1993 Ford Ranger Prerunner Swingset Steering
The focus of today’s build is a 1993 Ford Ranger, transformed into a prerunner, a type of off-road vehicle specifically designed to “pre-run” races. This entails building robust suspension systems and other components that can withstand the rigors of off-road racing. Recently, significant progress has been made, including the installation of frame plates and beam pivots, as well as constructing an engine cage. Painted beams and radius arms are temporarily removed, ready to be reinstalled after receiving a fresh coat of paint. Shock mounts and bump stops have been strategically placed, ensuring optimal travel and protection for the expensive suspension components. A removable crossmember above the engine allows for easy maintenance access. With these components in place, the stage is set for the next critical step: fabricating a custom single swing steering system.
Suspension and Steering System
Importance of Bump Stops and Limit Straps
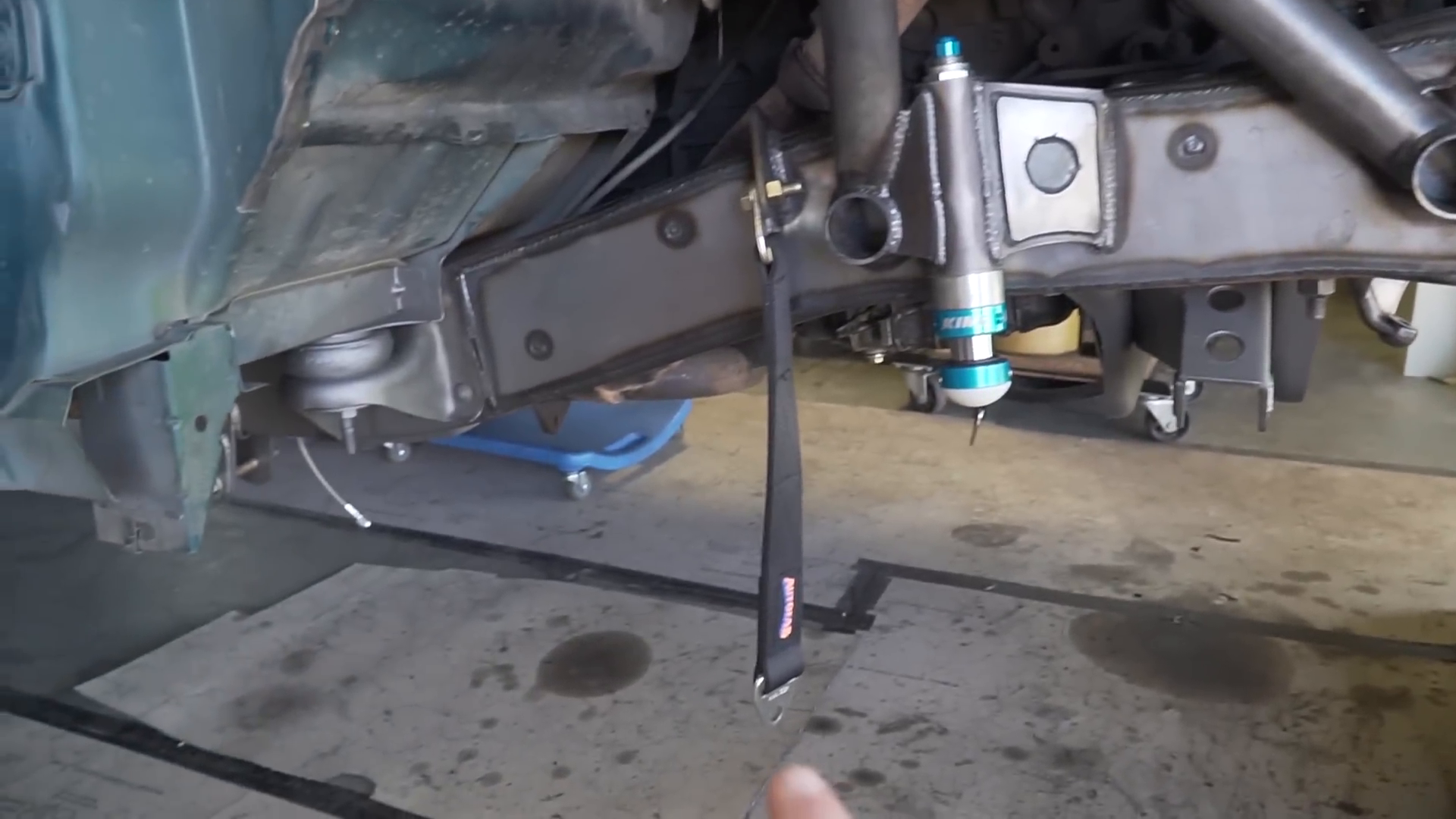
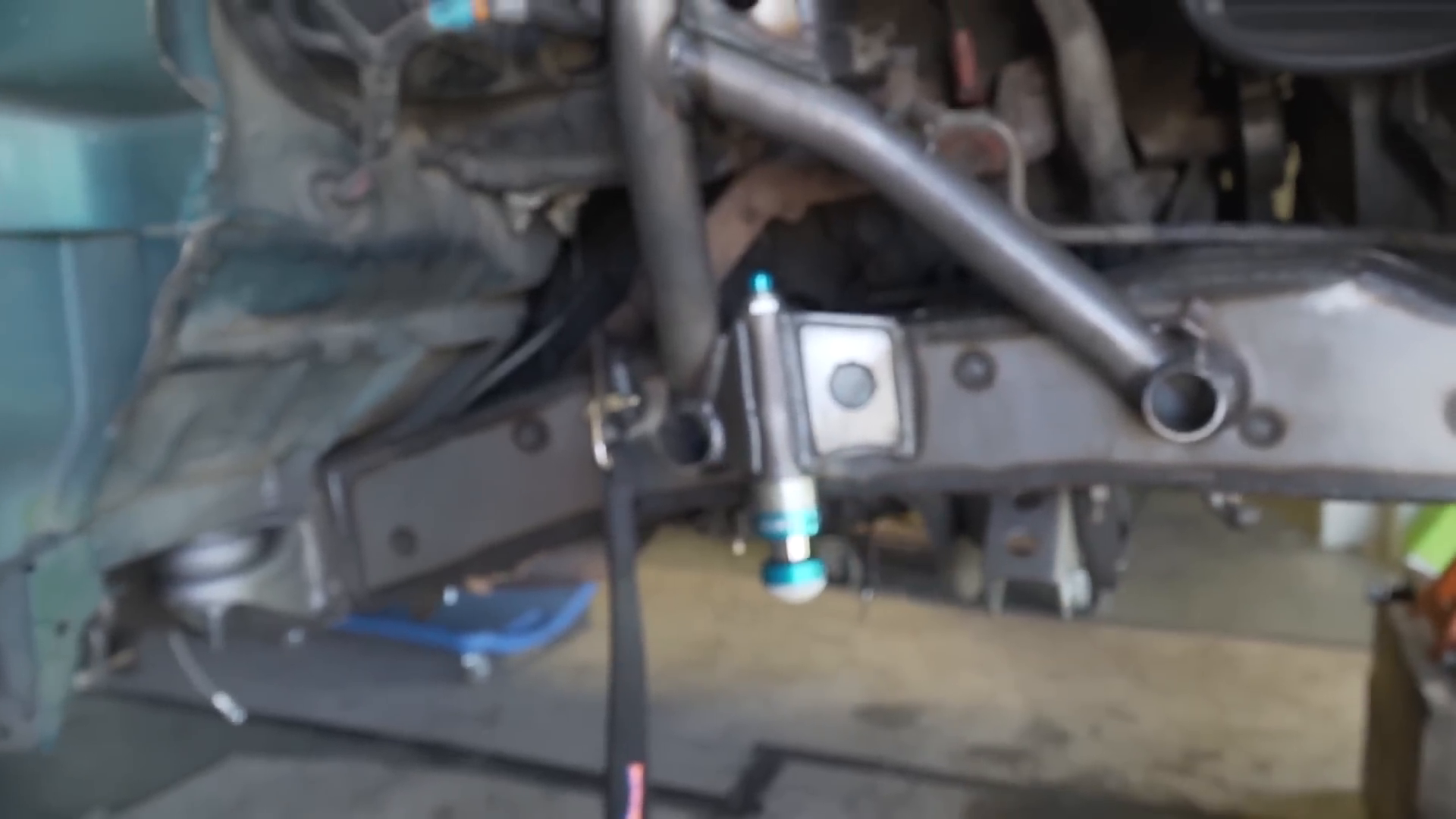
The Ranger’s suspension has been upgraded to achieve impressive travel numbers, cycling around 18 inches without bump stops and limit straps. However, these components are essential in preventing damage to shocks by cushioning full compression and restricting over-extension. This ensures the longevity and performance of the suspension while driving off-road. This setup exemplifies the importance of meticulous planning and execution in a prerunner build.
Custom Single Swing Steering Build
Creating a single swing steering system involves designing a unique steering mechanism tailored for this Ranger. Using templates and custom parts, the builder plans to construct a steering setup that integrates with the existing suspension. The process includes using two-inch 250-wall tubing and bronze bushings, with a pre-made pitman arm that suits various Ford models. The steering system’s layout involves connecting the dots from the pitman arm to the swinger, and finally to the tie rods and wheels. This intricate process highlights the complexity and customization involved in off-road vehicle builds.
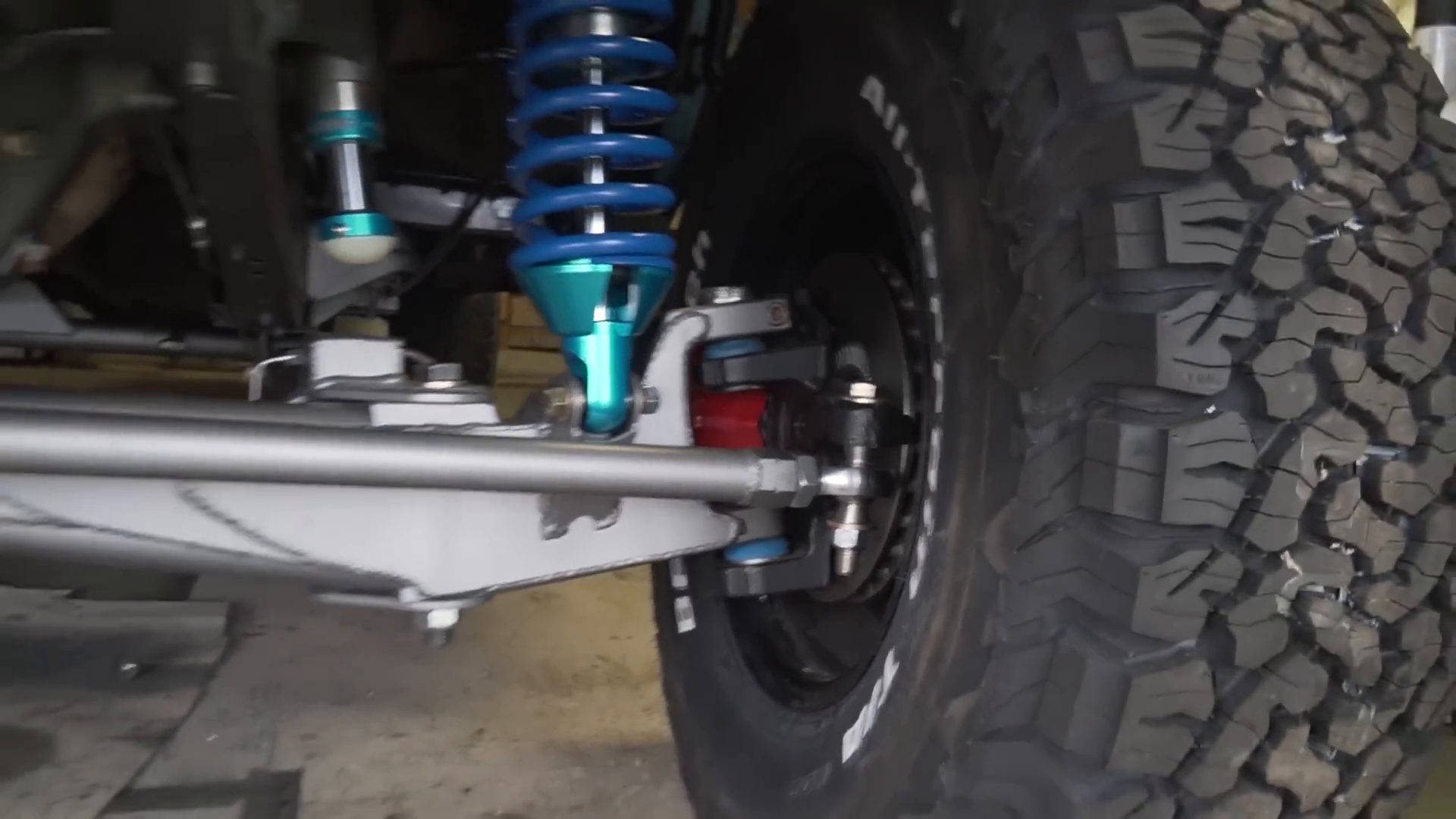
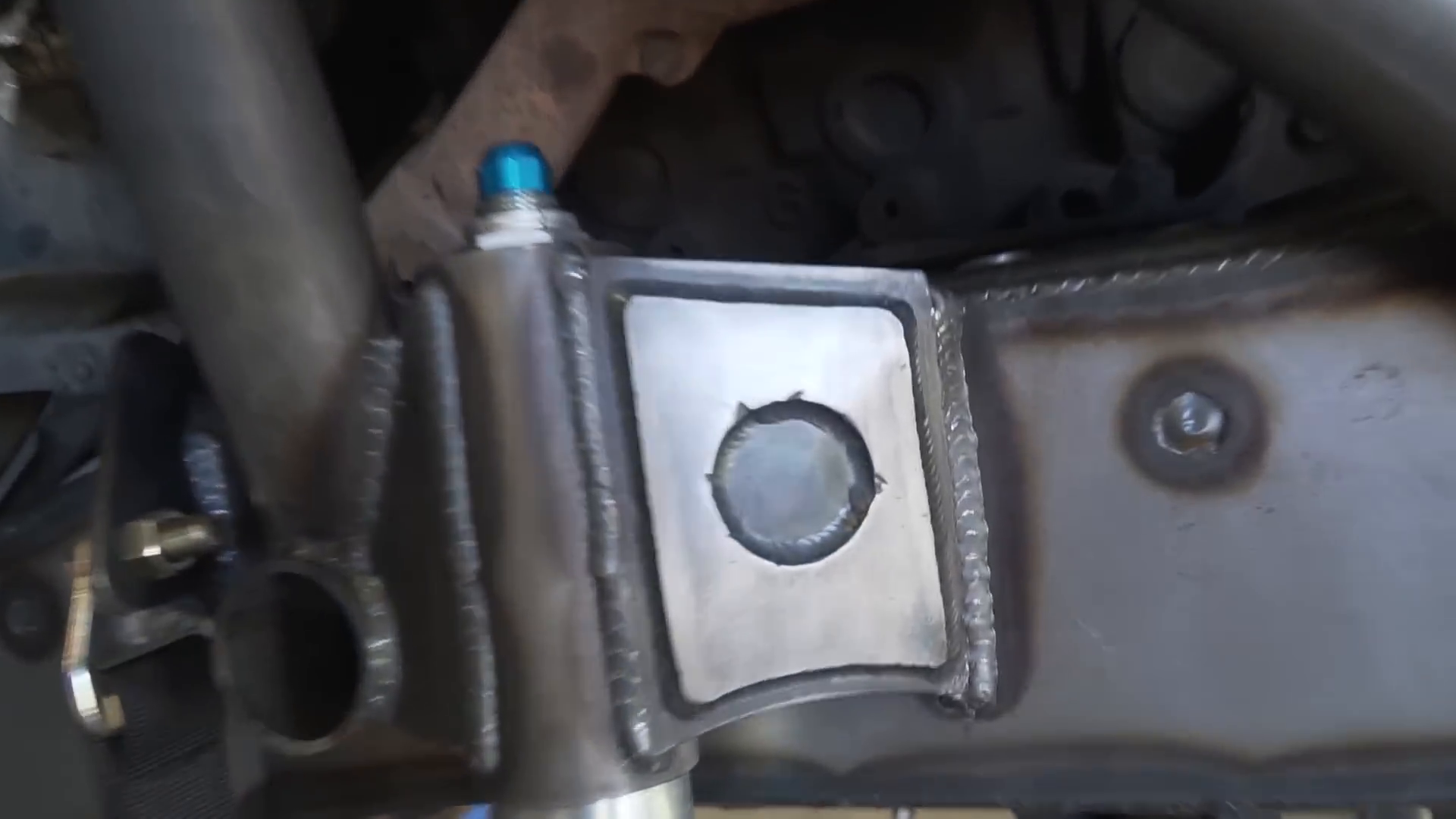
Fabrication Techniques and Tools
Mocking Up Tie Rods
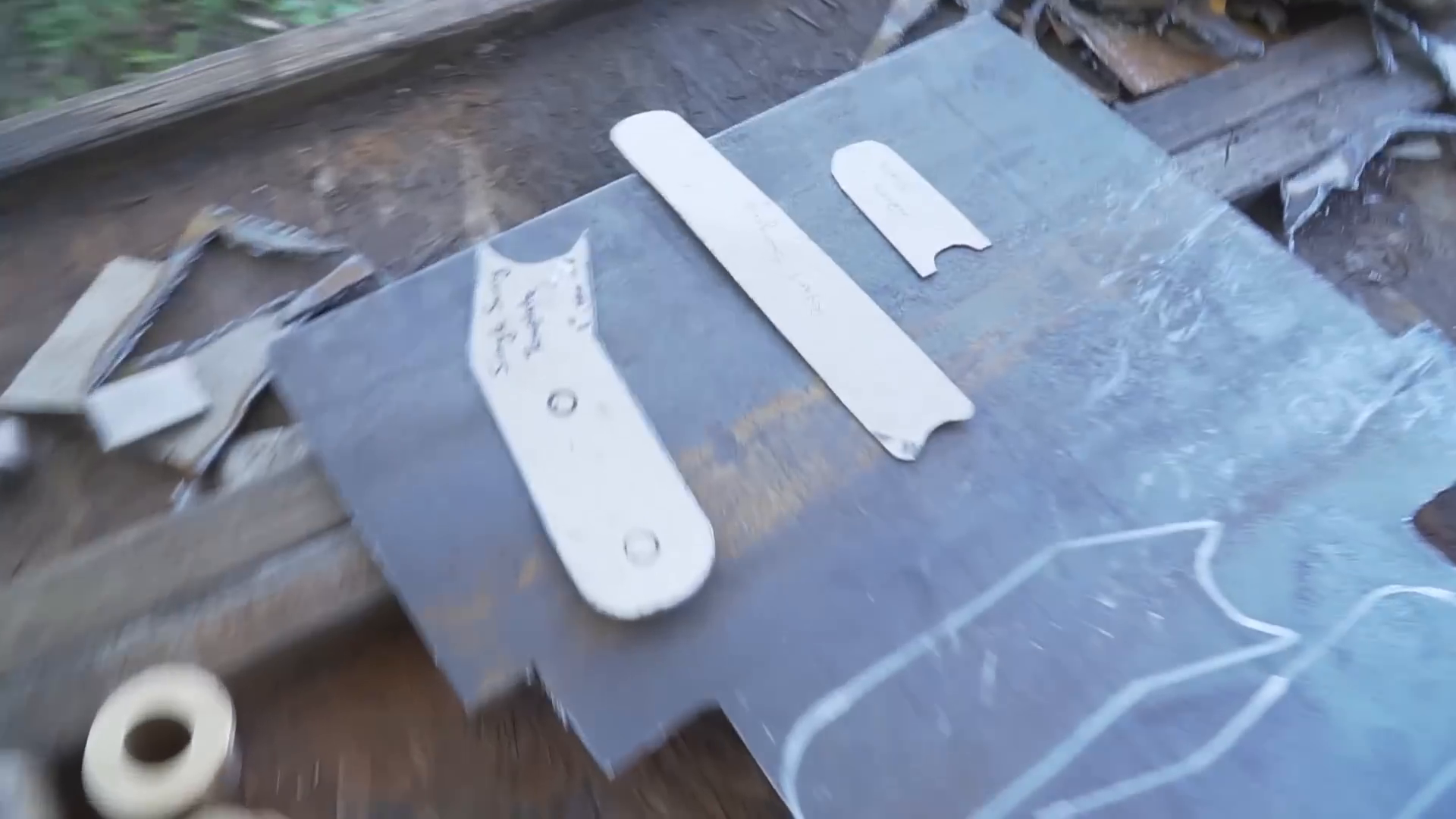
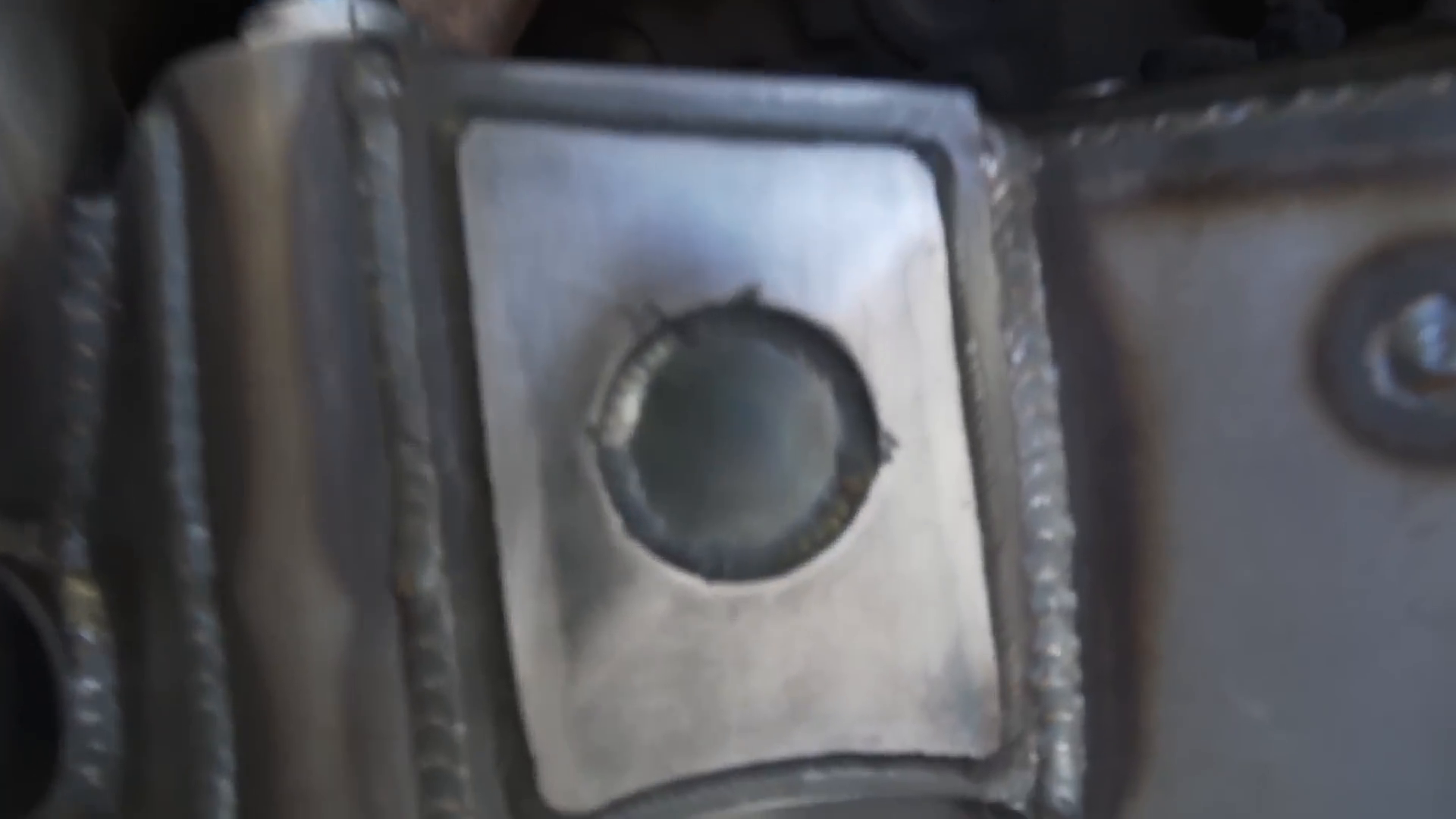
To ensure precision, electrical metallic tubing is used to mock up tie rods. This cost-effective method allows for adjustments and alterations before committing to expensive materials. Unlike PVC, this tubing can withstand bending, making it an ideal choice for simulating real-world scenarios. The tubing is galvanized, which requires caution during tack welding to avoid inhaling harmful fumes. This mock-up phase is crucial for visualizing and testing the steering geometry before final assembly.
Alignment Challenges and Solutions
With custom steering setups like this, traditional alignment shops are often not equipped to handle the unique requirements. The builder devised a homemade alignment tool to set the toe correctly, ensuring the vehicle drives straight on the road. By using a 35-inch piece of tubing and precise measurements, a quarter-inch toe-in is achieved, a common setting for off-road vehicles that helps maintain stability at speed. This DIY approach to alignment underscores the need for resourcefulness and innovation in custom builds.
Final Assembly and Testing
Reassembly and Painting
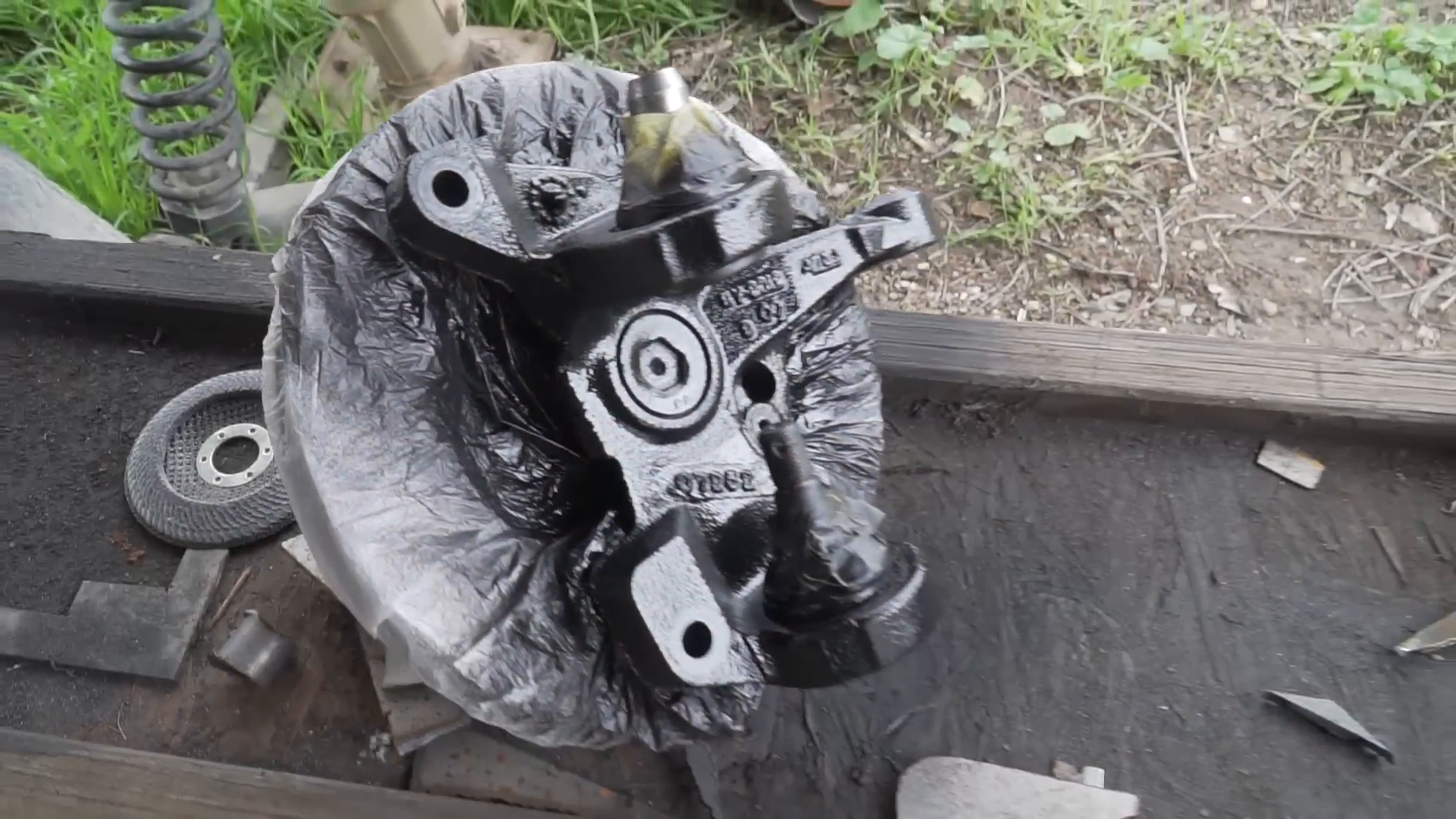
After mocking up the steering, the beams and radius arms are reinstalled, and the spindles receive a fresh coat of paint. These final touches might seem minor, but they contribute to the overall aesthetics and durability of the build. The attention to detail is evident in every aspect of the assembly, from ensuring proper hardware tightness to aligning the vehicle correctly.
Project Completion Goals
The builder faces a tight deadline, aiming to complete the project by March 1st. Upcoming tasks include fabricating the front bumper, fitting fenders, and modifying bed sides to accommodate larger tires. This timeline underscores the challenges of balancing meticulous craftsmanship with time constraints, a common scenario in custom automotive projects.
Broader Context and Implications
The modifications being undertaken on this 1993 Ranger reflect a broader trend in automotive customization, where enthusiasts push the boundaries of design and performance. Prerunner builds, in particular, are gaining popularity for their ability to transform standard vehicles into off-road powerhouses. Such projects often require a deep understanding of engineering principles, a blend of creativity and technical skill, and a willingness to experiment with unconventional solutions. Moreover, as off-road racing and recreational activities continue to grow, the demand for capable and reliable vehicles drives innovation in the industry. This Ranger build is a testament to the passion and dedication of those who engage in automotive customization, showcasing what is possible with vision, skill, and a willingness to tackle complex challenges.
Categorized in: Fabrication, Ford, Trucks