Ranger Prerunner Build Part 3: Fuel Cell Cradle and Shock Mount Innovations
Progress on the Ford Ranger Build
The ongoing transformation of the Ford Ranger into a highly customized vehicle continues to be an impressive endeavor. The latest update highlights significant progress in the project, showcasing advancements in the rear structure and overall framework. Key components have been meticulously crafted, and the process involves a blend of precision engineering and creative design. The build is particularly notable for its focus on structural integrity and aesthetic appeal.
Building the Fuel Cell Cradle
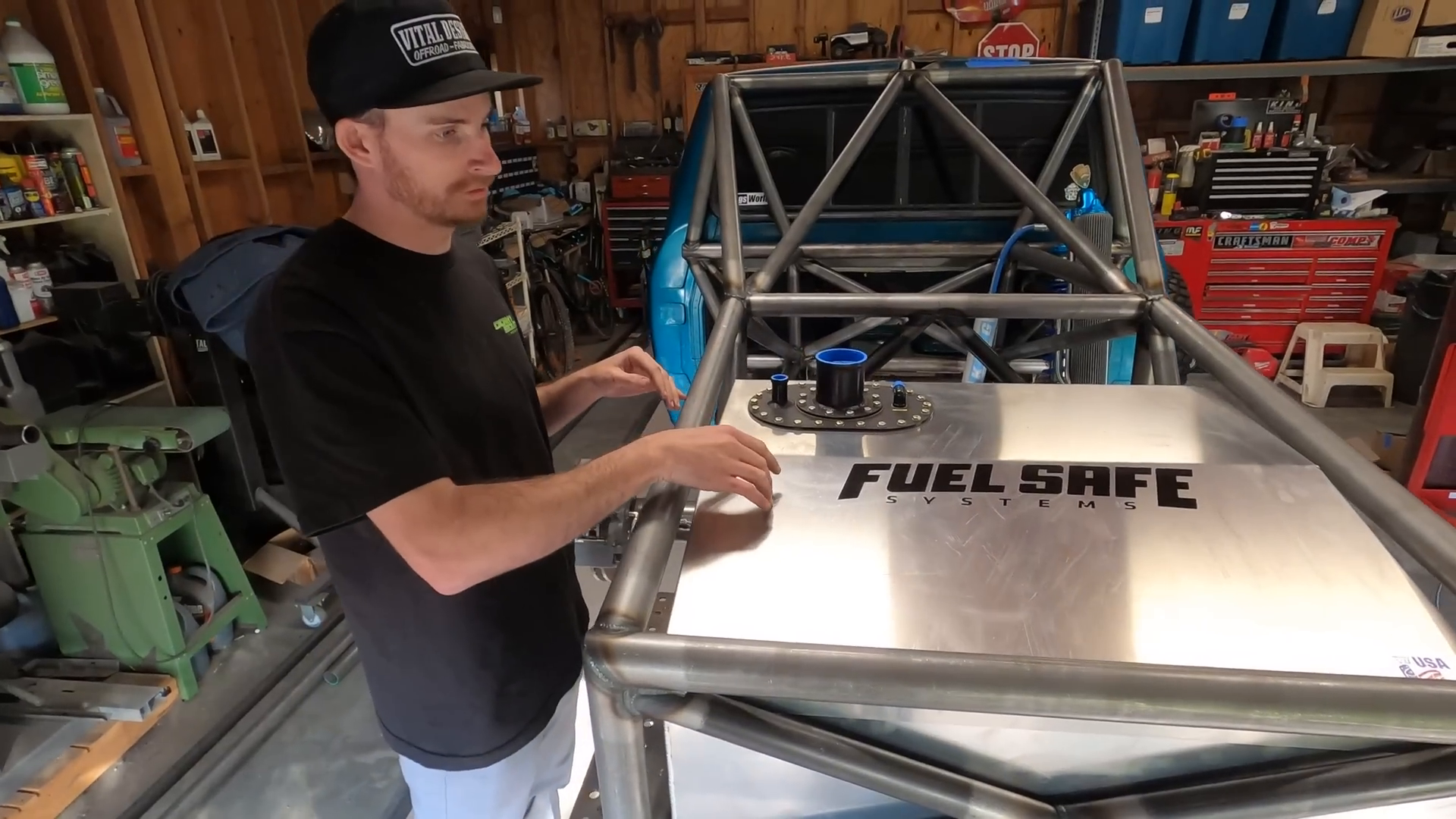
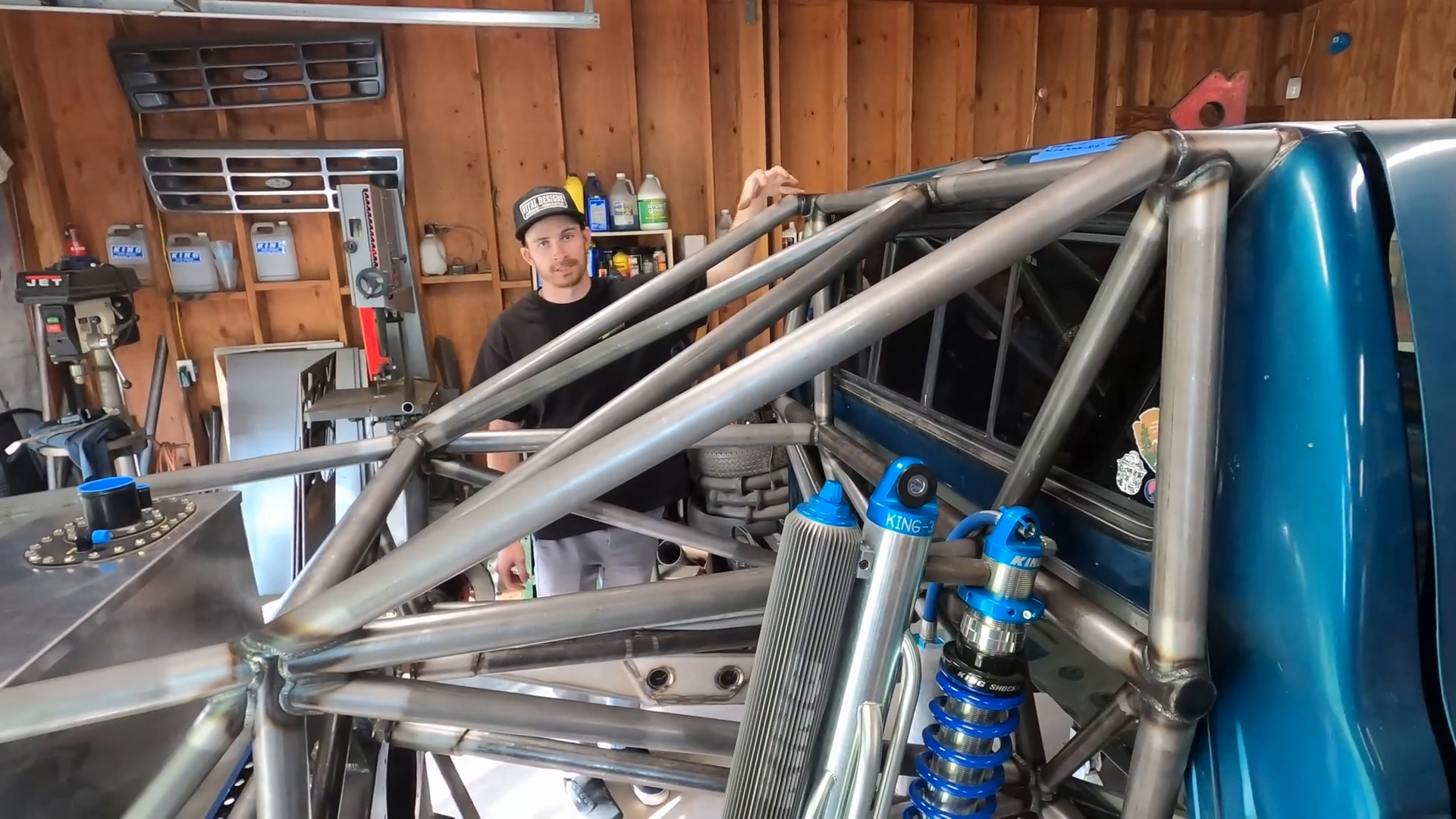
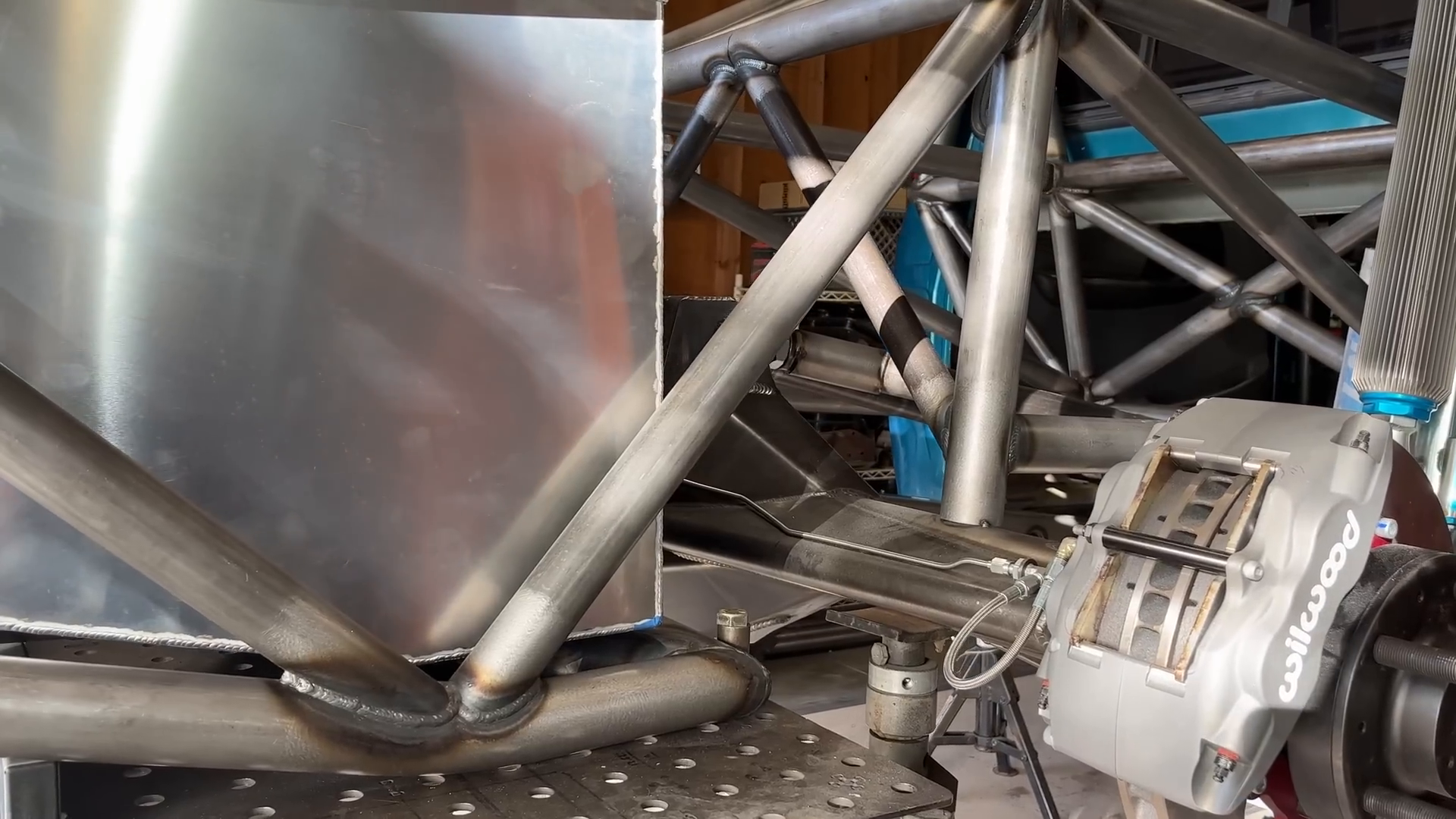
Design and Construction
The recent work has been centered around constructing a fuel cell cradle. The base of this component was initially crafted on a workbench with the fuel cell placed upside down. This method ensured that the structure was precisely tailored to fit the unique shape of the fuel cell. A notable feature is the inclusion of a single tube with a bend, aligned to the fuel cell’s profile, offering a clean and strong design.
Structural Considerations
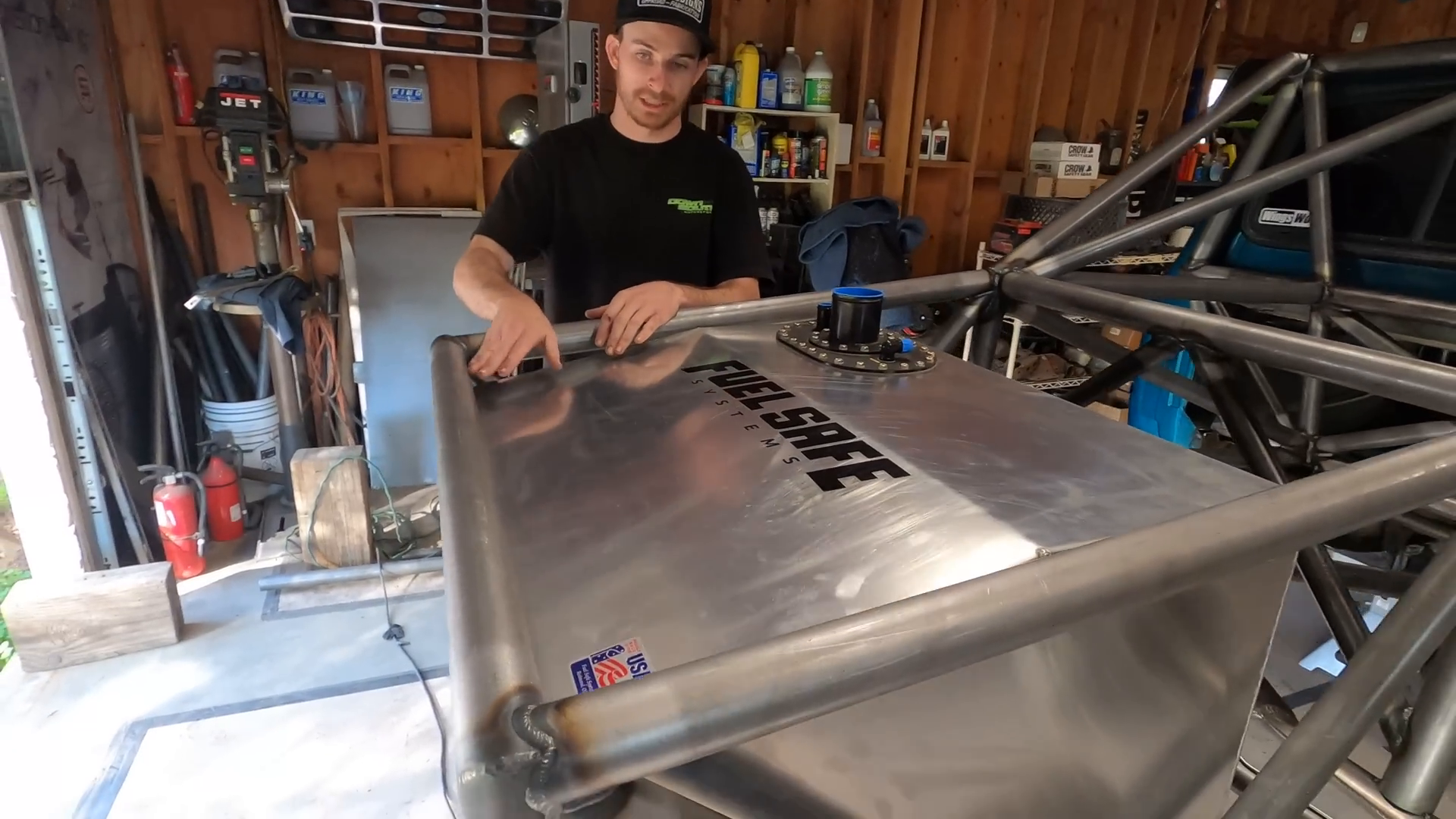
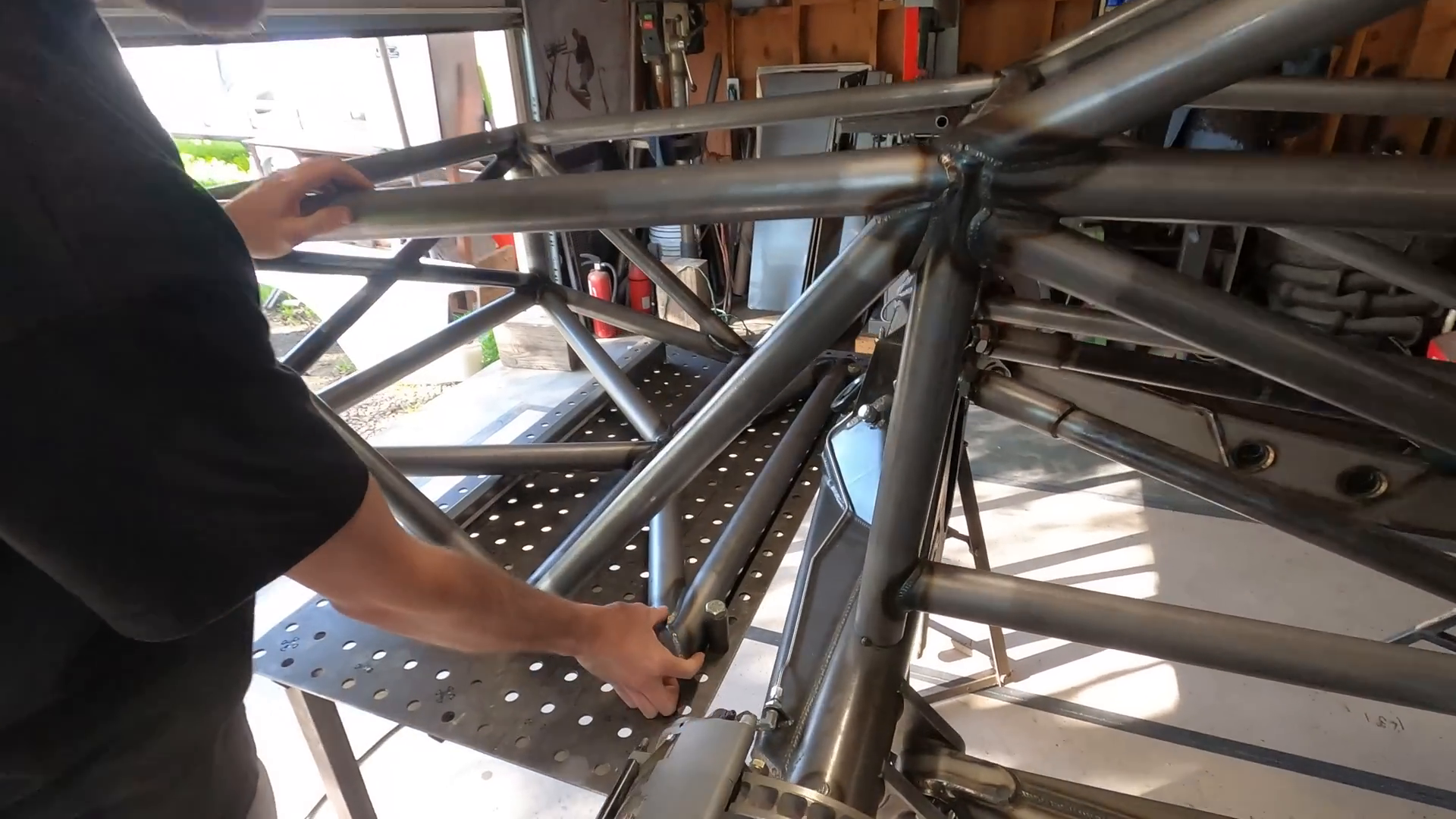
In crafting the fuel cell cradle, emphasis was placed on using miters rather than open-ended tubes. This approach not only enhances the visual appeal but also strengthens the structure. The integration of closed-off miters ensures a robust framework, which is crucial given the weight and load the cradle must support. This meticulous attention to structural details underscores the project’s commitment to both form and function.
Integration with the Chassis
Positioning and Alignment
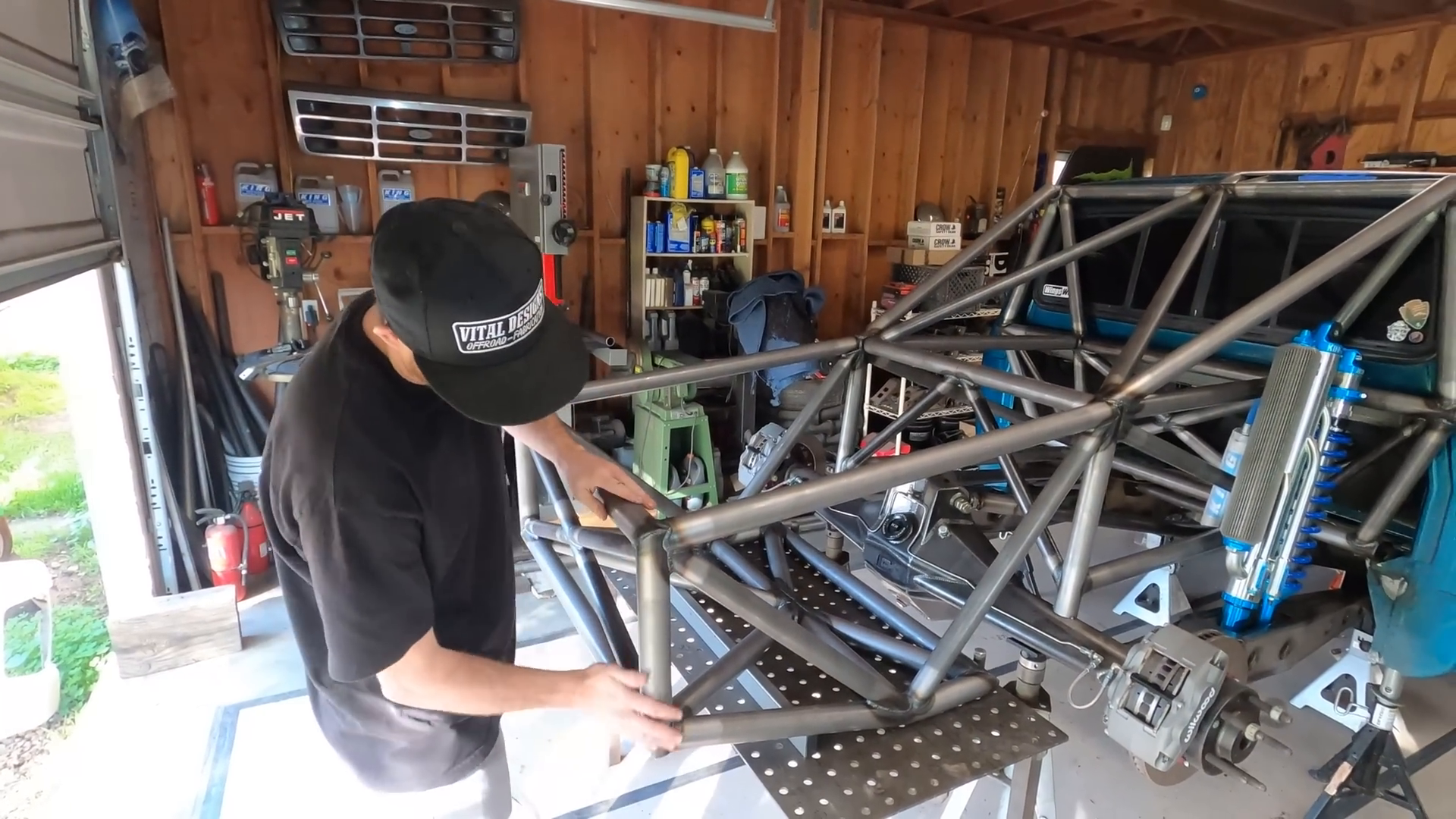
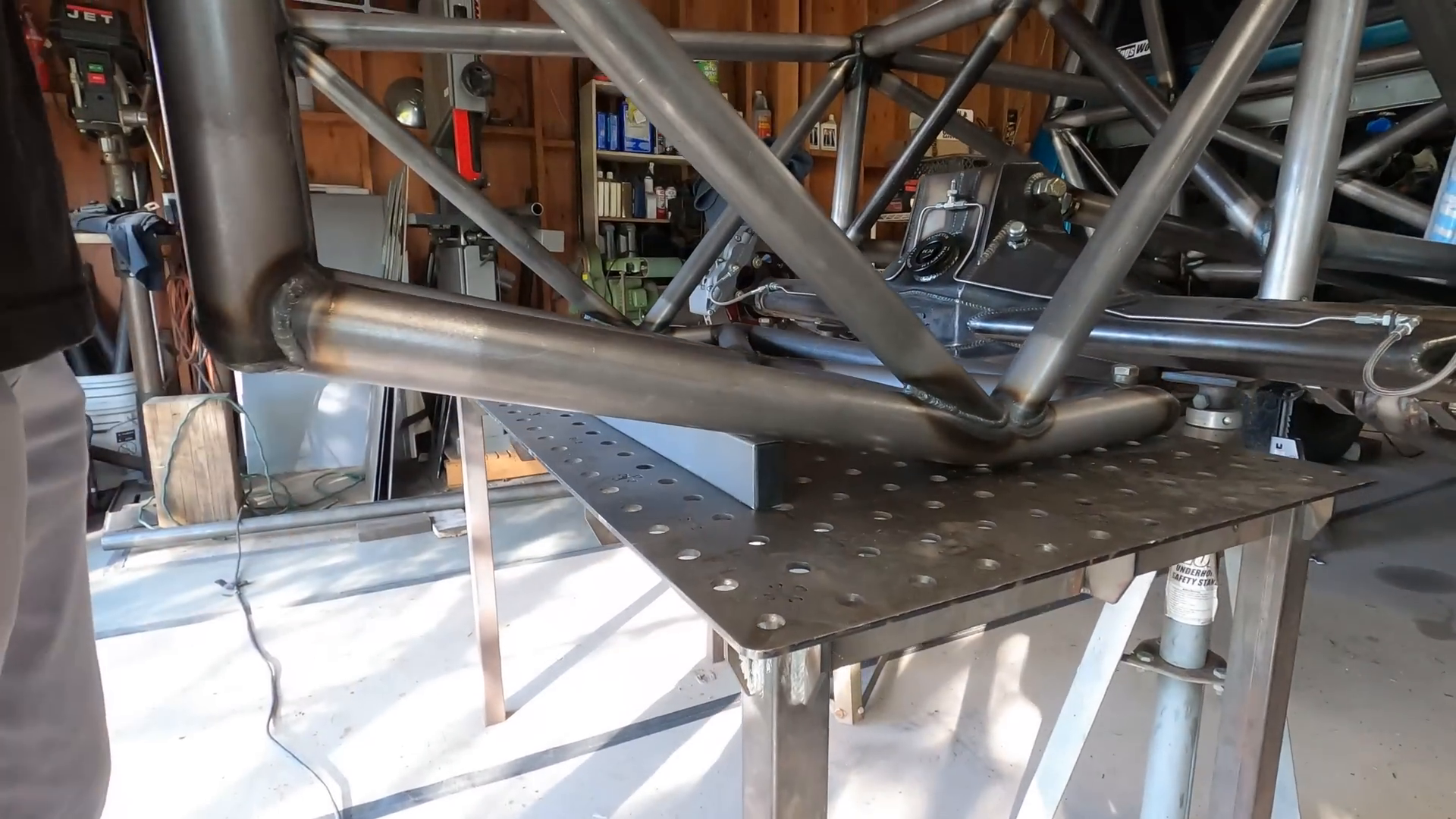
Positioning the fuel cell within the truck’s chassis required careful planning. Factors such as the wheelbase and the placement of the spare tire were taken into account to ensure that the vehicle’s proportions remained visually balanced. The fuel cell’s placement also facilitated the incorporation of auxiliary components, such as a jack, without compromising space or design integrity.
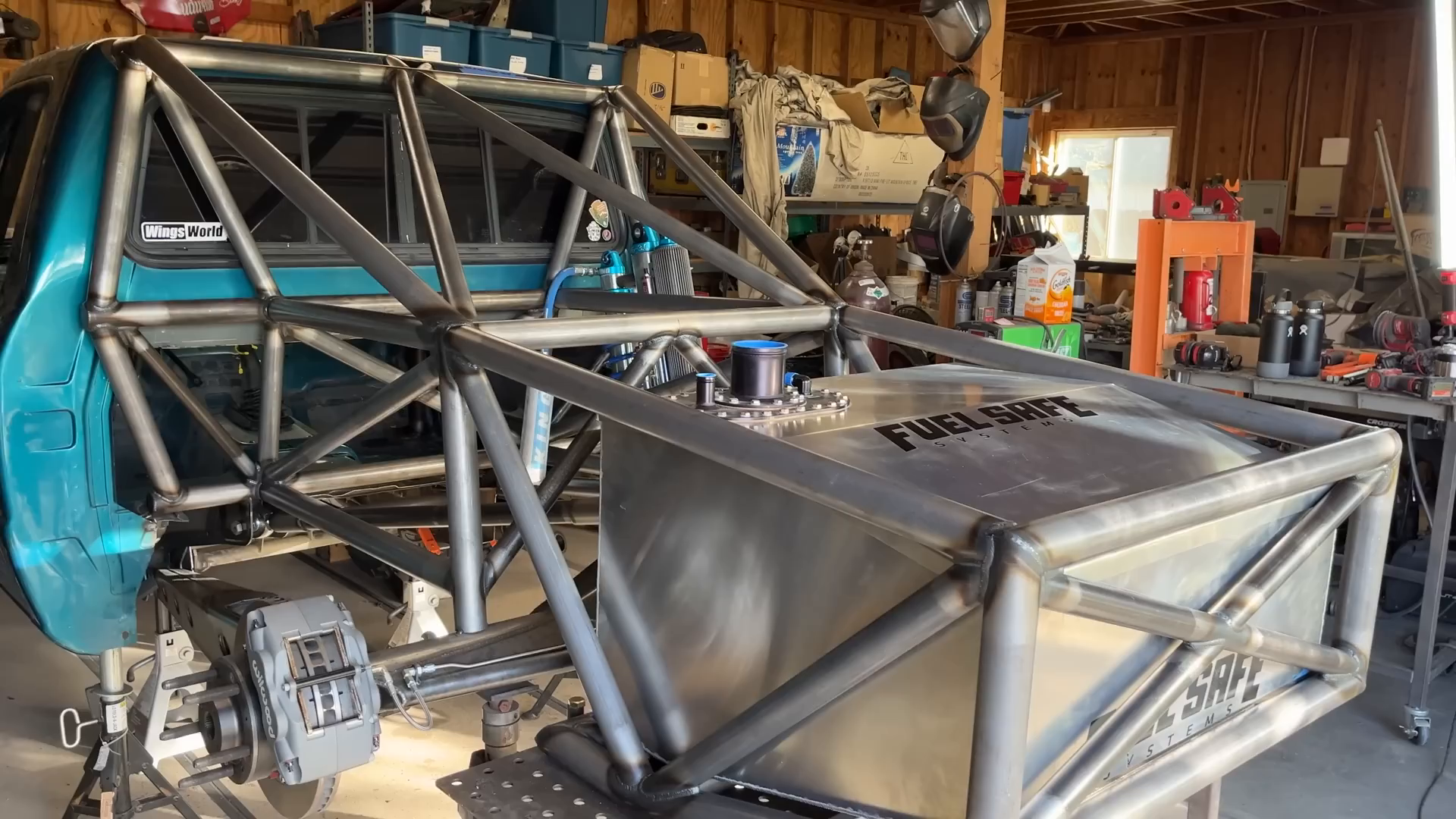
Connecting Sections
The integration of the fuel cell cradle into the truck’s chassis was achieved through strategic placement and alignment of various tubes. Each connection point was meticulously welded, ensuring a seamless transition between components. This careful attention to detail not only enhances the structural strength but also contributes to the overall aesthetic of the build. Additionally, the use of 3/16 plate work is planned to further reinforce the connection points.
Innovative Shock Mount Design
Mocking Up Shocks
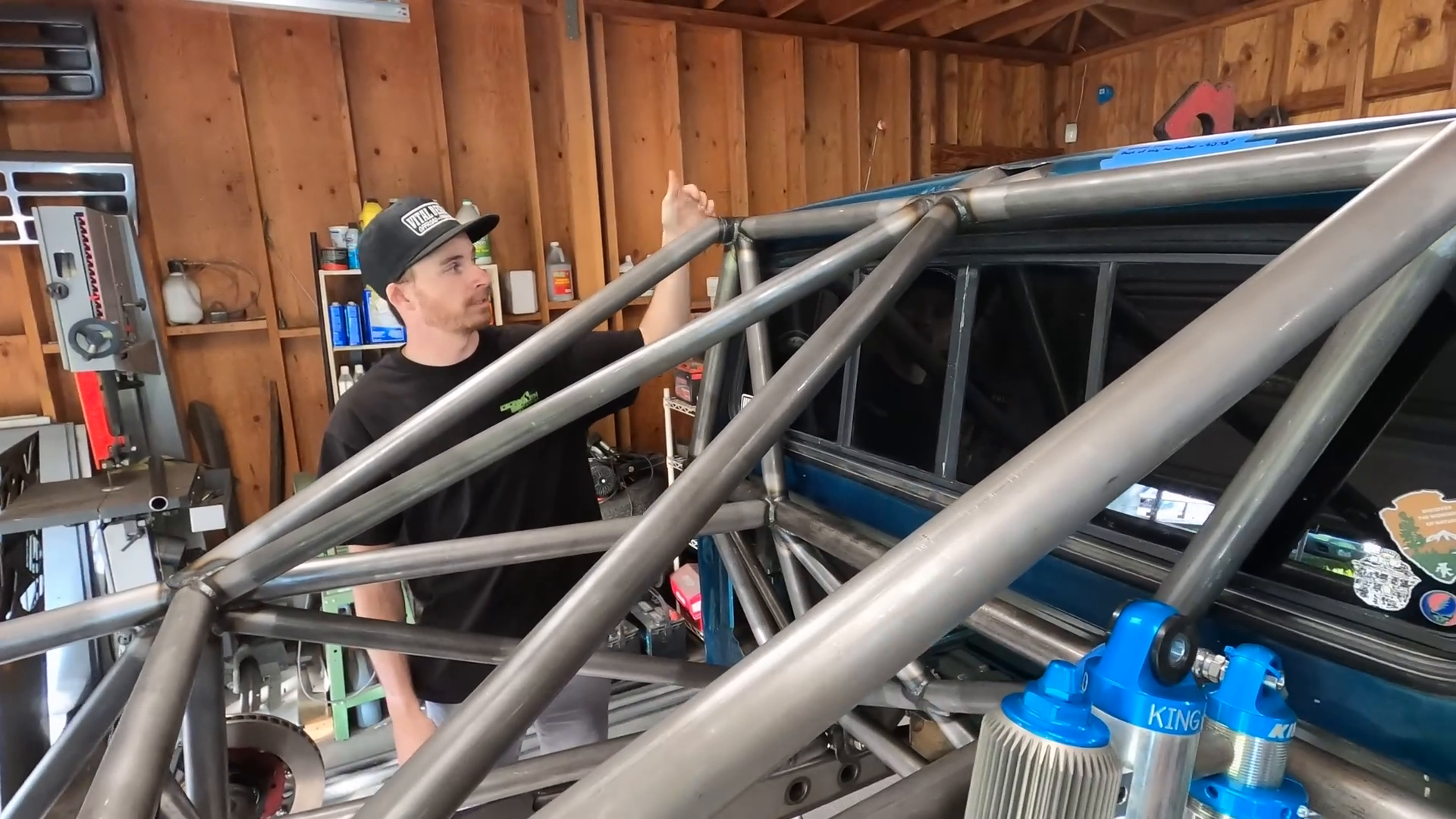
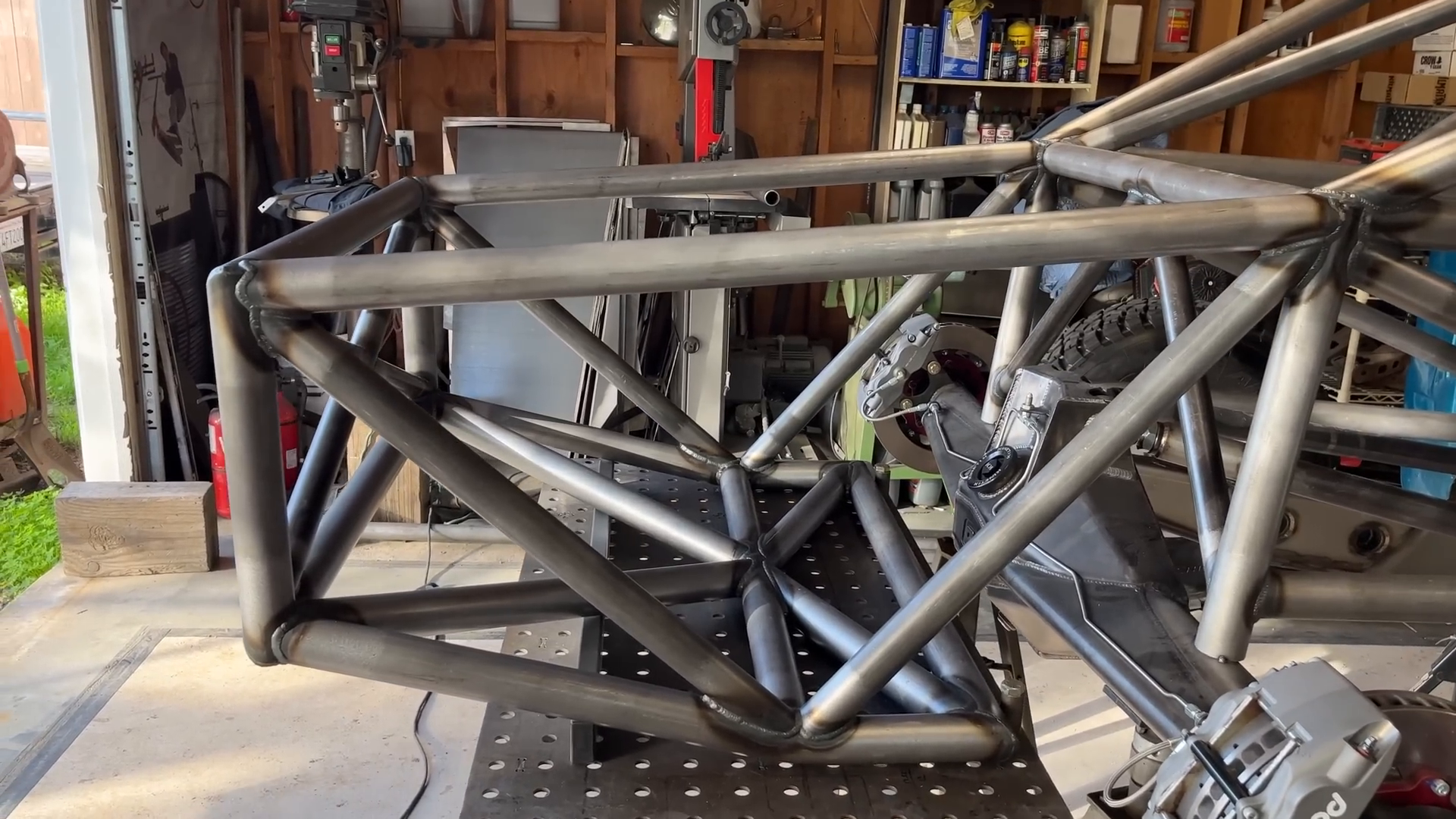
The process of incorporating shock mounts into the build required a strategic approach. The shocks were temporarily mocked up to assess the best placement for the mounts, which will be crucial for vehicle performance. The design considers both visual appeal and structural integrity, ensuring that the mounts will not only look good but also withstand the rigors of off-road use.
Structural Reinforcement
Once the shock mounts are in place, they will add another layer of structural reinforcement to the vehicle. The design of the mounts will ensure they tie into the existing framework seamlessly, providing additional support to handle the weight and stress of the vehicle’s suspension system. This reinforcement is critical, especially given the demands of high-performance driving conditions.
Progress and Challenges
Efficient Workflow
Despite the complex nature of the project, the build has progressed efficiently, with significant advancements made within a short timeframe. The meticulous planning and execution have allowed for rapid development, with key components pre-fabricated before the truck’s arrival. This efficient workflow has been instrumental in maintaining momentum and achieving milestones quickly.
Overcoming Design Hurdles
Throughout the build, several design challenges have been encountered and overcome. The unique demands of the project, coupled with the desire for a clean and robust design, have necessitated innovative solutions. Each challenge has been addressed with a combination of technical expertise and creative problem-solving, ensuring that the final product meets both functional and aesthetic goals.
The Importance of Customization in Vehicle Builds
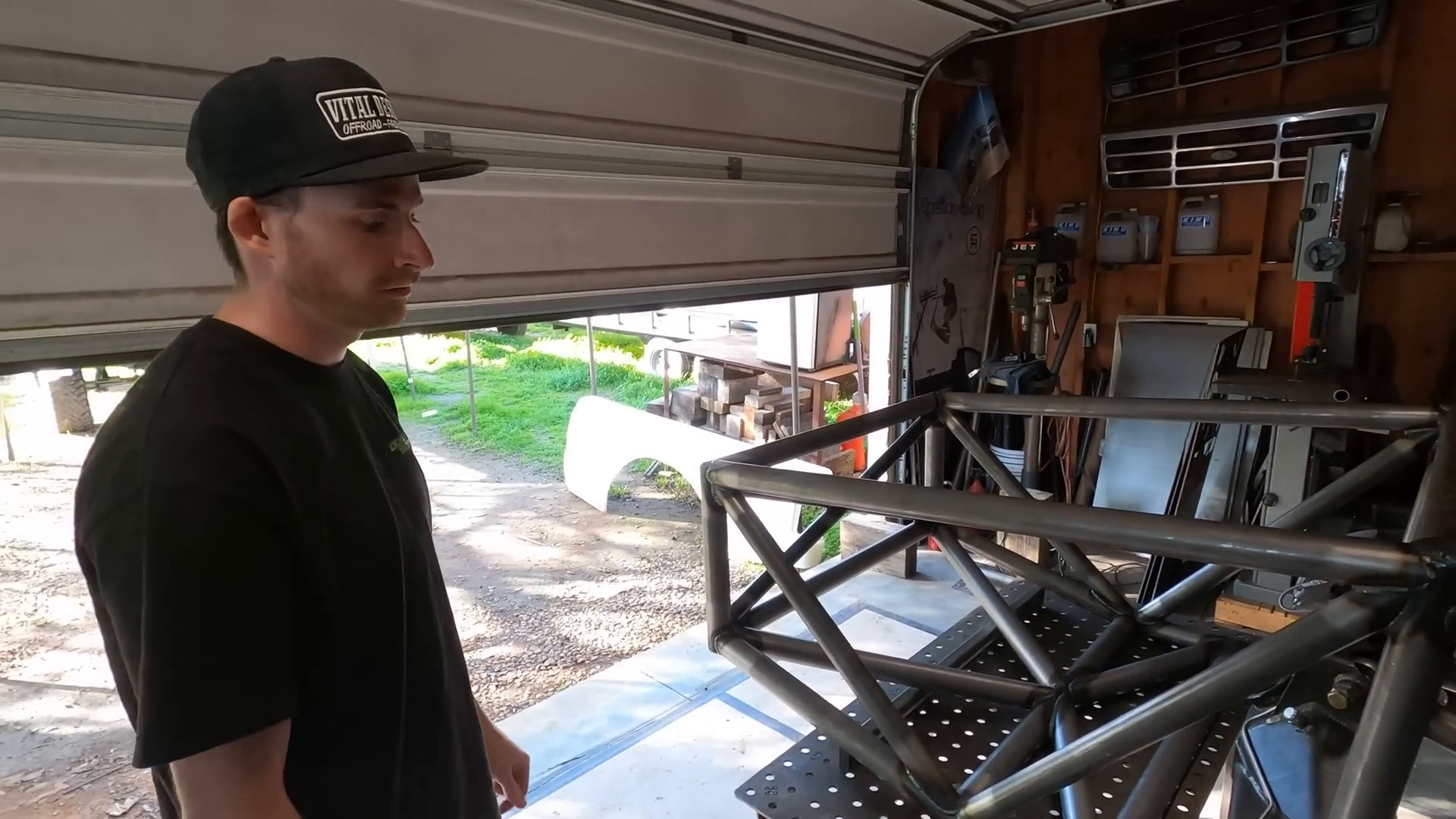
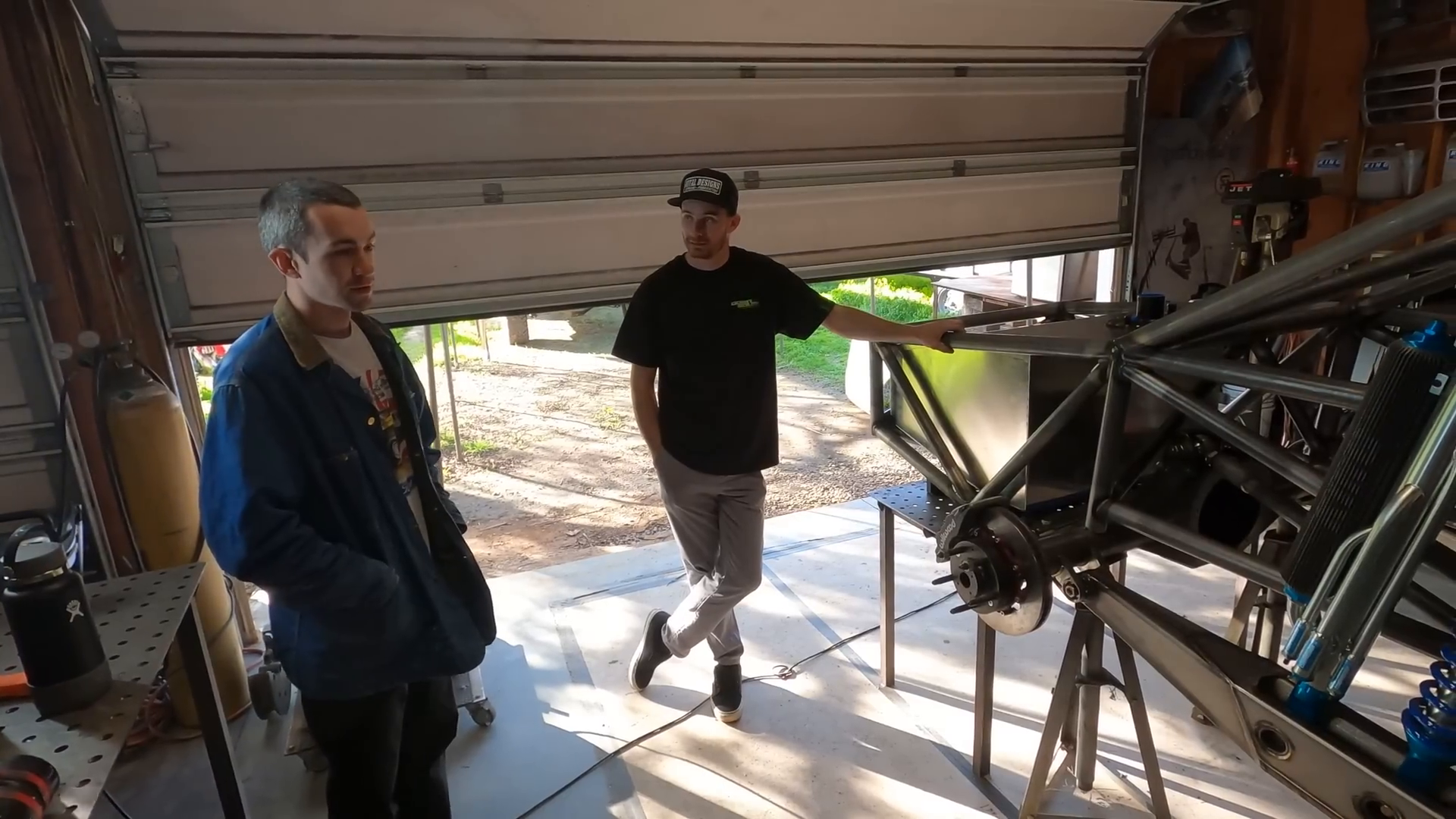
Vehicle customization is not just about creating a unique aesthetic; it’s about enhancing performance and utility. The Ford Ranger build exemplifies this by focusing on structural modifications that support additional weight and improve handling. Custom builds allow for tailored solutions that meet specific needs, such as off-road capabilities or increased payload capacity.
In the broader context of automotive customization, projects like the Ford Ranger build demonstrate the value of skilled craftsmanship and engineering. They highlight the importance of considering both visual design and structural integrity. Custom builds also provide a platform for innovation, allowing builders to experiment with new techniques and materials that can influence future automotive design.
As the Ford Ranger project progresses, it continues to set a benchmark for custom vehicle builds, showcasing what can be achieved when creativity and technical expertise are combined. The ongoing updates provide insight into the complexities and rewards of automotive customization, offering inspiration to builders and enthusiasts alike.
Categorized in: Fabrication, Ford, Prerunners, Trucks