned to minimize noise while providing a steady supply of air for various tools. Miscellaneous tools and hardware are organized efficiently, allowing fabricators to focus on their work without unnecessary interruptions.
The Role of Innovation and Tradition in Modern Fabrication
The fabrication shop highlighted here exemplifies a blend of innovation and tradition in metalworking. With a mix of modern machinery and reliable, time-tested tools, the shop is well-equipped to handle diverse projects. The skilled team demonstrates adaptability and efficiency, meeting the demands of both creative and functional fabrication tasks. Through continuous learning and application of advanced techniques, the shop maintains its reputation as a leader in the fabrication industry.
While the shop’s primary focus is on wine industry components and vehicle modifications, its capabilities extend far beyond these specialties. The dedication to craftsmanship and quality is evident in every project, ensuring the shop remains a valuable asset to its clients and a testament to the possibilities of modern fabrication.
Categorized in: Trucks